19 Equations of Fluid Motion
Introduction
Solving problems in fluid dynamics and aerodynamics requires setting up the appropriate mathematical models of the flow field correctly. The derivation of the mathematical equations that describe fluid dynamics and aerodynamic flows is relatively straightforward because it is a systematic process that has become well-established in engineering practice. However, all practical problems will inevitably require some assumptions and approximations to the equations to obtain solutions; a common and valid assumption is that air behaves as an ideal gas. Other assumptions include two-dimensional, steady, inviscid, and incompressible flow. Part of the skill in solving problems in fluid dynamics and aerodynamics is understanding what reference frames and sets or subsets of equations are needed.
Learning Objectives
- Understand how the conservation principles are applied to solve fluid dynamic and aerodynamic problems.
- Appreciate the various types of flow models that can be used to solve fluid problems.
- Understand the concepts of mass flux and mass flow.
- Know how to set up a finite control volume model of a fluid flow.
- Appreciate how the Reynolds Transport Equation (RTE) is derived and its uses.
Setting Up Flow Models
Setting up flow models in fluid dynamics and aerodynamics involves creating mathematical representations of fluid behavior to analyze and predict fluid flow patterns such as streamlines, pressures, velocities, and other related parameters. These flow models are a foundation for understanding and solving real-world engineering problems in aerospace engineering and other disciplines.
- Problem Definition: The first step is to clearly define the problem to be solved, which inevitably raises additional questions. Try to identify the type of fluid flow – is it incompressible or compressible, steady or unsteady, laminar or turbulent? What is the geometry of the fluid system, the boundary conditions, and the desired outcomes, e.g., flow rates, flow, velocities, pressure distributions, etc.?
- Governing Equations: Select the appropriate governing equations likely to describe fluid flow behavior. These typically include the continuity, momentum, and energy equations. If justified, additional equations, such as the equation of state, may be applied to specific problems.
- Assumptions and Simplifications: Make any assumptions and simplifications that might reduce the complexity of the equations while ensuring that they remain relevant to the problem. Typical assumptions include neglecting specific forces (e.g., viscosity) or considering steady-state conditions.
- Boundary Conditions: Specify appropriate boundary conditions at the system’s boundaries. These conditions can include prescribed velocities, pressures, temperatures, and any other relevant parameters. Boundary conditions will be crucial in determining the fluid’s behavior within and outside the system.
- Post-Processing: Analyze the results obtained from the flow model. If needed, generate plots, tables, and other visualizations to gain insights into the flow behavior and validate the model against experimental measurements.
Conservation Equations
The three fundamental conservation principles of mechanics must be applied to solve the fluid dynamic or aerodynamic problem, namely:
- Conservation of mass, i.e., mass is neither created nor destroyed.
- Conservation of momentum, i.e., a force acting on a mass equals its time rate of change of momentum.
- Conservation of energy, i.e., energy is neither created nor destroyed and can only be converted from one form into another.
The resulting mathematical equations should then describe the fluid dynamic or aerodynamic behavior of the flow of interest, at least within the bounds of the stated assumptions and approximations. The solution to these equations can be obtained analytically, numerically, or both, providing the engineer with the desired results.
Flow Models
There are two basic approaches used in fluid dynamics and aerodynamics:
- An integral or finite control volume approach in which the equations are developed as they apply to a finite control volume surrounding the problem.
- The differential or infinitesimal fluid element approach, in which the relevant equations apply at every flow point.
In both approaches, the control volume or the fluid element may be fixed in space, allowing the flow to pass through it, or it may move with the flow, containing the same collective group of fluid molecules. The former approach, in which the model is fixed in space, is known as an Eulerian model, as illustrated in the figure below. The latter, in which the model moves with the flow, is referred to as a Lagrangian model. Each of these modeling approaches has certain advantages and disadvantages when applied to solving specific problems in aerodynamics. In most cases, there will be a preferred approach for each situation.
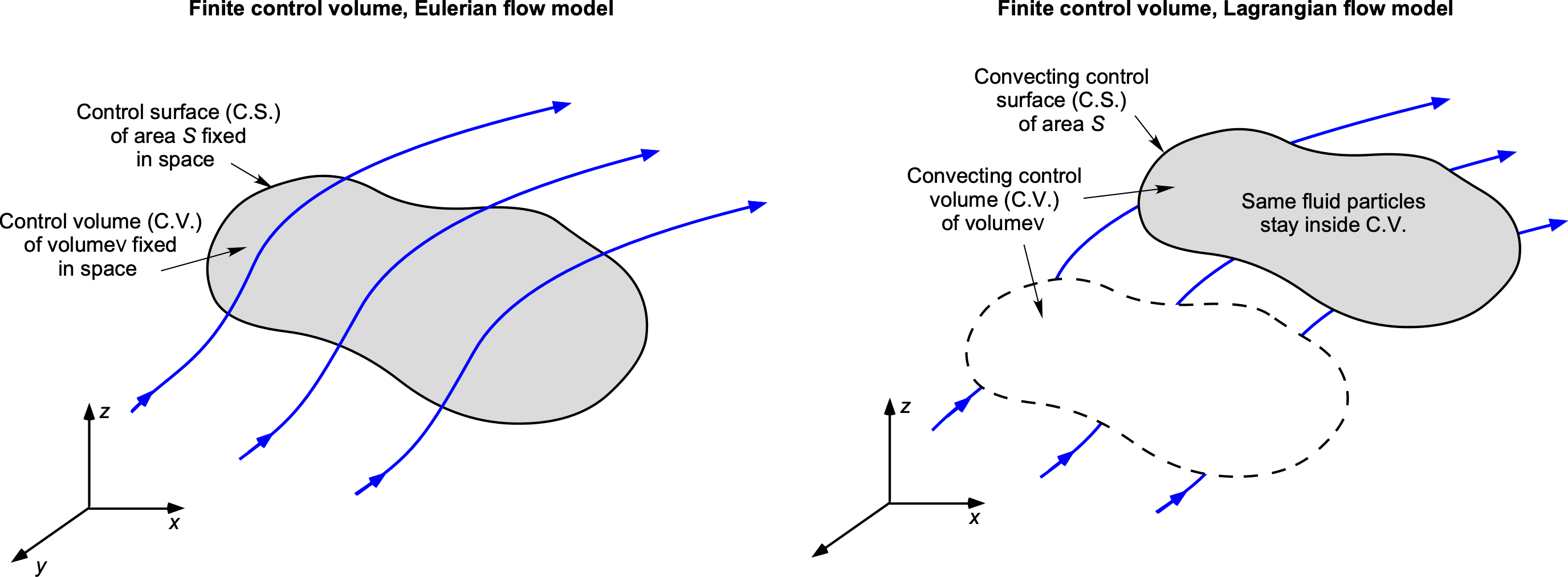
For example, on the one hand, an integral approach can be used to find total effects, such as the forces on a body in the flow, without necessarily solving for all the point properties in the flow. Knowing what the fluid is doing at every point in the flow may not be necessary, and an integrated approach may be more appropriate. On the other hand, the differential approach, as shown in the figure below, would be needed if the local distributions of flow velocity and pressure at points in the flow and over the surface of a body were the desired outcome.
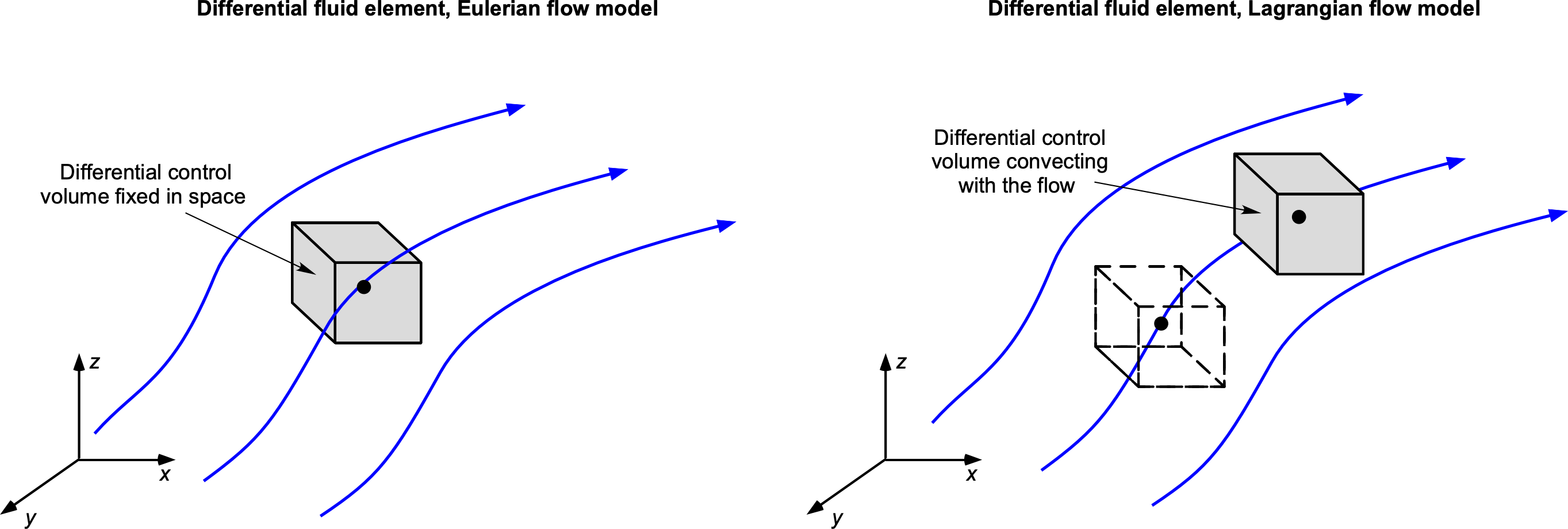
Likewise, a Lagrangian approach might be adopted over an Eulerian approach because it makes the problem description more manageable in modeling the physical problem and/or from a mathematical description and/or solution methodology. Part of the skills needed in fluid dynamics and aerodynamics problem-solving (and engineering problem-solving, in general) is to decide which type of foundational model to apply to specific problems. Sometimes, such decisions may not be immediately apparent, even to an experienced engineer, and different approaches may need to be tried tentatively before a suitable approach is determined.
For example, it may be desired to predict the velocity and pressure distribution over the surface of an airfoil or wing, as shown in the figure below. The question is then: What basic form of the aerodynamic model should be used? In this case, the answer is a differential model, in which point properties, such as flow velocity, streamlines, and pressures, can be determined. Integral forms of the equations are appropriate only when the overall or integrated aerodynamic effects are required. The total lift on the wing is an integral quantity because it arises from the impact of the pressure distribution when it is resolved and integrated over the wing’s surface.
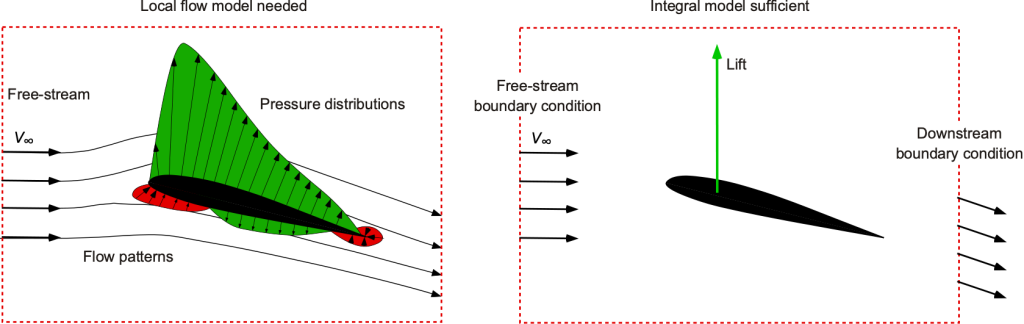
In practice, the integral approach is usually easier to learn and work with, at least from a mathematical and/or numerical perspective. The differential form of the equations is appropriate when the distributive quantities, such as velocity and pressure distributions over the wing’s surface, are needed, which are usually more computationally expensive. Again, the relative cost of obtaining a solution for the flow properties may need to be factored into the final choice of the model.
Finite Control Volume Approach
To introduce the conservation laws of fluid dynamics, it is convenient to focus on finite control volume or integral models, which are helpful in that they can be used to relate the global properties of the fluid. The concern is with the fluid properties entering the control volume versus the changes to these properties that occur within it. However, in many other practical problems, fluid properties at a point in the flow may be required, so using the differential (fluid element) model and applying this modeling approach to problem-solving is usually necessary.
In the finite control volume approach, a closed surface is drawn to enclose a specific volume of flow, as shown in the figure below. The symbol defines the area of the closed surface that bounds the control volume containing a fluid of volume
. The control volume is abbreviated to “C.V.” (denoted by
in mathematics) and the control surface to “C.S.” denoted by
in mathematics). This control surface (and control volume) must be large enough to encompass the entire domain of the problem. In some cases, the required control volumes may need to cover only part of the domain if certain flow conditions are known or defined elsewhere, which is common in practice. Engineers must develop a problem-solving technique to determine the most suitable control surface or volume, allowing the governing equations to be applied and enabling the correct solutions for the flow properties to be obtained.
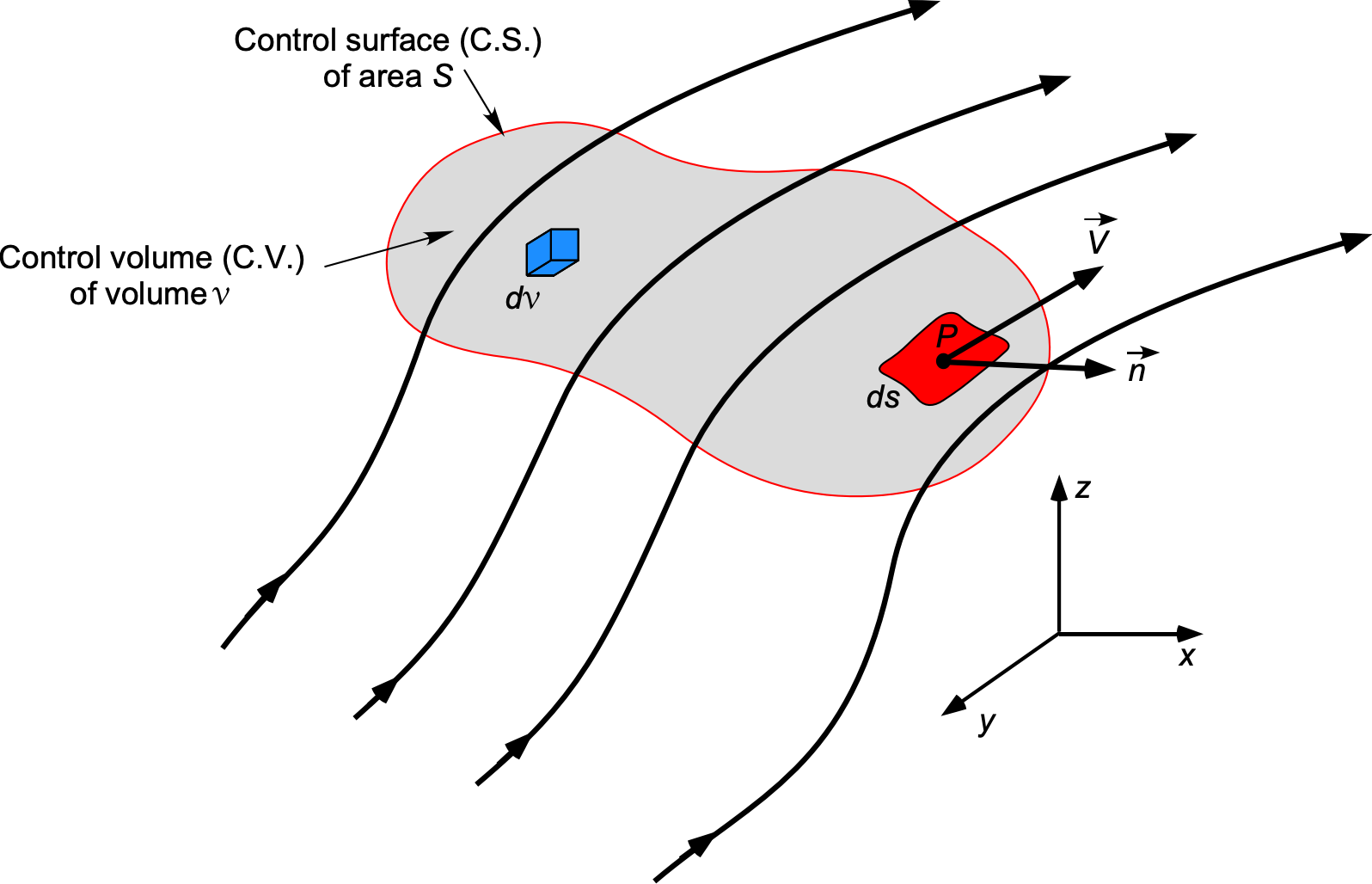
All fluid properties can and must be allowed to vary with spatial location (i.e., with respect to ,
, and
) and in time
so that
(1)
As previously described, is a small elemental area of the control surface, and the vector
is the unit normal vector. Because the product
appears in the resulting equations for the flow, the unit normal vector area is defined as
. Remember that by convention,
, and so also
, always point outward from the control volume perpendicular to the control surface. For example, if the surface is oriented perpendicular to the flow in the
direction (i.e., in the
–
plane), then
and if the surface is oriented perpendicular to the
direction (i.e., in the
–
plane) then
.
Notice: Be cautious not to confuse the symbol for velocity (a vector or
with the symbol for volume
or a “curly V.” Sometimes the symbol
is used rather than
, but the meaning (volume) is the same.
Mass Flow and Mass Flux
Before deriving the fundamental equations used in fluid dynamics or aerodynamics, it is essential to examine a concept vital to all these equations, which is mass flow. Consider a small, fully permeable surface of differential area that is oriented at some angle in a flow, as shown in the figure below.

Let the area be small enough so that the velocity of the flow is constant across it, i.e., in the spirit of the differential calculus. Then, consider the orientation of the small surface to be defined in terms of a unit normal vector
. The normal unit vector
establishes the orientation of the surface, where
is perpendicular to the curvature of the surface and points away from the surface. The mass flow
through the surface
per unit time (the mass flow rate) will be given by
(2)
where is the magnitude of the resultant flow velocity normal to the surface. Remember that if
is the velocity of the flow through the surface, then the component of the resultant flow velocity normal (perpendicular) to the surface is given by the dot-product
(3)
The concept is more effectively visualized in two dimensions, as illustrated in the figure below. Notice that the unit normal vector area is defined as , so that
(4)
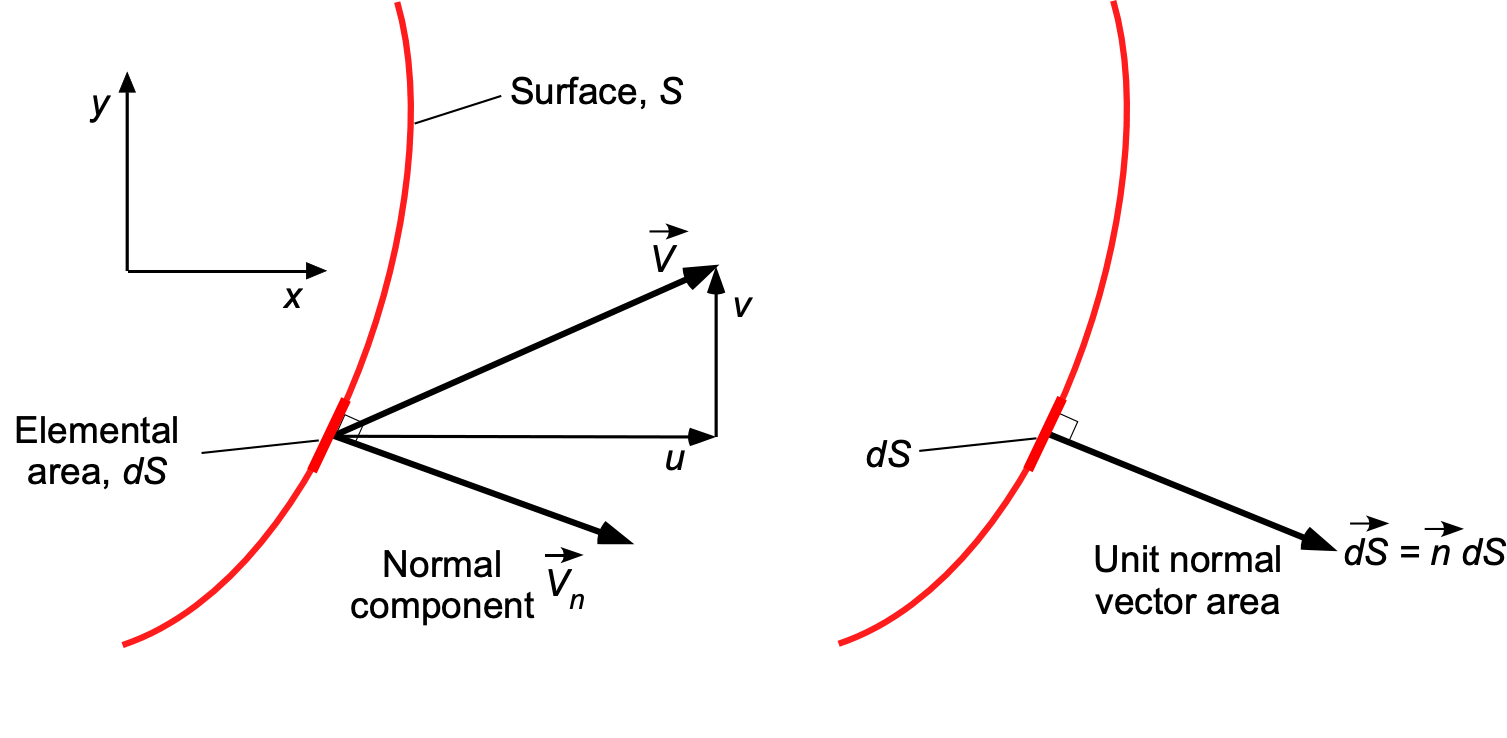
In this two-dimensional case, then
(5)
and
(6)
so
(7)
In general, the total mass flow rate, , over a surface
, is given by
(8)
Mass flow rate has dimensions () (
) (
) =
and so the units will be in kg s
in SI units or slugs s
in USC units.
The mass flux is defined as
(9)
which has has dimensions () (
) =
and so units of kg s
m
or slugs s
ft
. The mass flux terms like
, etc., frequently occur in fluid dynamic problem solving, so the meaning of these terms should be understood. The concepts of mass flux and unit normal vector area are also used in deriving the governing equations for fluid dynamics and aerodynamic flows.
Momentum & Energy Flow Rates
The corresponding momentum and energy flow rates can also be derived. The momentum flow through the surface
per unit time (the momentum flow rate) will be
(10)
Therefore, the total momentum flow rate, , over a surface,
, is given by
(11)
which is a vector equation with three components in Cartesian space. Momentum flow rate has dimensions of () (
)
(
) =
and so its units will be kg m s
in SI units or slugs ft s
in USC units.
The kinetic energy flow through the surface
per unit time (the kinetic energy flow rate) will be
(12)
Therefore, the total flow rate of kinetic energy, , over a surface
, is given by
(13)
Kinetic energy flow rate has dimensions (M L) (L T
) (L
) (L T
)
= M L
T
and so the units will be those of power, i.e., kg m s
or J s
or Watts (W) in SI units, and units of lb-ft s
in USC units.
Extensive & Intensive Properties
The conservation laws involve the rates of change of extensive properties, which are proportional to the mass of fluid contained within the control volume. The three extensive properties, which are all transportable by the flow, are those previously considered, i.e., mass, momentum, and energy, so that
(14)
where is called the specific energy, i.e., energy per unit mass. In the sense of an infinitesimal fluid volume
, then the mass is
.
The extensive properties, i.e., ,
, and
, which depend on the extent of the system, are designated by the general symbol
. The corresponding intensive properties, denoted by
,
, and
, are generally expressed as “per unit mass” and designated by the symbol
. The extensive and intensive properties are related by
(15)
Because the density of a fluid can change from point to point, it is always best to express the governing equations in terms of per unit mass. The intensive properties do not depend on the mass or extent of the system.
Reynolds Transport Theorem
The Reynolds Transport Theorem (RTT) yields a general equation known as the Reynolds Transport Equation (RTE). This equation enables the conversion of fluid transport equations from Lagrangian to Eulerian reference systems, a valuable problem-solving tool. Because the RTE connects governing equations in separate reference systems, it is sometimes referred to as a link equation.
Flow Model
The approach to deriving the RTE proceeds by defining a control system (sys) of fluid and a control volume (C.V.), as shown in the figure below. The system is a collection of fluid molecules of density in a Lagrangian frame of reference that sweeps into and out of the C.V. At some time,
, the system moves toward the C.V. At the time,
, the system, and the C.V. are coincident, i.e., they occupy the same space. At some later time,
, the fluid system moves out of the C.V. Therefore, this means that some of the fluid moves out of the C.V., some of the fluid remains inside the C.V., and some fluid comes into the C.V. to replace the fluid and properties that has moved out. In the derivation of the RTT, it becomes a matter of tracking and formally quantifying where all of this fluid goes.
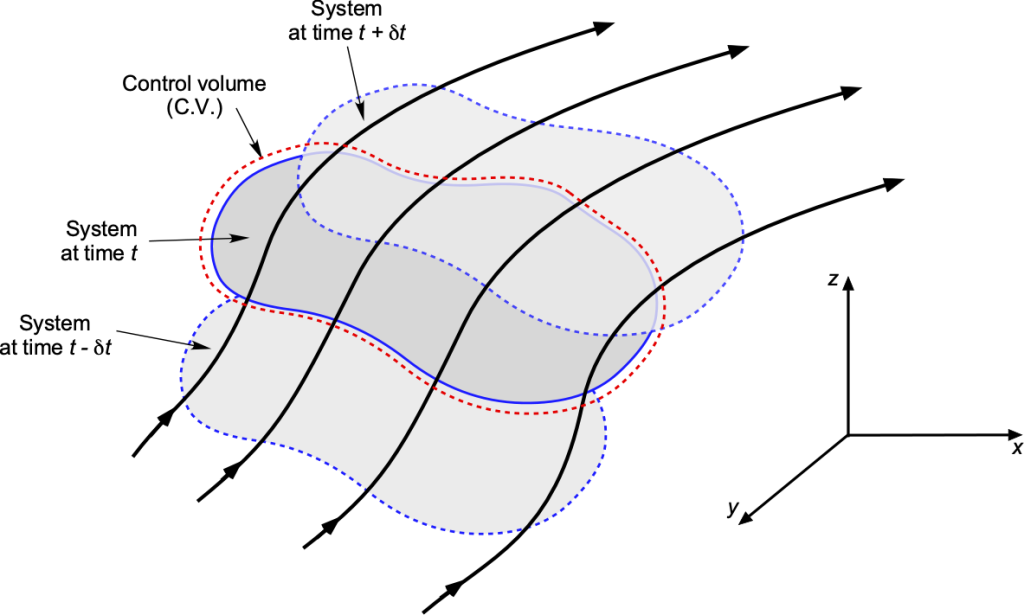
Derivation
Consider a small element of volume as shown in the figure below. The density of the flow is
, and the flow velocity relative to the C.V. is
. If
is one of the transportable intensive quantities, i.e., mass, momentum, and energy, then the corresponding extensive properties inside the small volume are
(16)
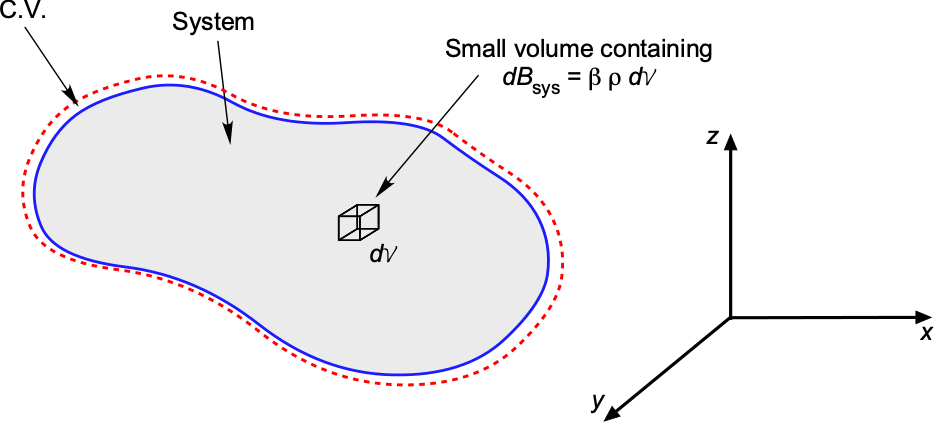
Integrating over the entire system volume then gives
(17)
Similarly, integrating over the C.V. gives
(18)
Notice that at time , then
(19)
but at time , then
(20)
Let be an extensive property of the fluid coming into the C.V. and
be the same extensive property of fluid coming out of the C.V., as shown in the figure below. It will be apparent then that
(21)
After rearrangement then
(22)
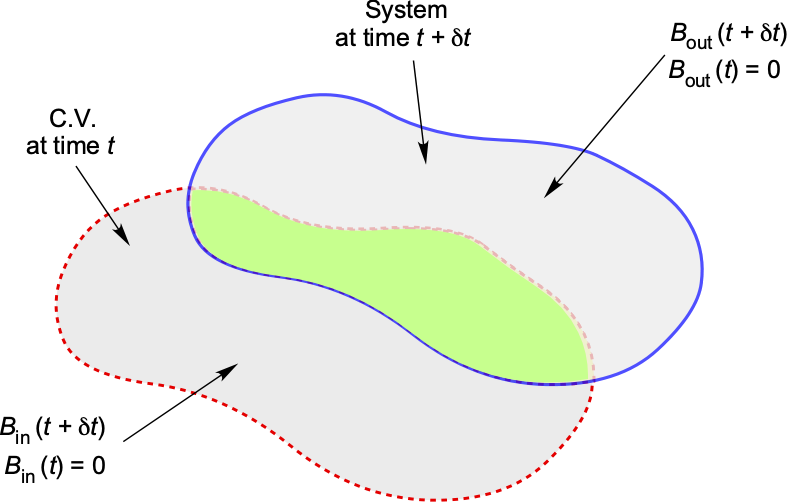
Recall that , so
(23)
(24)
The outcome here begins to look like a differential equation. Notice that the last two terms in Eq. 24 can also be expressed as
(25)
because , and also
(26)
because .
In the limit as , hen Eq. 24 becomes
(27)
By rearrangement, then
(28)
which is a differential equation. Substituting for from Eq. 17 and
from Eq. 18 gives
(29)
This previous equation helps connect fluid properties from a Lagrangian flow perspective, i.e., the fluid system moving with the flow, to the properties in an Eulerian perspective, i.e., the properties in a C.V. fixed in the flow. However, the C.V. does not have to be fixed in size, so its shape and size could also change over time.
The last term in Eq. 29 now requires further attention. It is apparent from the adopted flow model that some fluid comes into and out of the C.V., so there must be some net relative velocity of the fluid out of the C.V. Consider a small area of the control surface, C.S., of area , its orientation specified by the unit normal vector
, as shown in the figure below. The relative velocity of the flow out of the C.V. over the C.S. will be
(30)
The “relative velocity” refers to the velocity of the fluid relative to the moving boundary of the control volume, essentially the difference between the absolute fluid velocity and the velocity of the control volume itself. While many problems in fluid dynamics and aerodynamics will have a fixed C.V. in space and time, it is still possible that the C.V. can be deforming, hence the existence of the component
.
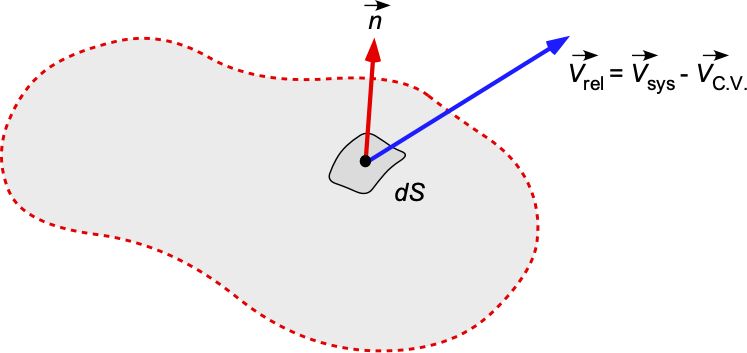
The volumetric flow rate over the surface will be the product of the component of flow velocity
that is normal to the area
over which it flows, i.e.,
(31)
The dot or scalar product gives the component of the volume flow that is normal to the surface. The corresponding mass flow rate is then found by multiplying by the local flow density, i.e.,
(32)
In terms of intensive properties, then
(33)
Integrating over the control surface gives
(34)
Therefore,
(35)
Reynolds Transport Equation (RTE)
Finally, after updating the terms in the preceding derivation and organizing everything in proper order, then
(36)
which is called the Reynolds Transport Equation (RTE). Notice that the mass, , of the elemental fluid volume
is given by
.
In other words, Eq. 36 states that the time rate of change of an extensive flow property, , in the system (sys) is equal to the time rate of change of
in the control volume (C.V.) plus the rate at which
is leaving through the control surface, i.e.,
(37)
Traditionally, the lowercase local derivative “” on the left-hand side of Eq. 36 is replaced by the substantial derivative “
,” implying that it is the net rate of change of properties in a “system.” Notice that the first term on the right-hand side of Eq. 36 is now replaced by the partial derivative because, generally,
.
The RTE is valuable because it allows one to relate flows in Lagrangian and Eulerian reference systems. It also helps to derive the conservation laws of fluid dynamics and aerodynamics for mass, momentum, and energy. The RTE is often referred to as a “link” equation because it connects the governing equations in both reference systems.
What are the units of the Reynolds Transport Equation?
The Reynolds Transport Equation (RTE) relates to the time rate of change of an extensive flow property, . The three extensive properties are mass, momentum, and energy. Therefore, the units of the RTE depend on the property being considered. However, in each case, the units represent the property per unit time; for example, for mass, the units would be M T
, and for momentum, the units would be M L T
.
Summary & Closure
Setting up flow models involves creating mathematical representations of fluid behavior, which is necessary to analyze and predict where the fluid flows and its related properties. Control volume approaches are fundamental concepts in fluid dynamics and are used to analyze and understand the behavior of fluids in various systems. A control volume is a fixed region in space that encloses a specific volume of fluid, and it is used to study the flow of mass, momentum, and energy across its boundaries. The control volume can be of any shape or size, depending on the problem.
The differential or infinitesimal fluid element is another approach in which the relevant equations apply at every point in the flow. In both cases, the control volume or the fluid element may be fixed in space, allowing the flow to pass through it, or it may move with the flow, containing the same group of fluid molecules. The Reynolds Transport Equation (RTE) is very important (i.e., a “star” equation) in fluid dynamics and aerodynamics. It can be used to connect the flow physics of Lagrangian and Eulerian flow models.
5-Question Self-Assessment Quickquiz
For Further Thought or Discussion
- How might the physical fluids problem to be solved impact the choice of flow models? Discuss.
- How might flow models be used in interdisciplinary fields like biomedical engineering? What challenges arise when applying flow models across different disciplines?
- Research the Internet for examples of applications in which flow models have significantly contributed to solving real-world fluid dynamics and/or aerodynamic problems.
- A Pitot probe is used on an airplane to measure dynamic pressure. Is this a Lagrangian or an Eulerian measurement? Explain.
- Put yourself in the position of a course instructor. What might be effective ways to teach students about setting up flow models? How might instructors better balance theoretical concepts with practical applications?
- Consider specific flow scenarios or complex geometries where setting up accurate flow models remains challenging. How might researchers tackle these challenges?
Additional Online Resources
- Navigate here to watch a video from the National Science Foundation on types of flow models.
- Watch this video to learn more about the Lagrangian and Eulerian flow models.
- This is an excellent video on the derivation of the Reynolds Transport Equation (RTE).
- Video: Fluid Mechanics: Reynolds Transport Theorem.