67 Electrically-Powered Aircraft
Introduction
Electrically powered aircraft convert electrical energy stored in batteries and deliver this energy to drive an electric motor connected to a propeller (or a fan), thereby producing propulsive thrust for flight. Such aircraft can potentially have a higher net energy efficiency than fossil-fueled propulsion systems, i.e., an internal combustion engine (ICE), such as a piston-prop, turboprop, or turbofan. Indeed, reductions in net energy consumption for propulsion are highly desirable, with electrically powered aircraft potentially using less than half the energy per unit of equivalent power delivery compared to an ICE. However, for an airplane, what matters is not just the power or energy available or required for flight per se, but the power or energy required per unit of flight weight, i.e., the power-to-weight ratio or energy-to-weight ratio.
Electrically powered aircraft have, at least for now, been mostly limited to various types of Unoccupied Aerial Vehicles (UAVs) or drones, which are used for tasks such as aerial photography, mapping, inspection, and short-range delivery. Many of these drones are often hybrids, capable of vertical takeoff and landing (VTOL), but cruise for most of the mission as fixed-wing airplanes, as shown in the photograph below. These platforms benefit from the simplicity, quiet operation, and low maintenance of electric propulsion. However, the limited energy density of batteries continues to constrain flight time and payload, making electric propulsion less practical for larger aircraft or long-duration missions.
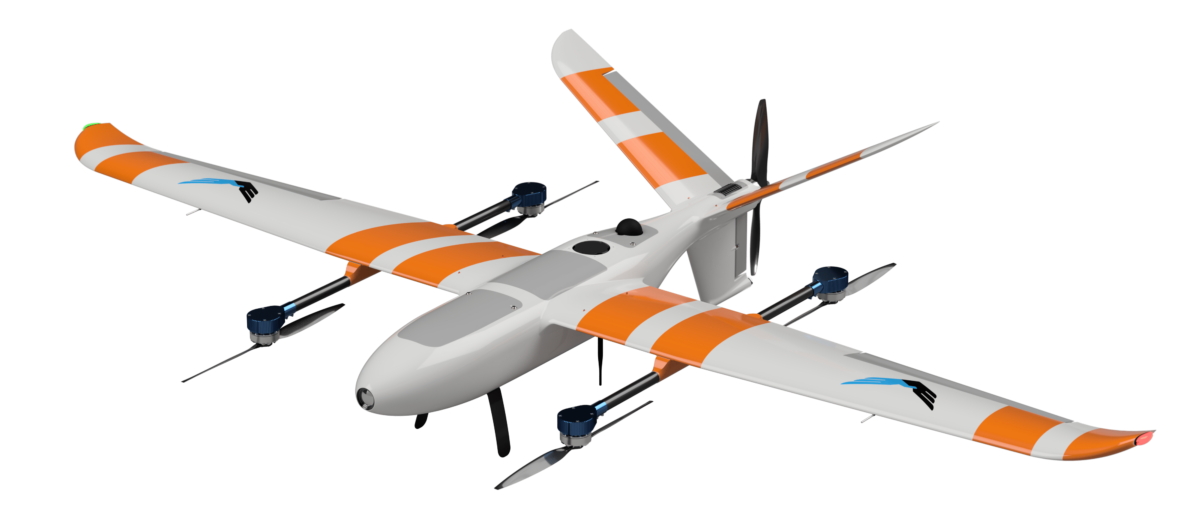
More recently, electrically powered light-sport aircraft are being developed, an example being shown in the photograph below. The upward scalability of electrically powered aircraft is unattractive, primarily because of the rapid weight growth and the associated high volume of batteries required. Nevertheless, this situation will likely change as the required technologies mature in the coming decades, but with a tipping point on the longer-term horizon. Electrically powered aircraft can improve energy efficiency and reduce greenhouse gas (GHG) emissions because of their commensurately lower “carbon footprint.”[1] GHG emissions contribute significantly to the depletion of the ozone layer in the atmosphere and global warming, causing unusually severe weather conditions such as F5 super-tornados and CAT-5 hurricanes, once considered anomalies, to increase.
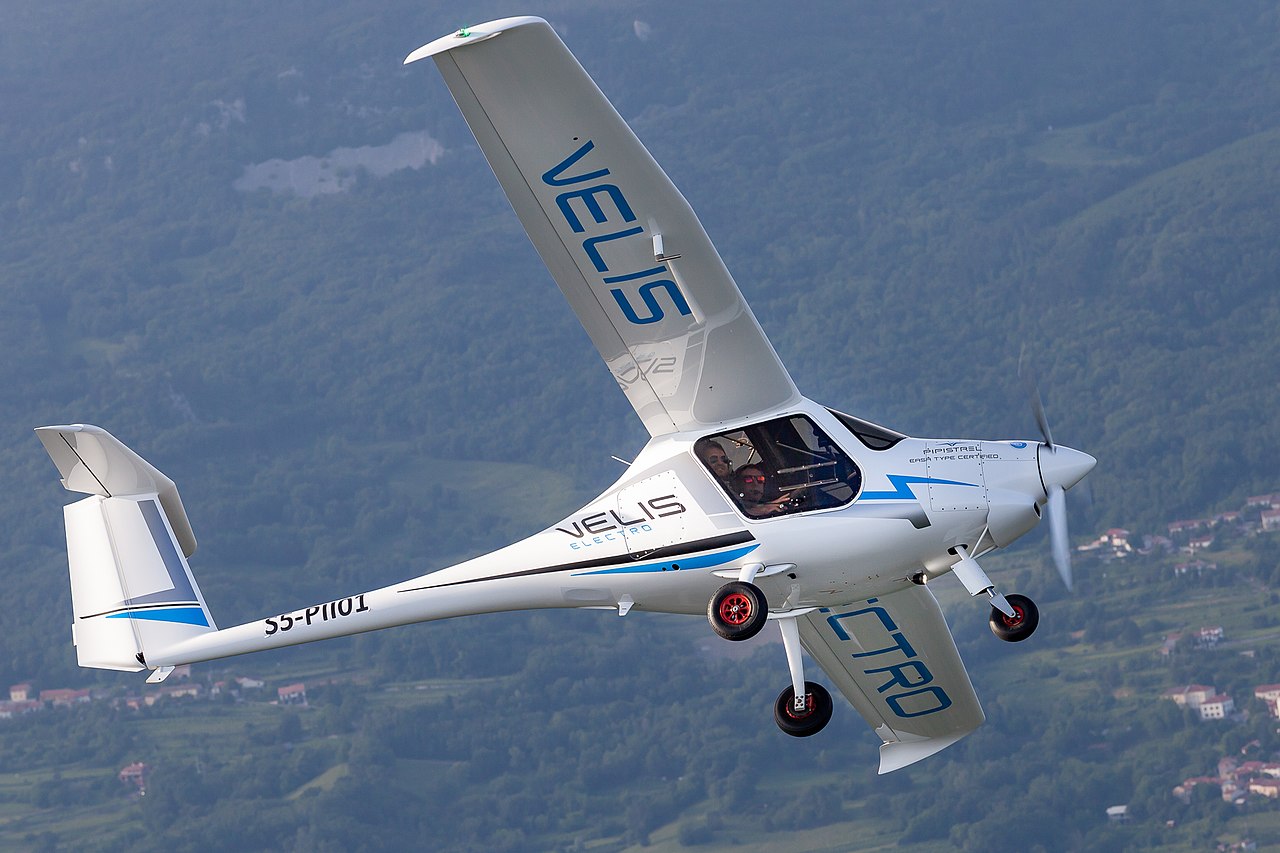
Some industry leaders have proclaimed that electric propulsion will represent the future and perhaps the pinnacle of aviation technology. While a bold vision is essential for success, its realization in the near term is unlikely for reasons that extend beyond technical limitations. Although advances in battery technologies have begun to decarbonize ground transportation, electrifying aviation poses far greater challenges on technical, operational, economic, and educational fronts. It is essential to acknowledge these hurdles rather than assume they have already been overcome. Nevertheless, as shown in the image below, ambitious proposals are being fielded by NASA and other organizations to conduct the necessary research and achieve electric propulsion goals for aviation, as they should. These goals include replacing piston-prop and turboprop engines with electric motors or using ducted fans driven by electric motors instead of turbofans to power commercial airliners. Although NASA’s X-57 Maxwell demonstrator concluded its flight-test program in 2022, lessons learned from its development will continue to influence the design of next-generation electric propulsion systems.
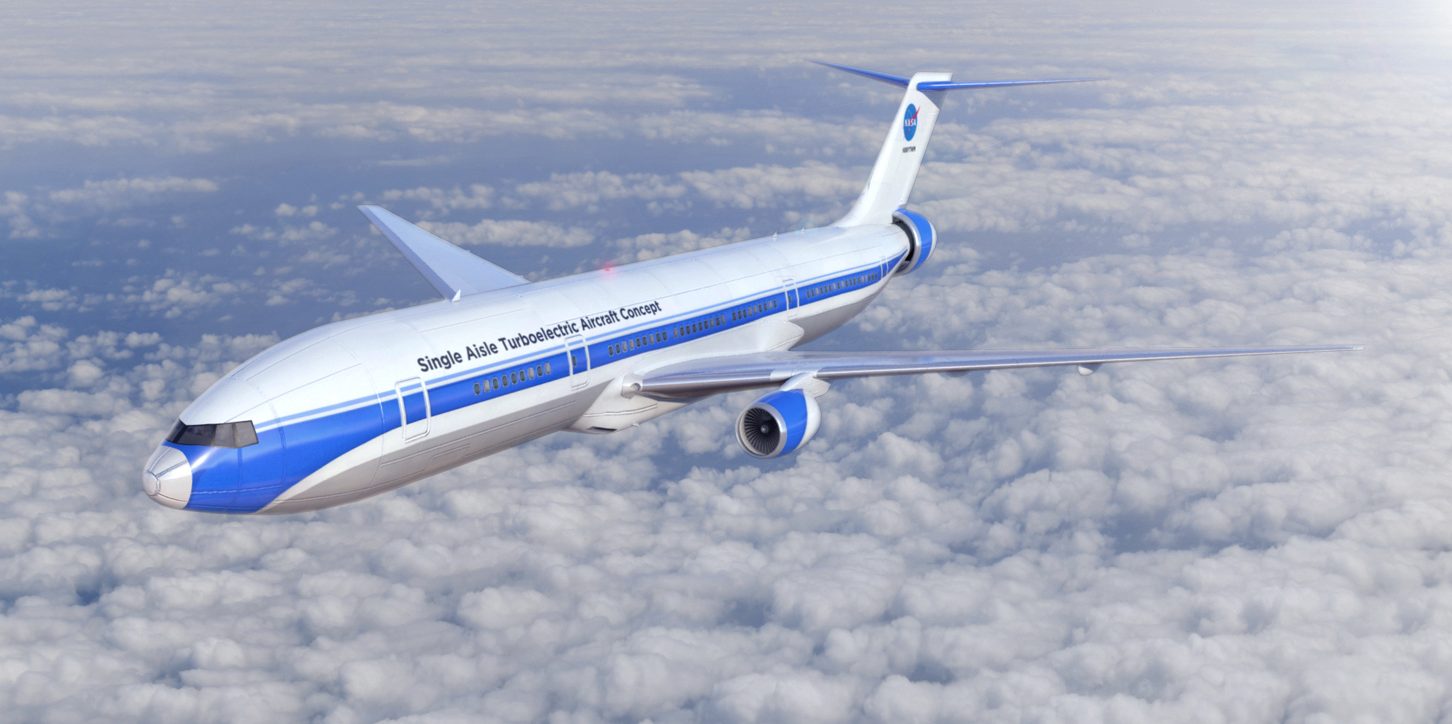
The aviation industry, known for its long innovation cycles, is beginning to invest resources into this promising new technology. Key initiatives, such as the Airbus E-Fan X project, are proving out high-power electric drivetrains and paving the way for certification standards and safety protocols. While the future of electrically powered aircraft appears promising, the technological tipping point between fossil fuels, such as Avgas (aviation gasoline) or Jet A-1 (kerosene used for aircraft), and electrical energy is likely another 20 to 30 years away. Another challenge for electrifying aviation, particularly in the commercial sector, is the relatively long time needed to recharge batteries. Refueling an aircraft using Avgas or Jet A-1 is relatively quick, taking up to 30 minutes for even the biggest airliners flying on transoceanic routes. However, recharging a battery-powered airliner would take significantly longer, perhaps several hours, and an airliner sitting on the ground for that long makes no economic sense for an airline.
Continued research and development efforts by engineers are necessary to push the boundaries of electric motor and battery technologies, realizing the higher energy efficiencies possible with electrically powered aircraft and proving their economic viability. An attractive byproduct of this technical effort is undoubtedly the reduction and eventual elimination of greenhouse gas (GHG) emissions. However, as shorter-term goals, a combination of approaches, including sustainable aviation fuels (SAFs), improved and novel aircraft designs, hybrid-electric propulsion, and hydrogen fuel cells, will likely be necessary. In the meantime, engineers need to be well-versed in the fundamentals of this emerging and rapidly growing field of electric propulsion for aircraft.
Learning Objectives
- Understand the environmental motivations behind electric aviation, including the impact of greenhouse gas emissions and the concept of carbon footprint.
- Explain the meaning and significance of energy density in the context of battery-powered flight.
- Evaluate the performance and weight trade-offs inherent in electrically powered aircraft designs.
- Identify the key capabilities and limitations of current battery technologies used in aviation.
- Assess the role of energy-to-weight ratio in determining the feasibility and range of electric aircraft.
- Distinguish between hybrid-electric, battery-electric, and solar-electric propulsion architectures.
- Describe the concept of eVTOL (electric Vertical Takeoff and Landing) aircraft and explain their relevance to emerging urban air mobility (UAM) applications.
- Know about the technical, operational, and regulatory challenges facing the development and certification of electric aircraft systems.
Why Electric Propulsion?
The energy source required for an electrically powered aircraft is obtained from batteries through an electrochemical energy conversion process, which creates an electrical current to drive an electric motor. The motor then creates the needed mechanical energy at a shaft to drive a propulsor in the form of a propeller (or fan) to do work on the air and create thrust, as shown in the figure below, although other solutions may be possible. Batteries and electric motors are certainly familiar technologies, having been around for centuries. However, over the last decade, sufficient technical progress has been made to make these essential elements viable enough to power airplanes, thanks to higher energy density in the batteries (i.e., more energy storage per unit weight) and the use of better motors (i.e., higher power output per unit weight).
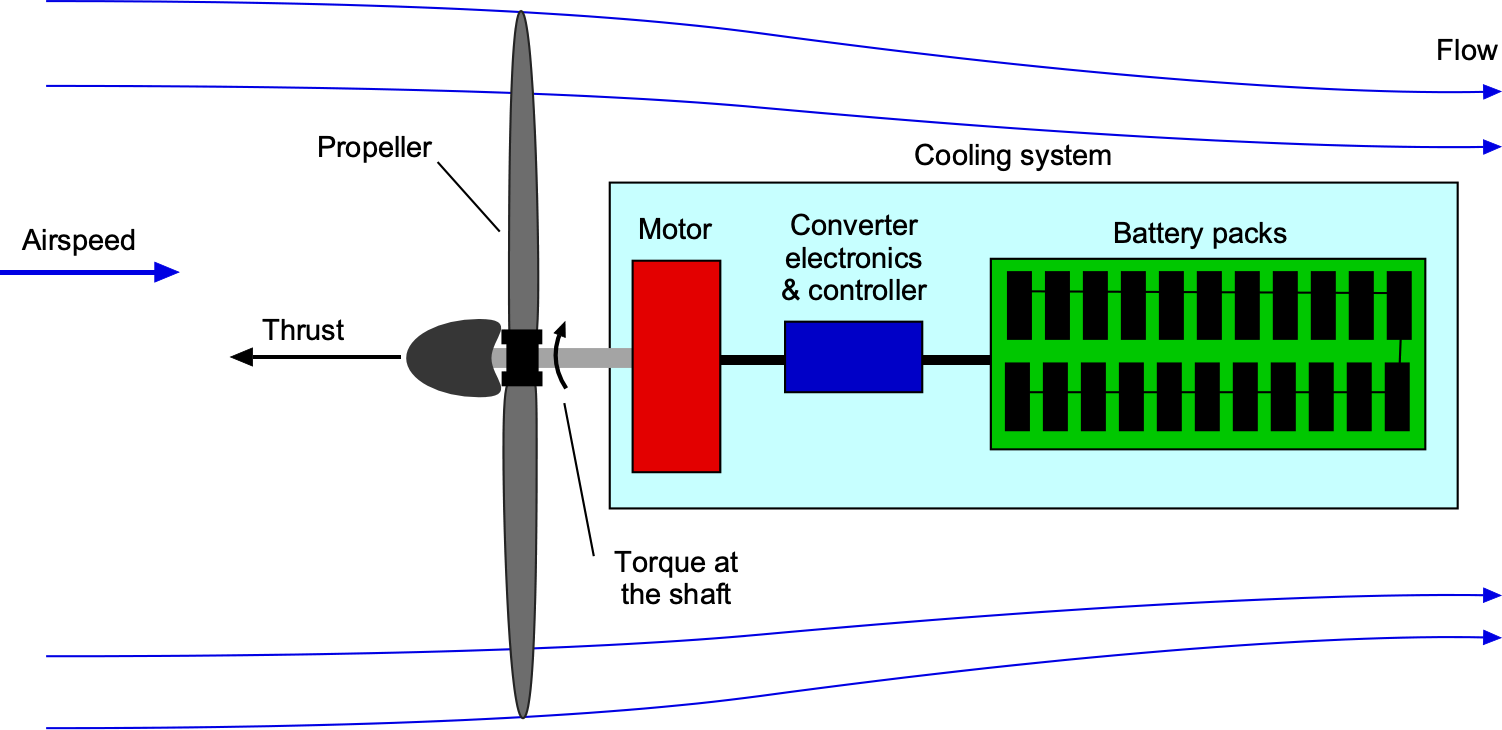
Electric vehicles (EVs), whether they are terrestrial or airborne, can achieve higher overall energy efficiency than those powered by internal combustion engines (ICEs), even when accounting for inefficiencies in electricity generation and distribution. However, as with all forms of electrified transportation, the foundational technologies for engineers to understand are the characteristics of electrical energy storage systems (i.e., batteries) and the means of converting electrical energy into mechanical work for propulsion (i.e., motors). Electric motors have higher efficiency than an ICE in converting the available energy into mechanical energy in the form of shaft torque and, hence, into usable power.[2]
Another reason is that electric motors have excellent power-to-weight ratios compared to an ICE. The downside is that the energy source, the batteries, which by any standard are heavy, have much less energy density than is contained in fossil fuel. Therefore, many heavy batteries must be installed on the aircraft to supply the energy needed for its flight. A further consideration is the need for a cooling system, which can increase the net system weight by up to 20%. Furthermore, the net energy balance must always be considered, including the trade-offs between higher electrical efficiency, net weight, flight requirements, and overall operating costs. Regarding costs, the relatively low price of electric power, measured in US dollars per kilowatt-hour (US$/kWh), is a significant advantage. However, an important consideration is the high cost of battery replacement because of the relatively limited recharge cycles of Li-ion batteries (fewer than 3,000 recharge cycles).
In addition, engineers need to be aware of the necessary infrastructure to supply the required electrical power, as well as the economic and other trades involved. Electrification efforts can also focus on new engineering solutions to replace traditional pneumatic and hydraulic systems on aircraft with electrically driven alternatives. In the U.S., electricity is generated from power stations using a variety of fuels, including natural gas, coal, nuclear energy, and renewable energy sources such as hydroelectric power, wind power, solar power, and biomass. Natural gas plants are currently the most prevalent because of their cost-effectiveness and efficiency, while coal usage is rapidly declining. Despite higher operational costs, nuclear power provides approximately 20% of the grid’s net electricity. Renewables are quickly growing, with wind and solar sources leading the way in these technologies.
Modern natural gas combined cycle (NGCC) power plants, among the most efficient, achieve thermal efficiencies of up to 60%, i.e., 0.6. After accounting for transmission and distribution losses of around 5%, i.e.,
0.95, the efficiency of converting this electrical energy into chemical energy in a battery, where
0.95, then through the electronic speed controller, where
0.98, and then to useful power at the shaft of a motor, where the motor efficiency is
0.95, and the wiring losses are 5%, i.e.,
0.95, then the combined net efficiency is
(1)
This efficiency level is significantly better than the 25% to 30% efficiency typical of ICE vehicles when converting gasoline fuel into shaft power, as well as diesel engines, which are about 30–35% efficient. However, conventional liquid fuels, such as gasoline, diesel, or Jet-A, carry hidden upstream energy costs. Significant energy is consumed during the extraction, refining, and distribution of crude oil, with refining efficiencies typically ranging from 85% to 90%. When combined with the low thermal efficiency of combustion engines, the overall oil well-to-propeller efficiency of fuel-powered aircraft may be as low as 30%.
This greater net efficiency means that EVs use less net energy per unit distance traveled, resulting in lower fuel consumption and reduced carbon emissions. While the specific efficiencies can vary based on the type of power plant and the fuel used, the advantages of EVs immediately become apparent when considering the entire energy pathway. Therefore, there are compelling arguments for why electric vehicles (EVs) are more energy-efficient and environmentally friendly than traditional gasoline- or diesel-powered vehicles.
What are greenhouse gases (GHGs)?
Gases that trap heat in the atmosphere are called greenhouse gases. They act like the glass walls of a greenhouse, hence the name. Without this greenhouse effect, temperatures would drop to such low values that life on Earth could not be sustained. Human activities are altering the Earth’s natural greenhouse effect, leading to a significant increase in the release of greenhouse gases. Scientists generally agree that greenhouse gases cause global warming and climate change. These types of gases include:
- CO2: Carbon dioxide is one of the primary greenhouse gases emitted through human activities, such as the burning of fossil fuels, deforestation, and industrial processes.
- CH4: Methane is a potent greenhouse gas released from various sources, including the processes of natural gas and oil production, livestock farming, and the decomposition of organic waste.
- N2O: Nitrous oxide is a greenhouse gas emitted from agricultural and industrial activities, as well as the combustion of fossil fuels and solid waste.
- F-gases: Fluorinated gases refer to a group of chlorofluorohydrocarbons (CFCs), hydrofluorocarbons (HFCs), perfluorocarbons (PFCs), and sulfur hexafluoride (SF6). These gases have detrimental effects on the ozone layer, thereby contributing to global warming.
Energy Density of Batteries
When engineers discuss batteries for electrically powered aircraft, the term “energy density ” inevitably comes up. In energy storage applications, the energy density is defined as the ratio of the energy stored to the volume or mass of the storage medium. To this end, energy densities are often quoted in terms of gravimetric energy density, , and volumetric energy density,
, which are usually referred to, in general, as specific energies. For any aircraft type, the weight of the energy storage medium is critically important because the power and energy required for flight increase with the square of its weight. It costs energy to carry energy, especially in the case of batteries, which represent such a high fraction of the flight vehicle’s total weight.
An aircraft’s power and energy demands for flight are significantly greater than those of a terrestrial vehicle. Indeed, the power and energy required for a small aircraft are about one order of magnitude higher than those of a road vehicle of the same gross weight, such as an average-sized family saloon. Therefore, to make an aircraft practically and economically successful in carrying a payload over any required distance, a high energy density in the fuel and low specific fuel (or energy) consumption of the engine or motor are crucial. For conventional aircraft propulsion using fossil fuel, such as Avgas or Jet A-1, the energy is stored in liquid form inside the fuel tanks; this energy is then liberated by combustion inside the engine. For electric propulsion, the energy is stored in batteries, which is liberated through an electrochemical process to supply a current to drive an electric motor.
Gravimetric Specific Energy Density
The mass or weight or “gravimetric” specific energy density of a battery is defined as
(2)
where is the stored energy (i.e., the ability to do work), and
is the mass of the battery containing the stored energy. Remember that weight is mass times acceleration under gravity, so one must be careful with units.
Volumetric Specific Energy Density
The volumetric specific energy density of a battery is defined as
(3)
where is the volume of the battery occupied by the stored energy.
Units of Energy Density
For all energy storage devices, the available energy is typically quoted in terms of energy available for a specific unit of time (usually one hour), i.e., in units of Watt-hours (Wh) or kilowatt-hours (kWh) in the SI system. Notice that energy has units of work (i.e., force times distance) or base units of M L2T-2, which is equivalent to a Joule (N m) in SI units or foot-pounds (ft-lb) in USC units. One Watt is a Joule per second, so one Watt-hour equals 3,600 Joules of energy. In USC units, energy output can be quoted in horsepower-hour (hp-hr). However, this latter unit is rarely used, as the SI system is the international standard for quantifying electrical energy and power, even in the U.S.
Comparison with Fossil Fuels
How do these preceding values stack up with fossil fuel? On the one hand, the energy density of jet fuel is approximately 11.9 to 12.5 kilowatt-hours per kilogram (kWh/kg), depending on the formulation and grade. The corresponding volumetric energy density is approximately 9.69 kWh/Liter (or kWh/L). The energy density of Avgas can also vary depending on the specific formulation and grade, being approximately 12.2 to 12.8 kilowatt-hours per kilogram (kWh/kg). On the other hand, Li-ion batteries have a gravimetric energy density of only about 0.22 to 0.25 kWh/kg, which is 50 times less than jet fuel, and a volumetric energy density of about 0.69 kWh/L, which is 14 times less than jet fuel. The figure below illustrates that the mass (and weight) of the batteries is a more critical issue for an aircraft than their volume. However, both weight and volume are significant concerns in the aircraft design process.
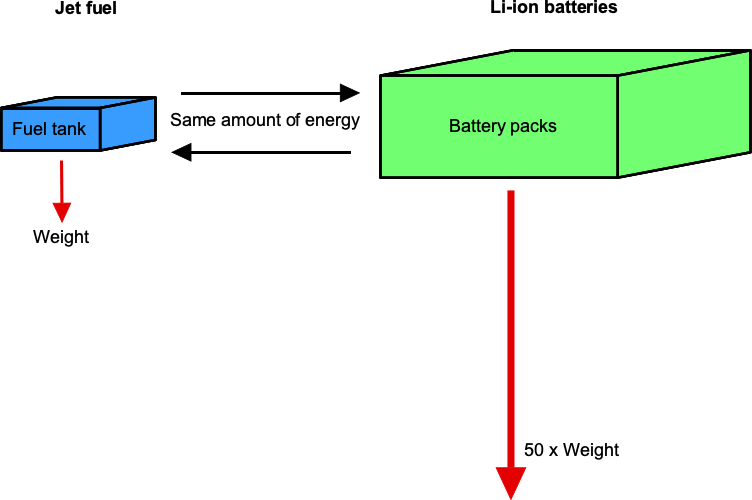
The equivalent energy contained in batteries compared to jet fuel requires 15 times the volume and incurs 50 times the weight. Therefore, one of the most significant challenges in the electrification of aviation now becomes apparent: the relatively low energy density of storage batteries compared to fossil fuels, as well as the higher weight penalty associated with storing that energy. For an aircraft, weight means everything and is one of the so-called “killers” of performance, the other being aerodynamic drag. However, these concerns are also offset by the higher energy conversion rate of an electric motor compared to an internal combustion engine (ICE), although this benefit must still be addressed on a system level in conjunction with the type of propulsor, such as a propeller or a fan.
What is a liter or a litre?
A liter (in the US) or litre (elsewhere) is a unit of volume used in the SI system. A liter is equivalent to 1,000 cubic centimeters (cm3) or one cubic decimeter (dm3), which is a cube with sides measuring 10 centimeters (0.1 meters) in length. The symbol for a liter is “L” or sometimes “l” will be used in commercial contexts. A liter is equivalent to 1.057 quarts or 0.264 gallons in USC units. The unit of a liter is widely used for measuring the volume of liquids, but remember that it is not a base engineering unit; the base SI unit of volume is cubic meters (m3).
Considerations for Electric Propulsion
The uptick in interest and subsequent development of various forms of electric aircraft are driven by the general goals of improving energy efficiency and reducing greenhouse gas (GHG) emissions from aircraft. To the flying public, however, the cost of a ticket to fly from one place to another is what matters to them, not so much whether they may care to acknowledge that they will also generate a substantial carbon footprint in the process. Furthermore, the core technical issue for an airline is improving aircraft efficiency and reducing seat-mile costs, i.e., transporting one passenger by one mile. The airlines will quickly align if this goal requires electric propulsion as the next step.
In the meantime, the International Civil Aviation Organization (ICAO) continues to advocate for stricter regulations that will reduce greenhouse gas (GHG) emissions from commercial aircraft. Regulations can help drive technical developments in the needed directions. Yet, it remains an economic and regulatory problem. However, in reaching these worthy goals, engineers must continue to address many key issues and technologies in developing successful electrically powered aircraft.
Batteries
Batteries are a crucial component of an electric aircraft, providing the source of the electrical energy required for flight. Li-ion batteries are commonly used, but all types of batteries are heavy, and battery technology still has a long way to go before it can have the energy densities needed for aircraft. Engineers are also developing other battery formats and chemistries to improve energy storage capabilities.
Electric Motors
Electric motors convert electrical energy into mechanical torque at a shaft and then into propulsion using a propeller or a fan. They can be of various types, such as brushed or brushless, synchronous, or induction motors. Electric motors can be 90% or more efficient, with the remaining 10% loss primarily from thermal losses, making further efficiency improvements challenging to achieve. However, advances in the power-to-weight ratio of motors, the metric that matters for an aircraft, are still possible. These gains are driven by improvements in materials (for example, high-temperature permanent magnets and high-permeability electrical steels), power electronics (wide-bandgap semiconductor inverters), novel motor topologies (such as axial-flux designs), and enhanced thermal management methods (including liquid cooling), which together can push the specific power of electric motors beyond 10 kW/kg.
Thermal Management
Thermal management systems are essential for maintaining the optimal temperature of batteries, motors, and other electrical components. The electrical current draw is high for aircraft, and the batteries can become excessively hot. Batteries exhibit some resistance, which can cause heating to occur during both charging and discharge cycles, especially with high currents. Therefore, proper cooling or thermal mitigation measures must be implemented to ensure optimal performance and prevent overheating or other temperature-related issues. A worst-case scenario is that overheating could cause failure or a fire, which is, in most cases, catastrophic for an airplane. Designing these cooling systems for high specific power requires careful trade-offs between heat-rejection capacity, system weight, and airframe integration.
Charging Infrastructure
Electrically powered aircraft require suitable airport charging infrastructure for recharging their batteries. These charging stations must be able to accommodate an aircraft’s high power and rapid charging demands. Merely extending the existing infrastructure for fast-charging electrically powered terrestrial vehicles, increasingly found at gas (petrol) stations and parking lots worldwide, cannot be considered a viable solution for aviation purposes. Airport charging for electric aircraft must be designed as dedicated megawatt-class hubs with on-site energy storage or renewable buffering and requires substantial grid reinforcement to recharge large battery packs within the short turnaround times demanded by commercial aircraft operations.
Costs
Li-ion batteries are expensive in terms of specific energy and replacement costs, which are also tied to the number of usable recharge cycles, typically ranging from 2,000 to 3,000 cycles, even for the best batteries. In 2021, the cost of Li-ion batteries for non-aviation applications was about $250/kg, and aviation applications (requiring additional certification) were about $500 per kWh. Additionally, it is essential to consider that the total cost of implementing Li-ion batteries in aviation involves not only the cost of the battery itself but also the cost of system integration, battery monitoring systems, safety measures, and numerous paperwork processes. Reducing aviation battery costs will require a combination of technological advancements, economies of scale, and industry investments. Indeed, continued basic research into battery technology will be crucial for achieving significant cost reductions in the future.
Electric Motors
An electric motor is a relatively simple electromechanical machine, at least in principle, which converts electrical energy into shaft torque and rotational mechanical energy. Electric motors operate through the interaction between the magnetic field and the electric current in wire windings to generate torque at the motor’s shaft, as shown in the animation below for a brushed motor. Motors used for aviation must be designed with a high power-to-weight ratio, just like any other propulsion system.
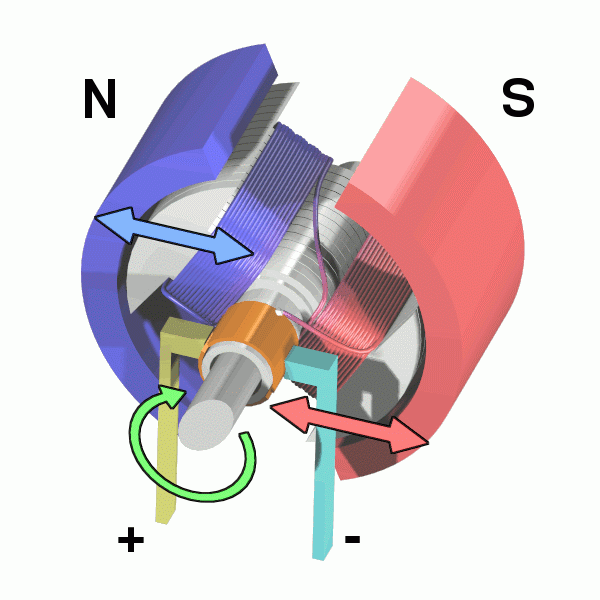
One significant benefit of electric motors over other methods of producing rotational torque, such as from an ICE, is that they are much more energy efficient. Typically, electric motors are over 90% efficient, whereas internal combustion engines (ICEs) using fossil fuels are between 30% and 50% efficient. Electrical motors are also lightweight, compact, and mechanically simple, and can provide almost instant increases in power when required. The power or strength of electric motors is quantified in terms of their specific power density (measured in kW/kg), equivalent to a power-to-weight ratio. Today’s state-of-the-art electrical motors can achieve power-to-weight ratios of up to 5 kW/kg, with potential improvements potentially reaching six or even 7 kW/kg. Such power-to-weight ratios are significantly higher than those achievable with an ICE.
Specialized types of electric motors, such as the brushless and radial-flux designs, provide various advantages over the primary motor design. One newer design of particular importance for aviation use is the axial-flux motor; its main advantage is higher power density and electrical efficiency. Axial-flux motors are also compact, making them suitable for use in applications where space is limited, such as an aircraft. In addition, it is possible to stack multiple motor units together to achieve the desired level of net power output.
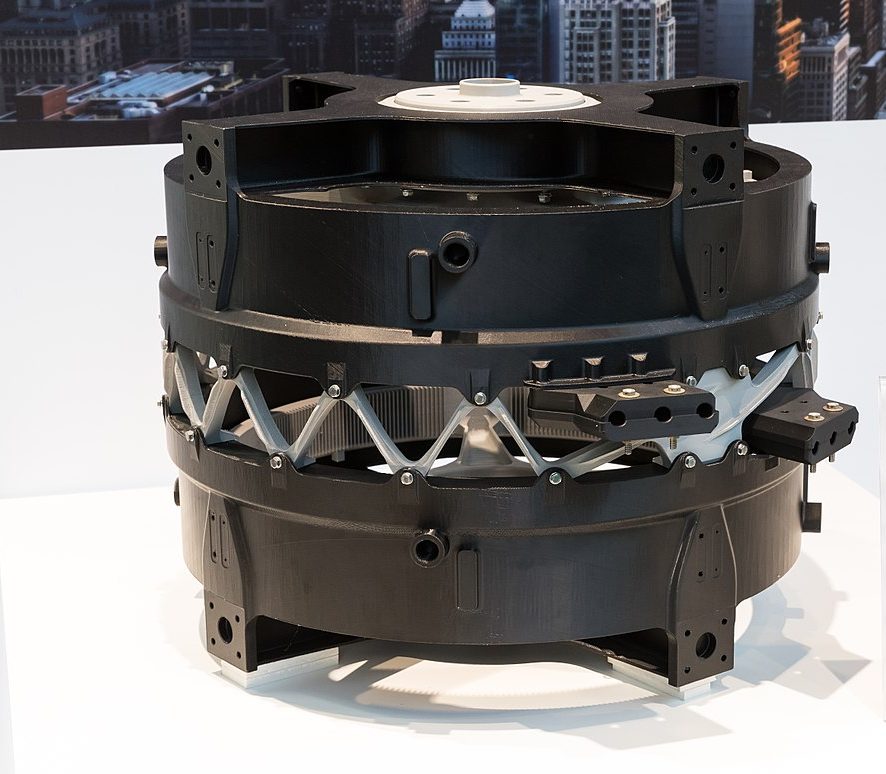
Battery Design
Electrically powered aircraft and their operation set unique and stringent requirements for battery design. The batteries must be lightweight, compact, quickly rechargeable, and capable of delivering high current and power to meet the requirements for all phases of flight, especially during takeoff and climb. They must also have protections to ensure safe operation and thermal control.
Rechargeable lithium-ion (Li-ion) batteries are the most widely used type of battery today. Prior to that, nickel-cadmium (Ni-Cd) batteries were commonly used. Li-ion batteries have become ubiquitous, powering everything from smartphones to laptop computers, electric cars, and even airplanes, mainly because they have the highest specific energy of any other type of battery. As previously discussed, specific energies are measured in terms of gravimetric energy densities (kWh/kg) or volumetric energy densities (kWh/L), both of which are important for aviation applications.
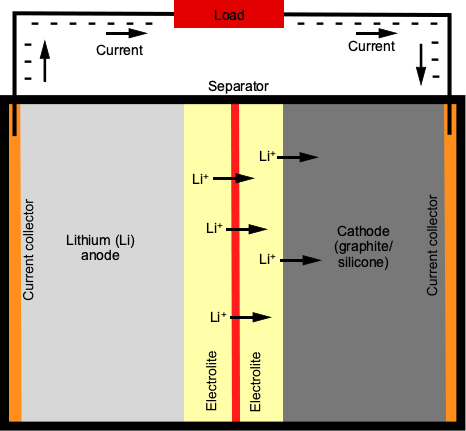
Over the last two decades, advances in understanding and implementing battery chemistry solutions have more than tripled the energy density of Li-ion batteries at the cell level. The specific gravimetric energy of Li-ion batteries has increased from approximately 80 Wh/kg (circa 2001) to 450 Wh/kg (circa 2022), with corresponding volumetric energy densities rising from approximately 200 Wh/L to 700 Wh/L. However, as previously discussed, these values are still low in comparison to Avgas or Jet A-1 fuel, which have a specific (mass) energy that is nearly 50 times higher at about 12,000 Wh/kg and a volumetric energy density that is about 14 times higher at 10,000 Wh/L.
Further gains in battery cell‐level energy density now seem more incremental as material limits are approached. Current research focuses on high-nickel layered oxides (>90% Ni), silicon-dominated anodes, and solid-state electrolytes, which together may push energy densities toward 500–600 Wh/kg. Alternative chemistries, such as lithium-sulfur and lithium-air, hold promise but face significant challenges in terms of cycle life, safety, and manufacturability. Even with these next-generation cells, the considerable energy difference between electrochemical storage and hydrocarbon fuels poses enormous challenges for the electrification of aviation.
What is lithium?
Lithium is a chemical element with the symbol Li and atomic number 3. It is the lightest metal and belongs to the alkali metal group in the periodic table. Lithium is highly reactive and has a silvery-white appearance. It is commonly found in small amounts in the Earth’s crust and primarily obtained from spodumene, petalite, and lepidolite. Lithium has various industrial and commercial applications, one of which is in rechargeable lithium-ion batteries.
Batteries also have an energy conversion efficiency. Battery energy conversion efficiency refers to the extent to which a battery effectively converts its stored chemical energy into usable electrical energy during discharge. For modern lithium-ion batteries, discharge efficiency is typically 90–95%, meaning most of the stored energy can be delivered to an electrical load. If charging losses are included, the net efficiency is about 85–95%. Efficiency varies with temperature, discharge rate, and battery age. Remember that in electric aircraft, this battery efficiency is just one part of the total system efficiency, which also includes losses in the motor, electronics such as the Electronic Speed Controller (ESC), wiring, and the propeller.
Battery Concerns for Aviation
Several key concerns regarding the use of batteries on aircraft include installation losses, thermal effects, longevity, safety concerns, and associated costs. To address these concerns, the aviation industry is actively researching and developing advanced battery technologies, enhancing safety protocols, and integrating electric and hybrid-electric propulsion systems into aircraft. These efforts aim to harness the benefits of battery technology while mitigating the associated risks and challenges to enhance aviation’s safety, efficiency, and sustainability.
Installation Losses
The electrical metrics quoted for Li-ion batteries are also better than “pack-level” metrics, which must consider installation losses. These losses include the “hidden” weight of the wiring from the batteries to the motor, insulation, structural materials, and the cooling systems required. Still, they will not otherwise contribute to its energy storage capacity. Such considerations can add at least 20% to the cell-level battery weights. Therefore, it is essential for aircraft design that allowances for such factors be included in the weight estimates and performance evaluations of electrically powered aircraft.
High Discharge Rates
For electrically powered aircraft, the battery discharge rates are significantly higher than those of an electric road vehicle. One problem is that they also get hotter when the batteries discharge quickly. Heat generation shortens the battery’s life and requires specialized cooling systems to mitigate a temperature rise. Aircraft batteries will likely go through multiple deep discharges and thermal cycles per day. The high power demands of takeoff and climb-out will result in exceptionally high battery discharge rates and thermal management issues, which, if not appropriately controlled, can seriously reduce the number of duty cycles a battery achieves.
Safety Issues
Li-ion batteries can be hazardous if not carefully monitored and protected with temperature, voltage, and current sensors that track the condition of each battery cell, such as through the use of a battery management system. Because a typical battery pack to power an aircraft may have tens or hundreds of individual cells, just as many protection sensors and circuits are needed. The reported incidents involving Li-ion batteries in aviation have been attributed to faulty cells exceeding their safety limits, often leading to thermal runaway. Thermal runaway is a chain reaction within a battery pack, where exothermic reactions occur in one cell and then spread to neighboring cells, potentially causing a fire or explosion of the entire battery pack. If not catastrophic, this situation can still pose significant risks to an aircraft and its occupants.
Hidden Carbon Footprint
The carbon footprint of the Li-ion battery production process is a crucial consideration when evaluating the overall emissions from electric aircraft. The production of batteries generates its own environmental and climate-related issues. Most global lithium supply comes from China and Chile, where extraction methods have been heavily criticized for causing environmental damage. Lithium, a silvery metal, is not easily obtained from mining and requires 500,000 gallons of water to extract one ton of lithium from the earth. This water becomes contaminated and cannot be released back into the environment without treatment.
The carbon footprint associated with manufacturing Li-ion batteries is challenging to quantify and may be substantial. However, carbon savings will likely offset it in the long run. GHG emissions from battery production are typically 60 kg CO2/kWh. However, it is worth noting that the emissions from battery production are a one-time upfront cost, whereas fossil-fueled aircraft emit GHGs throughout their operational life. The continued decarbonization of the electric grid system, utilizing solar and wind energy, will also play a crucial role in reducing the overall carbon footprint of electric aviation.
Battery Replacement Cycles
The frequency of battery replacements for an electrically powered aircraft still needs to be determined. Most research on battery aging has focused on automobiles, many of which have reached the end of their useful lives. Battery usage in an electric aircraft will differ from that in electrically powered road vehicles, partly as a result of the higher energy and current draw rates, as well as the accompanying thermal factors.
Without specific battery age modeling for aircraft, a Li-ion battery typically has a lifespan of 3,000 duty cycles. This life span roughly equates to an aircraft performing four daily flights for two years. Once this lifespan is reached, the battery must be discarded and replaced. It is likely that future certification requirements, such as under FARs or EASA rules, will require that the batteries be replaced more frequently than 3,000 cycles to ensure a safe operational life without the possibility of failure, i.e., a standard regulatory safe-life policy used for many other aircraft components.
Future of Battery Technology
Lithium battery technology has seen significant advancements, with a notable increase in energy density since 2010 and a doubling in the last fifteen years, as shown in the timeline below. This upward trend is because of various improvements in materials, design, and manufacturing processes. Innovations such as solid-state electrolytes, silicon anodes, and advanced cathode materials have played vital roles in enhancing the performance and energy density of lithium batteries. These advancements have helped extend battery life, reduce charging times, and increase overall efficiency, which is crucial for applications such as electric aircraft propulsion, electric road vehicles, portable electronics, and other forms of energy storage.
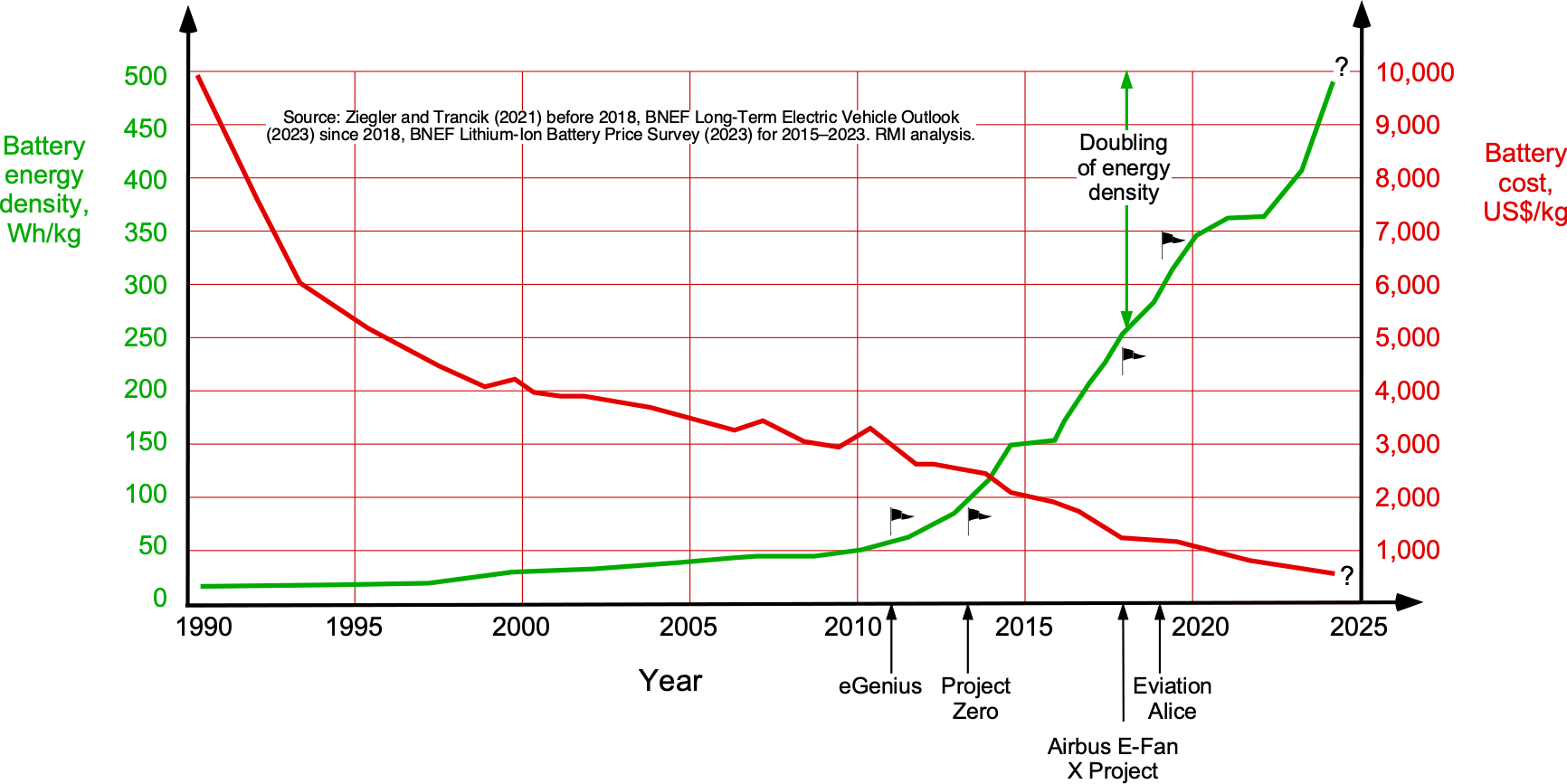
Further developments in battery technology aim to achieve a battery density of up to 1 kWh by the year 2050. In the short term, commercially produced high-energy, state-of-the-art Li-ion batteries that utilize cathodes made of lithium-nickel-manganese-cobalt-oxide or lithium-nickel-cobalt-aluminum-oxide can achieve energy densities of up to 450 Wh/kg. Further research and commercial development of lithium batteries could reach a capacity of up to 1 kWh/kg at the cell level by 2030. However, achieving Li-ion battery energy densities of over 500 Wh/kg will require significantly more technical advancements in battery technology and may even necessitate the development of different battery chemistries. Based on the current pace of battery research and the time it takes to translate this research into production batteries, energy densities greater than 500 kWh/kg may still be a decade or more away.
The cost of lithium batteries has also seen significant improvements over the past decade. According to various industry reports, the cost of lithium-ion battery packs has fallen from around US$1,100 per kWh in 2010 to less than US$150 per kWh in recent years, with some projections suggesting costs could drop below US$100 per kWh in the near future. These cost reductions make lithium batteries more viable for various applications, not just the aviation and aerospace fields.
Where does the electric power come from when I plug my electric-powered vehicle into an outlet?
The majority of electricity in the U.S., approximately 80%, is still generated from traditional fuel sources, such as coal, natural gas, and oil, which have a significant carbon footprint. Wind energy has experienced substantial growth in the U.S., now accounting for approximately 10% of the total, and is expected to continue increasing. Solar power accounts for approximately 3% of total electricity generation and is experiencing rapid growth. Hydroelectric power accounts for roughly 7%. Biomass (such as wood, agricultural residues, and dedicated energy crops) and geothermal energy contribute less than 1% to the total energy mix. Therefore, when you plug your airplane in for a recharge in the U.S., you still generate a substantial carbon footprint. Germany is a global leader in renewable energy adoption, with more than half of its electricity coming from renewable sources.
Power Chain Efficiency & Weights
It is essential to understand better how an electrically-powered aircraft’s power and the associated weight compare to what might now be called a “traditional” fossil fuel-powered aircraft. A modern turboprop or turboshaft engine has a net mechanical and thermodynamic efficiency of approximately 50%, meaning that 50% of the fuel energy can be converted into useful work to produce power at the engine shaft. A piston engine (sometimes called a piston-prop or piston aero-engine) has a lower net efficiency of about 35%. However, an electric motor’s net mechanical and thermal efficiency is much better, approximately 90%; this means that the motor converts 90% of the available energy into usable power. Therefore, one may be tempted to replace an ICE and its fossil fuel supply with an electric motor and a battery “because it is more efficient.” However, this decision requires a deeper justification through analysis.
Motor Efficiency & Weight
A turboshaft or turboprop has a shaft brake power-to-weight ratio, on average, of about 1.32 kW/kg (0.8 hp/lb) to 1.97 kW/kg (1.2 hp/lb). For piston-prop engines, their brake power-to-weight ratios are lower, averaging about 0.33 kW/kg (0.2 hp/lb) to 0.66 kW/kg (0.4 hp/lb). Yet, these values are still substantially lower than those of an electric motor, which can achieve, on average, brake power-to-weight ratios of 5 to 8 kW/kg. A nominal value of 5 kW/kg represents 2020 motor technology. While the values for an electric motor are desirable, a propulsion system on an aircraft also needs to be compared relative to the weight of the energy source carried onboard, which is contained in the batteries.
Battery Efficiency & Weight
One kilogram of Avgas or Jet A-1 fuel stores approximately 12 kWh of energy, 50 times more than a Li-ion battery pack, which holds only about 0.25 kWh of energy. Therefore, using these values yields a useful power available for a turboprop or turboshaft of approximately 6 kW per hour per kilogram when operating on Jet-A, equivalent to 6 kWh/kg (in terms of kilowatt-hours) or 8 hp/lb. For a piston-prop engine running on Avgas, the energy consumption is approximately 4.2 kWh/kg or 5.8 hp/lb. However, even with a 90% efficiency, the power available at the shaft of an electric motor running on a Li-ion battery is only about 0.225 kWh/kg or 0.3 hp/lb at the system level, which is significantly less than that of an ICE.
Net System Efficiency
At this point, it is possible to have better engineering clarity about the net system efficiency of an ICE propulsion system versus an electric propulsion system, at least in electrifying an existing aircraft with an ICE. The foregoing values are summarized in the table below, illustrating the high efficiency of an electric propulsion system but its poor overall net system efficiency in terms of brake power per unit weight. The primary reason for this outcome is that the high weight of the batteries reduces the net weight efficiency of any electric propulsion system.
Type | Efficiency | Power-to-weight (kW/kg) | Fuel/energy type | Fuel/energy brand | Energy density (kWh/kg) | Average available brake power (kWh/kg) |
---|---|---|---|---|---|---|
Piston engine | 32 – 35% | 0.30 – 0.33 | Gasoline/petrol | Avgas | 11.2 – 12.8 | 4.2 |
Turboprop | 45 – 50% | 1.22 – 1.32 | Jet fuel | Jet A or Jet A-1 | 11.9 – 12.5 | 6.0 |
Electric motor | 90–95% | 5.0 – 8.0 | Batteries | Li-ion | 0.22 – 0.25 | 0.225 |
For example, consider replacing a 150 kW (200 hp) piston-prop engine on a relatively small airplane with a payload of 400 kg (882 lb) when carrying a full amount of Avgas. If the engine has a mass of approximately 136 kg (300 lb), then an equivalent electric motor would have a mass of only about 20 kg (approximately 44 lb), as shown in the figure below. Running the piston-prop engine for one hour requires 150 kWh of energy, equivalent to the energy contained in 13 kg (28 lb) of Avgas. However, to run a comparable electric motor with the same shaft power for one hour would require at least 667 kg (1,471 lb) of Li-ion batteries, which is approximately 50 times the weight of a tank of Avgas. Similar arguments can be made for turboprops or turboshafts, in general.

Again, while an electrical motor’s low weight and high efficiency are extremely attractive, one begins to see the challenges of simply retrofitting an existing aircraft with an electric propulsion system, as it seems like a good idea on the surface. The power-to-weight ratio, or more specifically, the propulsion system’s energy-to-weight ratio, including the weight of the energy source, is crucial for an aircraft.
In this regard, the weight of the batteries needed for an electric propulsion system, even for a short flight, would quickly erode the aircraft’s payload capacity. It would not be a matter of maintaining the payload and increasing the aircraft’s gross weight. The certified weight of the aircraft is just that, and for a good reason, so flying an overweight aircraft is not only foolish but illegal. In the process of aircraft design, which is essentially a point design, it is rarely sufficient to change out a propulsion system without it necessitating a significant redesign of the entire aircraft.
Check Your Understanding #1 – Retrofitting a turboprop with an electric motor & battery pack
A turboprop engine has a rated power of 746 kW and a mass of 227 kg without the propeller. Estimate the mass of an equivalent electric motor plus the needed mass of batteries to run this electric motor at the same rated power as the turboprop for one hour. Assume the turboprop has an efficiency of 50% and the electric motor is 90% efficient.
Show solution/hide solution.
This analysis applies to a 746 kW turboprop engine with a mass of 227 kg (weight of 500 lb). On the one hand, a turboprop has a power-to-weight ratio of about 1.32 kW/kg (0.8 hp/lb) to 1.97 kW/kg (1.2 hp/lb) and an efficiency of about 50%. On the other hand, an electric motor has a power-to-weight ratio of 5 to 8 kW/kg and an efficiency of 90%. Assuming the turboprop has the lowest average value of the power-to-weight ratio of 1.32 kW/kg and the electric motor has the highest average power-to-weight ratio of 8.0 kW/kg, then the equivalent electric motor would have a mass of
which is significantly lighter than the turboprop engine! However, running this electric motor for one hour at its rated shaft power would require 746 kWh. With a battery gravimetric energy density of 0.256 kWh/kg, the needed battery weight will be
which is a lot of heavy batteries! For comparison, the turboprop engine would need only about 62.17 kg (137 lb) of jet fuel. Notice that the energy density of jet fuel is about 12 kWh/kg. Therefore, it is difficult to justify replacing the turboprop, except for experimental flight testing to support research and development.
Aircraft Weight Considerations
The power and energy demands for the flight of any aircraft depend on its airspeed, rate of climb, operational altitude, thrust or power required, and engine characteristics. For a fossil fuel-powered aircraft, the weight of fuel carried is generally a significant fraction of the takeoff weight. It costs fuel to carry fuel, but the aircraft becomes lighter and more efficient as fuel is burned off. The thrust and energy demands for flight decrease in proportion to the square of the reduction in fuel weight, so the improvements in efficiency as fuel is burned off are significant. However, the weight of an electrically powered aircraft remains constant throughout the flight because all the energy is stored in fixed-weight batteries.
At the most basic level, the gross takeoff weight, , of a conventional (i.e., non-electric) aircraft can be expressed as the sum of its empty weight,
, plus the useful load,
, i.e.,
(4)
The aircraft’s empty weight comprises its structure, the engines, internal fixtures, oils, hydraulic fluids, etc., and everything else it needs to be ready to fly, but without loading any payload or fuel. The useful weight, , is the sum of the payload weight,
, and the fuel weight,
, i.e.,
(5)
Payload refers to the weight that the airplane carries, which pays the bills, including passengers, baggage, and cargo. But fuel is not payload.
The takeoff weight must always be less than or equal to the maximum allowable (officially certified) maximum gross weight of the aircraft, . Therefore, the gross takeoff weight of the aircraft,
, will be
(6)
The empty weight, , is
(7)
where is the airframe weight and
is the weight of the powerplants (motors or engines). Therefore,
(8)
Another way of expressing this latter sum is in terms of weight ratios, i.e., a component weight as a fraction of the gross takeoff weight. Therefore, in this case
(9)
or
(10)
where the values are called weight fractions.
For a traditional (i.e., fossil-fueled) aircraft, the values of the empty weight fraction, , can vary from about 0.6 to as low as 0.5 for general aviation airplanes and from about 0.55 to 0.45 for commercial jet airliners. This means that useful load fractions,
, average between 0.55 and 0.4 for conventional aircraft. This value must be split between the “wet” fuel fraction,
, which is required to carry a specific payload over a certain flight range, depending on the aircraft and engine efficiencies. The payload fraction,
, comprises the number of passengers, cargo, or other items that generate revenue. Trades between the allowable payload and the achievable range apply to all traditional fossil-fueled aircraft.
For a battery-powered aircraft, however, the weight of the aircraft remains the same at landing as it was at takeoff. The same weight fraction sum still applies, but now the weight fraction of batteries, , becomes a permanent (fixed) part of the empty weight fraction of the aircraft (rather than a diminishing fuel weight), i.e.,
(11)
The question is the battery weight fraction and what is left as a payload fraction. The answer is that with existing technology, the battery weight fraction dominates over the payload fraction. Indeed, the payload fraction for an electrically powered aircraft may be at most 0.1, i.e., 10% of gross weight. Such low payload fractions are not economical, especially for an airline.
What is a “carbon footprint”?
A carbon footprint is a metric that refers to the amount of greenhouse gas emissions, primarily CO2, that are released into the atmosphere as a consequence of a specific human activity. Everyone has a carbon footprint; even breathing contributes to it. In general, a carbon footprint measures the impact that individuals, organizations, vehicles, aircraft, and other entities have on climate change. Various activities contribute to carbon footprints, including burning fossil fuels, industrial processes, deforestation, and producing (and disposing) goods and services. By assessing carbon footprints, such as from aircraft, it becomes possible to identify areas where emissions can be reduced or mitigated to lessen the longer-term environmental impact.
Flight Profiles & Missions
The types of flight profiles or missions that can be satisfied by electrically powered aircraft are identical or similar to those of existing aircraft. However, with current battery technology, flight ranges will inevitably be shorter, and the payloads that can be carried will be significantly lower. Furthermore, it is not realistic to retrofit any existing aircraft powered by ICEs with electric motors and expect it to retain the same level of performance.
A typical flight profile for an electrically powered aircraft is one where the aircraft flies from A to B. It will include a takeoff, climb, cruise to the destination, descent, and landing, as shown in the figure below. The cruise condition is predominantly in straight-and-level, unaccelerated flight at a relatively constant airspeed. A contingency plan for a possible diversion, which would prevent landing at the destination, must be anticipated by regulation. This will require significant reserve battery energy to be accounted for in the planned flight, thereby shortening the feasible range on a single battery charge. Recharging at intermediate stops along the route may also be necessary and should be considered when planning the flight.
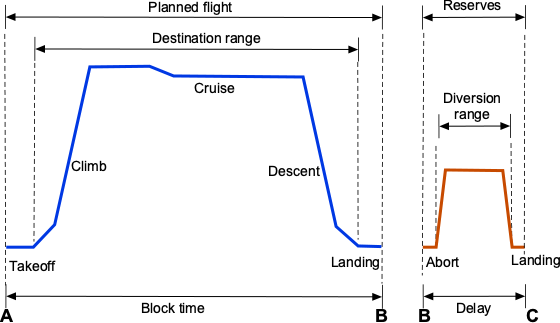
Other missions for an electrically powered aircraft may involve an out-and-return flight profile, i.e., flying to a destination to conduct some operation and then returning to base without a landing, which is typical of what is routinely done using drones. UAVs and drones have been in use for the last two decades, meeting numerous military and civilian requirements. These aircraft typically have shorter range and endurance goals, lower net energy requirements, and smaller, lighter battery packs. Such drone missions may involve photography or surveying. The task for a military drone may include reconnaissance or weapon delivery, which have proved effective in recent conflicts.
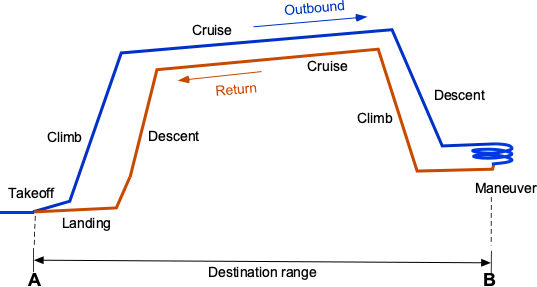
Short flights of less than an hour in an electrically powered aircraft make the significant weight penalty of the batteries feasible. In general, however, the energy required for longer flights means that the battery weight would quickly become prohibitive, eroding the aircraft’s payload and range. A commercial airliner’s payload consists of fare-paying passengers and cargo, making it easy to see how it could quickly erode to uneconomic thresholds. The volume of batteries also becomes another consideration when deciding where to put them inside the airframe. To maintain the correct center of gravity of the aircraft, the batteries and associated heavy wiring must be carefully positioned.
Power Required for an Electric Aircraft
For electric aircraft, the power required for flight is supplied by the batteries and must pass through several stages of energy conversion, each with associated losses. These losses include the battery discharge efficiency , electronic speed controller (ESC) efficiency
, motor efficiency
, wiring efficiency
, and propeller efficiency
. The product gives the overall system efficiency
(12)
Typically, the net system efficiency will be between 70% and 80%. Propeller efficiency will depend on the operating advance ratio or “ value,” which can be determined from propeller charts, assuming these are available. For example, propeller performance charts are available at the UIUC Propeller Data Site based on wind tunnel measurements for a wide range of smaller propellers suitable for electric airplanes and drones.
The power required at the battery terminals to sustain steady, level flight is determined by the aerodynamic drag and the flight speed, corrected by the system efficiency. The propulsive thrust required, , is equal to the total drag in steady level flight, and assuming the validity of the drag polar
, then
(13)
where and
is the true airspeed (i.e.,
). The lift coefficient is determined using
(14)
where lift equals weight, i.e., . Substituting
into the drag expression and multiplying by
gives the electrical power required from the battery, i.e.,
(15)
Expanding this latter expression gives
(16)
where the first term is the non-lifting or parasitic/profile power, and the second term is the induced power. The power required equation may be written in the canonical form
(17)
where the constants are
(18)
Equation 16 gives the power requirement in terms of flight speed , in-flight weight
, and the aerodynamic parameters
and
, the wing area
, as well as the total system efficiency, including electrical and propeller losses. This is the fundamental relationship governing the power demand of a pure electric aircraft in steady, level flight.
The qualitative shape of the power-required curve as a function of airspeed for an electric airplane is the same as that of a conventionally powered airplane in that it exhibits a characteristic “U”-shape. Higher power is required at low airspeeds because of higher induced drag, a minimum at the most efficient cruise airspeeds, and increasing power at higher airspeeds from the buildup of parasite drag. The only distinction is that the actual electrical power drawn from the battery depends on the total system efficiency, . Therefore, while the aerodynamic power profile remains unchanged, the battery power required is proportionally higher depending on the net losses in the electric powertrain.
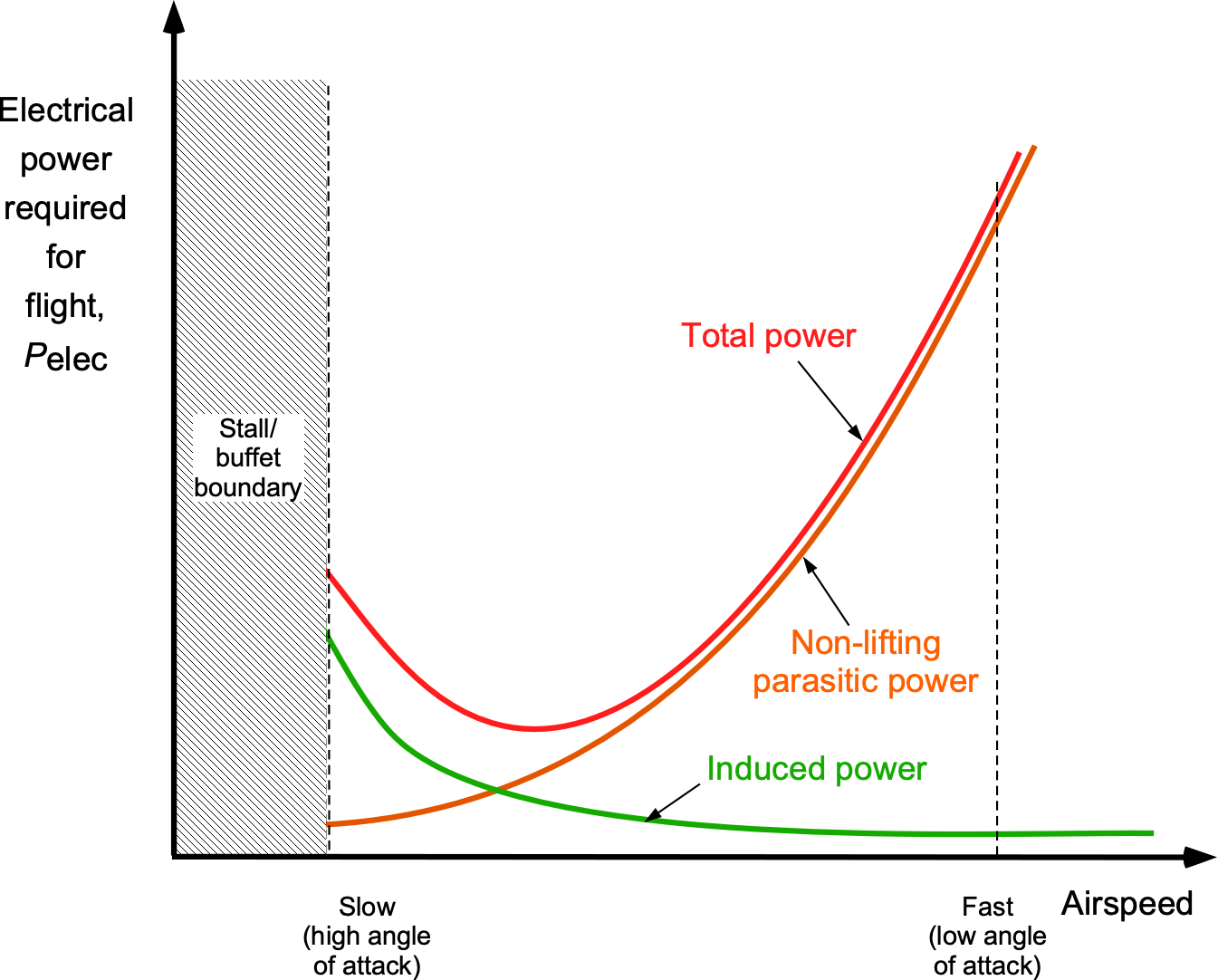
Payload & Range of Electric Aircraft
While an aircraft burning fossil fuel will be considerably lighter when it lands than when it takes off, a battery-powered aircraft will have the same weight throughout the flight. The range of a battery-powered aircraft can be expressed as
(19)
where is the takeoff weight,
is the weight of the batteries, and where
is the stored energy per unit weight of the battery pack, i.e., the gravimetric energy density. Therefore,
(20)
The efficiencies ,
,
,
and
are the efficiency of the battery, ESC, motor, wiring, and propeller, respectively; the net or total efficiency
will typically be about 0.7 to 0.8. Recall that the propeller efficiency will depend on the operating advance ratio or “
value,” which can be determined from propeller charts.
Therefore, to maximize the flight range of an electrically-powered airplane, which is not much different from a fossil-fueled aircraft, it must be flown in such a way that:
- The motor (and its electrical power chain) and propeller must operate at or near their respective maximum efficiencies.
- The battery must have as high an energy density as possible and be fully charged.
- The airplane flies at or near its best lift-to-drag ratio
.
- The battery pack, controller, power cables, and other components must be as lightweight as possible.
As previously discussed, the net battery weight, , on an electric aircraft (which includes cabling and other electronic components to regulate and protect the batteries) is a significant fraction of the gross aircraft takeoff weight,
. Based on current technology, the value of
is typically 0.4 to 0.5 for an electrically-powered aircraft. For the same energy storage as aircraft using an ICE, for which the fuel fraction is 0.3 or less, it is not difficult to understand why an electric aircraft will have a limited payload and flight range.
The payload-range characteristics of any aircraft, illustrated in the figure below, reflect the fundamental trade-off between payload and fuel. When a conventional fossil-fuel-powered aircraft operates at maximum payload, the fuel tanks typically cannot be filled to their volumetric capacity because of takeoff weight limitations. This condition defines the left-most vertical segment of the curve, between points A and B. To achieve longer ranges, the payload must be progressively reduced to allow for increased fuel carriage, resulting in the sloped segment from B to C. Point C represents a ferry flight, which is an operational scenario in which the aircraft is loaded with maximum fuel but carries no payload. Such missions are typically used for repositioning the aircraft rather than for revenue-generating service.
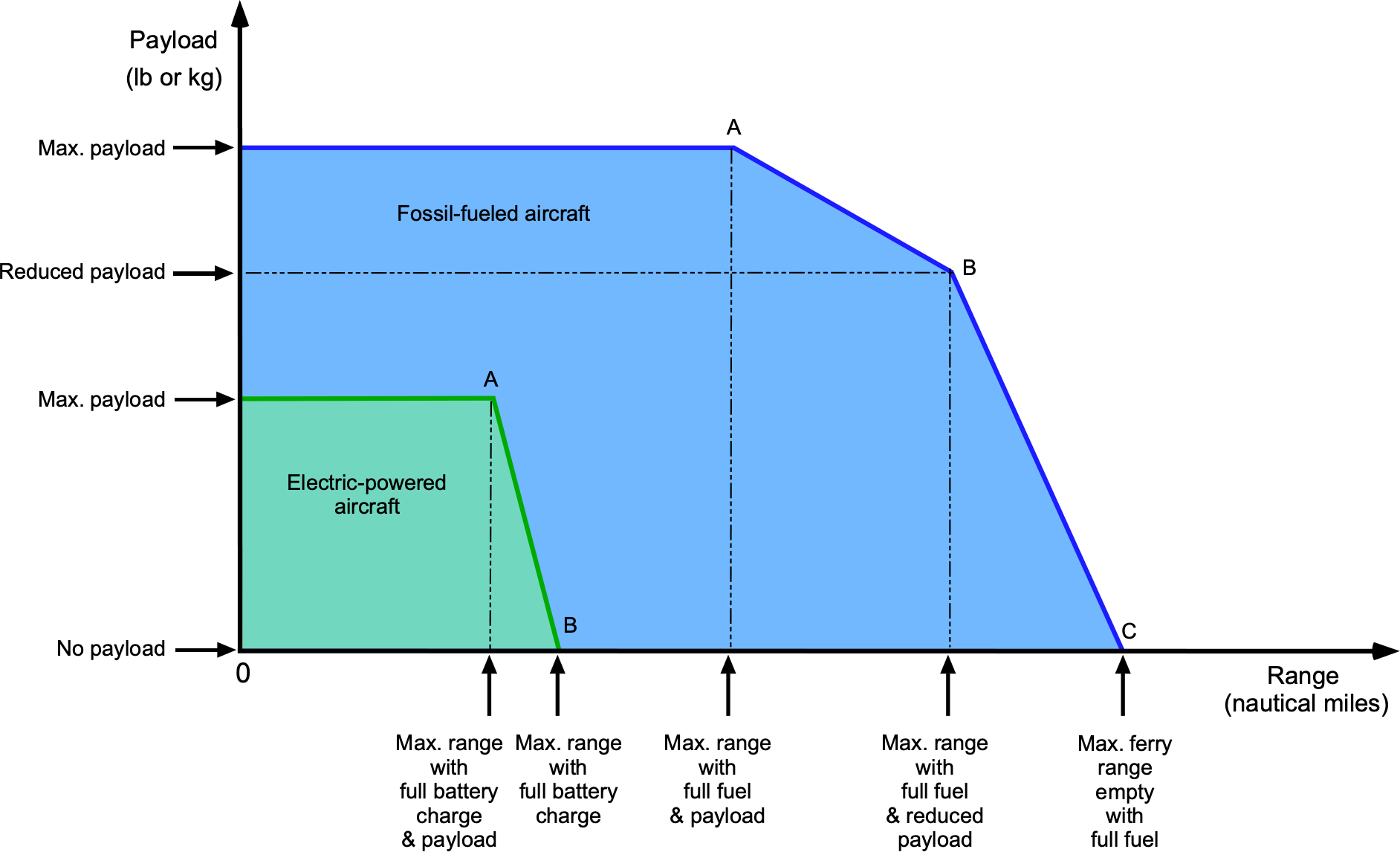
The payload-range characteristics of an electrically powered aircraft change significantly. All other factors being equal, the maximum payload is substantially lower than that of a conventional airplane because of the high specific weight of the batteries. In addition, the achievable flight range is relatively short, limited by the low energy density of current battery technologies. Reducing the payload decreases the required energy, allowing for a modest increase in range. However, because the overall payload fraction is already low, the gains in range remain limited.
Ultimately, the weight and size of all onboard components are critical factors in aircraft design, as they directly affect overall efficiency, range, and payload capacity. For electrically powered aircraft, lighter and more compact batteries enable higher payloads or longer flight ranges within the same takeoff weight constraints. While arguments based on environmental benefits are often compelling, they must be evaluated in the context of these fundamental performance trade-offs and design limitations.
Check Your Understanding #2 – Estimating flight time for an electrically-powered airplane
An electrically powered experimental airplane has a takeoff weight, , of 3,500 kg. It has an electric motor with a maximum power output of 300 kW. The onboard battery pack’s weight fraction,
, is 0.30 with a gravimetric energy density of
= 200 Wh/kg. The onboard instrumentation indicates that the electric motor is operating at a constant power output,
, of 250 kW during a cruise segment of the flight at an airspeed of 150 knots. Estimate this electric airplane’s flight time and distance, assuming that 50% of the battery energy is available for this flight segment. Assume an 85% net system efficiency.
Show solution/hide solution.
First, the weight of the battery pack is needed, i.e.,
Next, the available energy contained in the batteries needs to be determined, i.e.,
The energy available at the electric motor will be reduced because of the system efficiency, so the actual available energy is
If the motor is running at = 250 kW, then the time to use 50% of the available energy in the battery pack for the cruise segment will be
During this time, the aircraft will have covered a distance of 150 0.357 = 53.55 nautical miles. Note: The other 50% of the energy in the battery packs would need to be allocated for takeoff, climb, descent, and reserve purposes. Again, the challenges with batteries become apparent in that they comprise a significant weight fraction but do not allow an aircraft to have much flight time or range.
Hybrid-Electric Propulsion
Electric aviation includes all-electric aircraft, which rely solely on batteries or fuel cells, and hybrid-electric designs that combine internal combustion engines (ICEs) with electric motors. Hybrid power systems offer certain advantages while mitigating the limitations of purely electric propulsion. Hybrid architectures can offer a practical compromise by leveraging the high energy density and long-range capabilities of fossil fuels, while also benefiting from the efficiency and reduced emissions of electric propulsion.
In many cases, the ICE drives a generator that powers electric motors, or both the engine and motor contribute directly to propulsion. This flexibility enables the ICE to operate closer to its optimal efficiency, allowing for quiet, low-emission operation during taxi, takeoff, and descent segments. Hybrid systems can also incorporate regenerative energy capture during descent or braking to improve overall performance. As such, hybrid-electric propulsion represents a viable near-term solution to bridge the gap between conventional combustion-powered aircraft and the eventual adoption of fully electric flight.
Several prototype and demonstrator aircraft illustrate the application of these principles. The Ampaire Electric EEL is a retrofitted Cessna Skymaster, as shown in the photograph below, that uses a parallel hybrid drivetrain, allowing both the piston engine and electric motor to provide propulsion. Diamond Aircraft’s DA40 hybrid demonstrator combines a small rotary engine with electric propulsion components to explore serial hybrid configurations. These and other projects signal growing interest in hybrid-electric aviation, particularly for short-range and regional flight operations where endurance and reliability are key considerations.
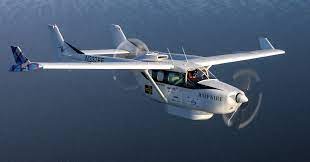
Power System
Hybrid propulsion systems can employ different configurations. For example, they can use an ICE to generate electricity, which is also used to power electric motors for propulsion, as shown in the schematic below. This combination allows the ICE to operate at its most efficient power output while reducing emissions compared to using it directly for propulsion. Additionally, hybrid systems can utilize regenerative braking and energy recovery systems to improve efficiency further and extend flight range. Of course, these hybrid power systems have been used with automobiles for over a decade.
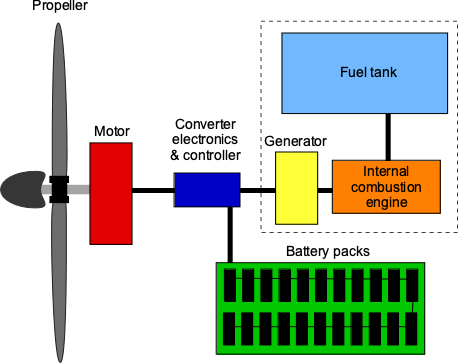
The two main types of hybrid-electric propulsion systems for aircraft are serial and parallel hybrid. In the serial hybrid, an ICE generates electrical energy that charges a battery and/or powers the electric motor, which in turn spins the propeller. In the parallel combination, an ICE drives the propeller directly. However, its work is supported by an electric motor during take-off and climb.
While there are performance and weight trade-offs associated with all hybrid systems, the primary benefit is that hybrid propulsion systems can offer many of the advantages of electric propulsion systems, as illustrated in the figure below, while mitigating their drawbacks. As such, hybrids are an excellent near-term solution before all-electric aircraft become feasible. Hybrid propulsion systems may also alleviate some of the certification challenges for a pure electric aircraft, but this remains to be seen.
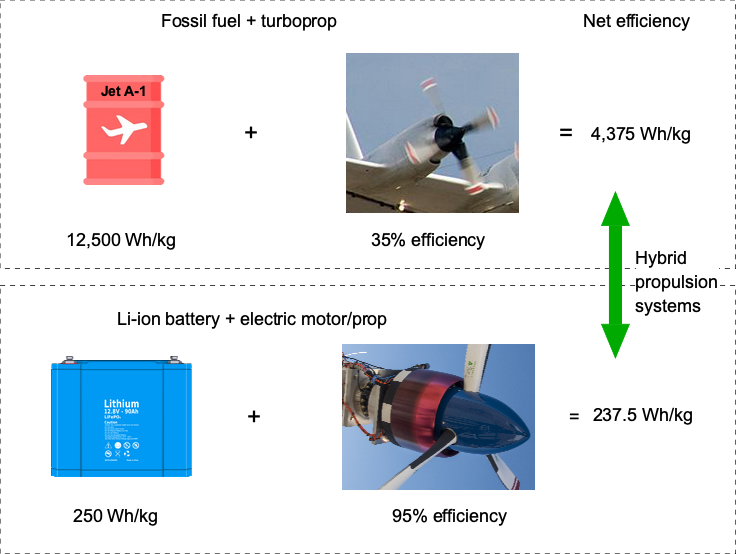
Power & Flight Analysis
At any instant during flight, the total propulsion power must be supplied by a combination of engine output and battery discharge, i.e.,
(21)
where is the shaft power provided by the engine,
is the net power drawn from (or charged into) the battery (positive when discharging), and
is the power required by the propulsion system to sustain flight at speed
.
Over the full mission duration , the total required energy is
(22)
and the energy provided by the hybrid system must satisfy
(23)
Here, is the total shaft energy from the internal combustion engine, and
is the battery’s stored energy. The battery charge–discharge efficiency is
.
The engine energy is derived from fuel combustion, i.e.,
(24)
where is the lower heating value of the fuel,
is the fuel mass consumed, and
is the shaft efficiency of the engine. The instantaneous fuel power conversion is given by
(25)
The total fuel mass consumed is
(26)
The battery provides additional or backup propulsion power, and its usable energy is
(27)
where is the gravimetric energy density of the battery (typically in Wh/kg) and
is the battery mass. The effective usable energy is
.
The propulsion power required at a given airspeed is
(28)
with the aerodynamic drag being given by
(29)
Here, is the propulsive efficiency,
is the ambient air density,
is the wing reference area, and
is the drag coefficient. Again, careful optimization of aerodynamic design, wing loading, battery capacity, and fuel allocation is essential to achieving efficient, long-range, or long-endurance hybrid-electric flight.
As with any aircraft, an electric or hybrid-electric airplane can only carry a specific payload over a given range, as illustrated in the figure below. Longer ranges can be achieved by reducing the payload, for example, by limiting the number of passengers or the amount of cargo. A pure electric aircraft, operating at maximum payload, may reach a range corresponding to point A. To fly farther, the payload must be reduced to allocate more weight for energy storage, thereby extending the range.
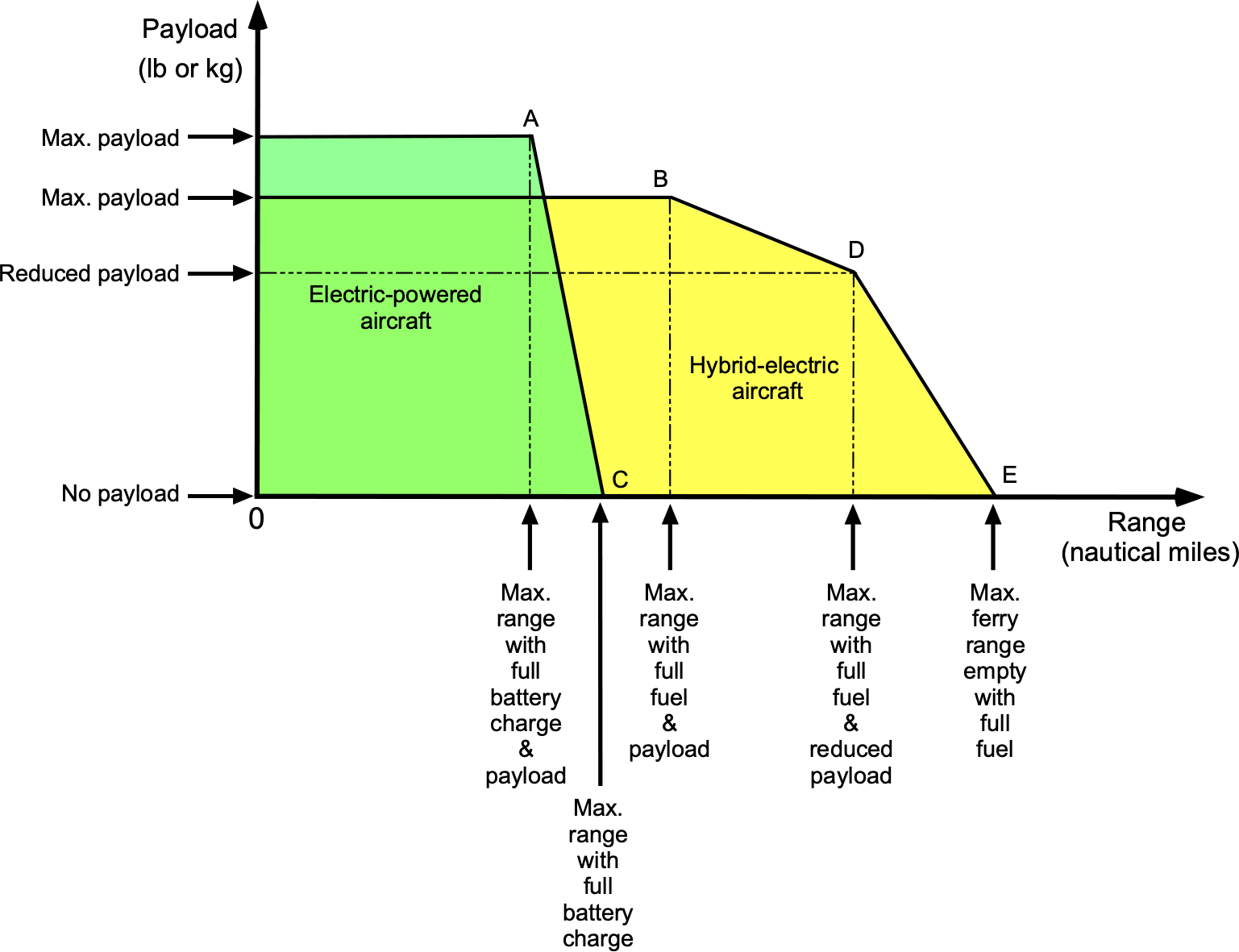
Hybrid-electric aircraft have a different trade-off. While a hybrid-electric configuration is likely to have a higher empty weight fraction than a comparable all-electric design because of the added weight of the ICE, fuel system, and associated components, it benefits from the higher energy density of liquid fuel. Consequently, it may carry its (somewhat lower) payload to a longer range, denoted by point B. Further reducing the payload allows the range to be extended even more, up to point D, assuming the aircraft is operated to its fuel limits.[3] Point C (for the electric case) or E (for the hybrid case) represents a ferry flight, a mission flown with the aircraft’s full energy capacity (battery charge and fuel) but with zero payload. This operating point maximizes the achievable range but does not contribute to revenue service.
Solar-Electric Propulsion
Solar-electric aircraft harness photovoltaic (PV) power systems to sustain flight. PV power systems for aircraft are designed to convert incident solar irradiance into usable electrical energy using lightweight, high-efficiency PV cell arrays. For aviation use, the PV cells are made to be lightweight and flexible. They are typically integrated into the curved upper surfaces of the wings and fuselage, covering as much area as practically possible. Modern photovoltaic (PV) technologies used in aerospace applications typically achieve efficiencies of 20–25%. The electrical power generated generally is on the order of several kilowatts,[4] which can be used to drive electric propulsion systems or to charge onboard batteries. By harnessing sunlight with solar arrays and onboard energy storage, an airplane can fly for days without refueling while producing zero greenhouse gas emissions. This is ideal for applications such as continuous environmental monitoring, disaster response, and high-altitude communications relays.
Research into solar-powered flight began in the early 1970s with small, unoccupied airplanes, such as the AstroFlight Sunrise, which first demonstrated that lightweight PV cells could directly drive electric motors for sustained flight. In 1998, the Solar Challenger, a crewed airplane, crossed the English Channel using only solar energy, demonstrating the viability of human-piloted solar power. In the early 2000s, the NASA Pathfinder and then Helios prototypes achieved flights above 30 km altitude, thereby introducing the concept of high-altitude pseudo-satellites (HAPS) for telecommunications and Earth observation.
Solar Impulse 2, as shown in the photograph below, circumnavigated the globe on solar-only power, validating high-efficiency solar cells, ultra-light composite structures, and large-span wing designs in a single integrated system. It featured a 72 m (236 ft) wingspan, 200 m² (2,153 ft²) wing area, an empty weight of 2,300 kg (5,071 lb), a PV area of 200 m² (2,153 ft²), a PV efficiency of , and a battery capacity of 68 kWh (245 MJ). By balancing ultra-light composites with a low wing loading (approximately 23 kg/m² or 4.7 lb/ft²) and efficient motors (
), it required only 25 kW (33.5 hp) to cruise at 60 km/h (37 mph). It could sustain flight during nighttime hours on its stored electrical energy.
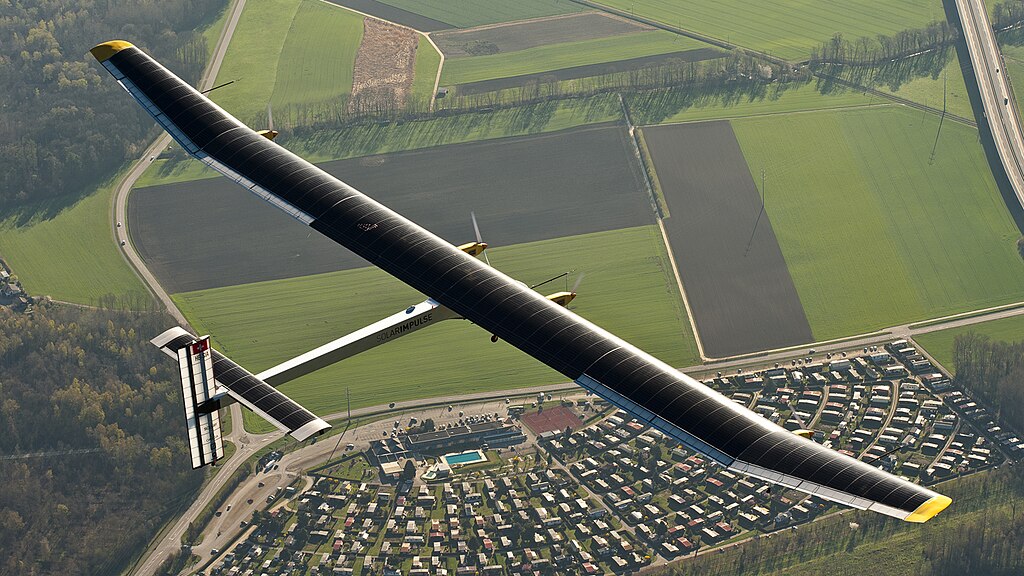
Photovoltaic (PV) Cells
Photovoltaic (PV) cells operate based on the photovoltaic effect, in which sunlight is directly converted into electrical energy. Each PV cell consists of a p-n junction, formed by combining two types of semiconductor materials: a p-type layer, which contains an abundance of holes (positive charge carriers), and an n-type layer, which has an excess of electrons (negative charge carriers). When sunlight strikes the cell’s surface, photons with sufficient energy excite electrons in the semiconductor lattice, freeing them from their atomic bonds and generating electron–hole pairs. The built-in electric field at the p-n junction drives electrons toward the n-side and holes toward the p-side, establishing a voltage difference across the layers. This potential difference drives a direct current (DC) through the load when the cell is connected to an external circuit.

In aviation applications, PV cells are often manufactured using lightweight and flexible materials, allowing them to conform to and be attached to curved aerodynamic surfaces such as wings or fuselages. The electrical power output of a PV cell is given by
(30)
where is the power output at time
(in Watts or W),
is the photovoltaic efficiency,
is the incident solar irradiance (in units of W/m2), and
is the surface area of the PV cells (units of m2). Obviously, a larger solar array will generate more power.
Power System
Because solar irradiance is inherently variable and operational conditions can fluctuate, solar-powered aircraft require a sophisticated energy and mission management strategy to achieve sustained flight beyond 24 hours. The core of this system is the Energy Management System (EMS). To maximize the electrical power extracted from photovoltaic (PV) cells, a Maximum Power Point Tracker (MPPT) is used. The MPPT is a DC/DC converter with a variable gain, incorporating electronics that continuously monitor the current and voltage of the PV cells and rechargeable batteries. By dynamically adjusting the gain, the MPPT ensures continuous operation at the photovoltaic system’s maximum power point.
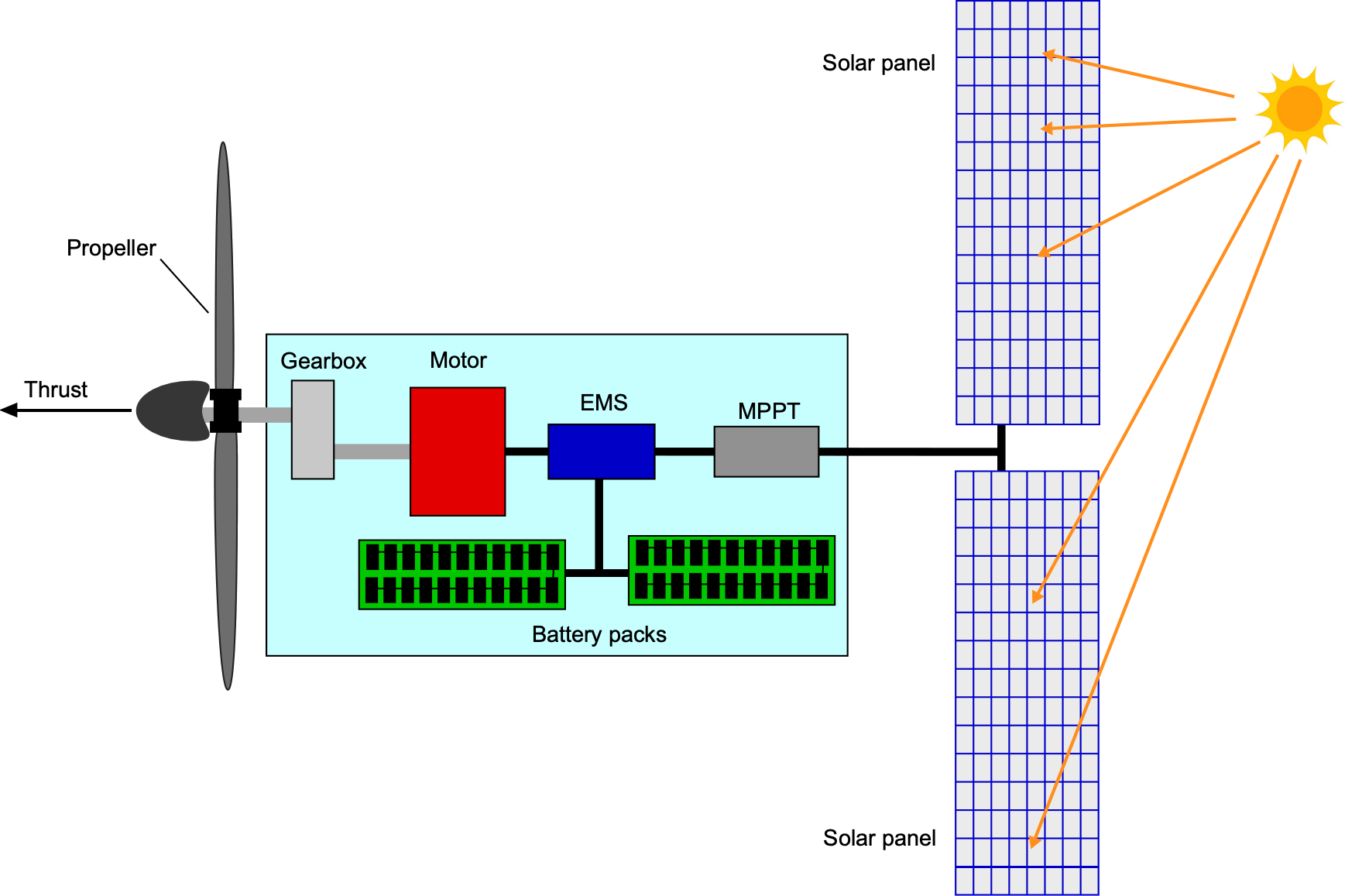
Power & Flight Analysis
The analysis of a solar-electric flight vehicle is straightforward. At every instant during flight, the power harvested from the sun plus the power drawn from or charged into the battery must equal the propulsion power required, i.e.,
(31)
where is the PV output,
the net battery power (positive when discharging), and
the shaft power needed for flight at a true airspeed
.
Over a full day–night cycle, the total solar energy collected between sunrise and sunset must cover both the energy required during daylight and that demanded at night, i.e.,
(32)
Defining daily solar energy and battery capacity
, the design constraints become
(33)
The instantaneous PV power is given by
(34)
where is the module efficiency,
the solar irradiance normal to the wing surface, and
the planform area covered by solar cells. Under clear-sky conditions near noon at mid-latitudes,
1,000 W/m
.
The battery must supply night-time propulsion and buffer diurnal fluctuations. Its usable energy is
(35)
with the gravimetric energy density (Wh/kg) and
the battery mass. A round-trip efficiency
accounts for charge–discharge losses, so the effective available energy is
. Modern lithium-ion batteries reach
250 Wh/kg and
0.95.
Finally, the propulsion power required at steady speed is given by
(36)
where is the propulsive efficiency, the drag being given by Eq. 29 with the factors affecting the drag being previously discussed.
Again, the wing loading plays a key role in determining cruise efficiency and overall aerodynamic performance. Increasing the wing area to enhance solar energy collection inevitably adds structural mass and wetted surface area, which can increase parasitic drag. Therefore, optimizing wing loading represents a critical design trade-off in solar-powered aircraft, where structural efficiency must be balanced against aerodynamic performance. Achieving long-endurance flight requires not only a high lift-to-drag ratio
and high propulsive efficiency
, but also an appropriately chosen wing loading
that minimizes the propulsion power required for sustained cruise. These considerations are central to the successful design of solar-electric aircraft.
Electrifying a Turbofan?
According to some claims, an electric motor driving the same fan stage can replace a turbofan engine. This all sounds easy, but this claim needs a deeper analysis. Remember that an electric motor would only replace the engine core, as shown in the figure below. Therefore, one immediate issue is the loss of jet thrust from the core of a turbofan engine, which accounts for approximately 30% of the total thrust. Another issue is the accessory components, such as pumps for hydraulics and pneumatics, which would still be required with an electric drive.
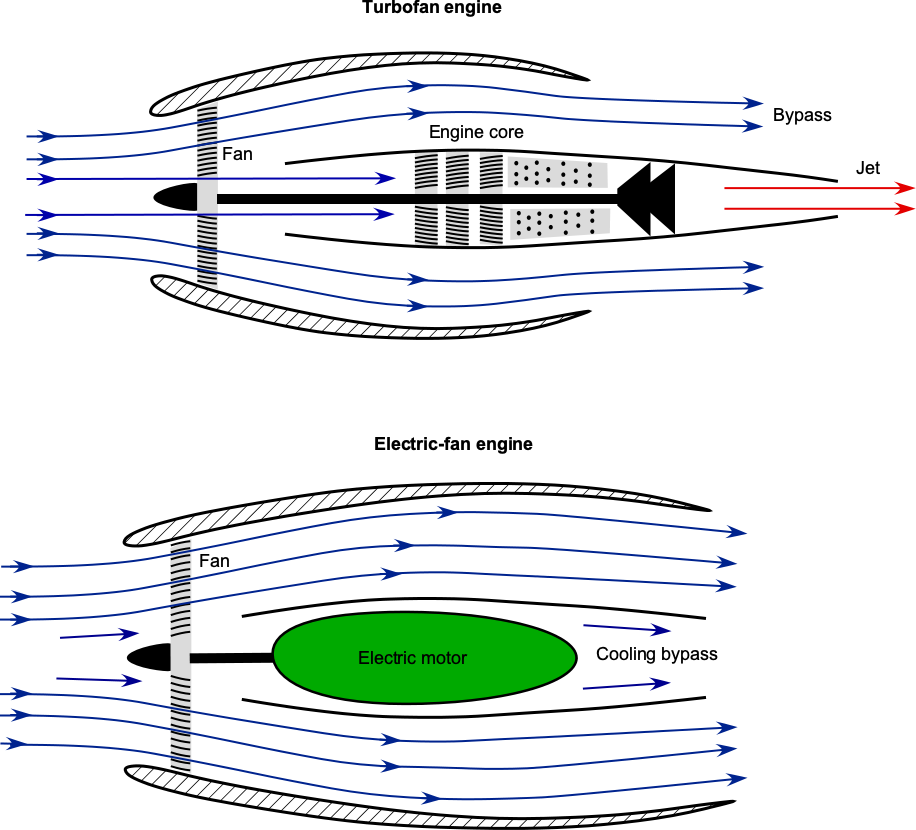
Therefore, if an electric motor were to drive the fan used in any particular turbofan engine with the same torque, rotational speed, and blade section Mach numbers (which affect efficiency), the resulting thrust would be lower. This “lost” thrust could be recovered using a larger fan or other design modifications. In the case of a bigger fan, if the fan is uniformly loaded, then the new “electric” diameter, , can be estimated in terms of the original diameter,
, by using
(37)
where is the required thrust and
is the lost thrust from the engine core. For a 30% loss of thrust, the new fan diameter will be about 20% larger.
The implication is that retrofitting a turbofan with an electric drive is not a plug-and-play replacement. Instead, it necessitates a substantial redesign of the propulsion system, including potential aerodynamic and structural modifications. Furthermore, larger fans exacerbate existing constraints on ground clearance for underwing engines, which is already a limiting factor in many current aircraft designs. On the other hand, an electric fan system would be significantly lighter than a conventional turbofan engine, which may partially offset the added mass of larger fans. Nevertheless, the high weight of current battery systems remains a fundamental challenge, especially for medium- and long-range flight profiles.
Assessing Costs
What does it cost to charge up and run an electrically powered aircraft? To answer this question, it is first necessary to compare the cost of electric power from the grid with the cost of equivalent energy from jet fuel. Industrial consumers of electricity in the U.S. pay, on average, about $0.075 (7.5 cents) per kWh. Jet A-1 fuel prices fluctuate daily, but in 2022, it was priced at approximately $820 per metric tonne. A metric tonne is 1,000 kg or 2,204.62 lb, which equates to about $0.82 per kg or $0.37 per lb. However, airlines typically pay less for their fuel by using a process known as “fuel hedging,” which allows them to fix fuel prices for a specified period, thereby mitigating the risk of price volatility.
Remember that at a system level, the usable power available at the shaft of a turbofan or turboprop is approximately 6 kW per hour per kilogram of Jet A-1. The corresponding power available from an electric motor is 0.225 kW per hour per kilogram of battery pack. Therefore, the cost of powering a jet engine is about $7.5 per kW per hour, and the cost of an electrically-powered engine will be about $3 per kW per hour, so 2.5 times less cost. This is an attractive outcome for an operator!
However, another significant cost consideration is the maintenance cost of the engines versus the replacement cost of batteries. Li-ion batteries typically reach 3,000 duty cycles before needing replacement, but FAA or EASA certification requirements may limit the batteries to 1,500 cycles or less for safety reasons. Turbofans and turboprops are reliable and may only need a major overhaul once every 20,000 flight cycles; such overhauls can cost hundreds of thousands of dollars. Typically, this works out to be about $200 per flight cycle for a turboprop to $500 per flight cycle for a turbofan.
For now, assume the battery replacement frequency is 1,500 cycles (flights). Consider a turboprop engine with a shaft power of 820 kW (1,100 shp). This means the maintenance cost for 1,500 one-hour flight cycles will be about $300,000 per engine or $200 per kWh. The cost of replacing the equivalent Li-ion battery pack for aviation use is about $500 per kWh, so 2.5 times the comparable maintenance cost of the turboprop per hour. While the energy cost per kW for electric propulsion is 2.5 times lower than that for a turboprop, this advantage is negated by the high cost of battery replacement. Based on this cost argument, the result is a zero net sum gain, which makes it challenging to justify electric propulsion. However, over time, battery costs may be reduced, resulting in a positive financial net gain in terms of cost per flight hour.
Electrically-Powered VTOL Aircraft
Electrically-powered VTOL (Vertical Takeoff and Landing) or “eVTOL” refers to an aircraft capable of vertical takeoff and landing and forward flight using one or more electric propulsion systems. eVTOL aircraft typically rely on multiple electric motors, each with its own propeller or rotor, to provide vertical lift and/or forward propulsive thrust. These aircraft are designed to combine the benefits of helicopters and fixed-wing aircraft, potentially offering the same benefits as another electrically powered airplane, while also featuring vertical takeoff and landing (VTOL) capability. The FAA refers to eVTOL aircraft as a form of “powered lift” and is subject to all the requirements and regulations applicable to this aircraft category. The ICAO does not currently recognize powered lift airplanes, which poses an interesting dilemma in the development and eventual certification of eVTOL aircraft.
The world’s first eVTOL aircraft, which was flown in 2009, was the Agusta-Westland Project Zero, as shown in the photograph below. This aircraft was an all-electrically powered, fly-by-wire tiltrotor concept that represented the state-of-the-art use of electrical motors and battery technology at that time. It was a demonstrator for technologies never previously flown on a rotorcraft, including individual blade control (IBC); however, it was never designed for production. Yet, the vehicle was to set the stage for many future eVTOL developments.
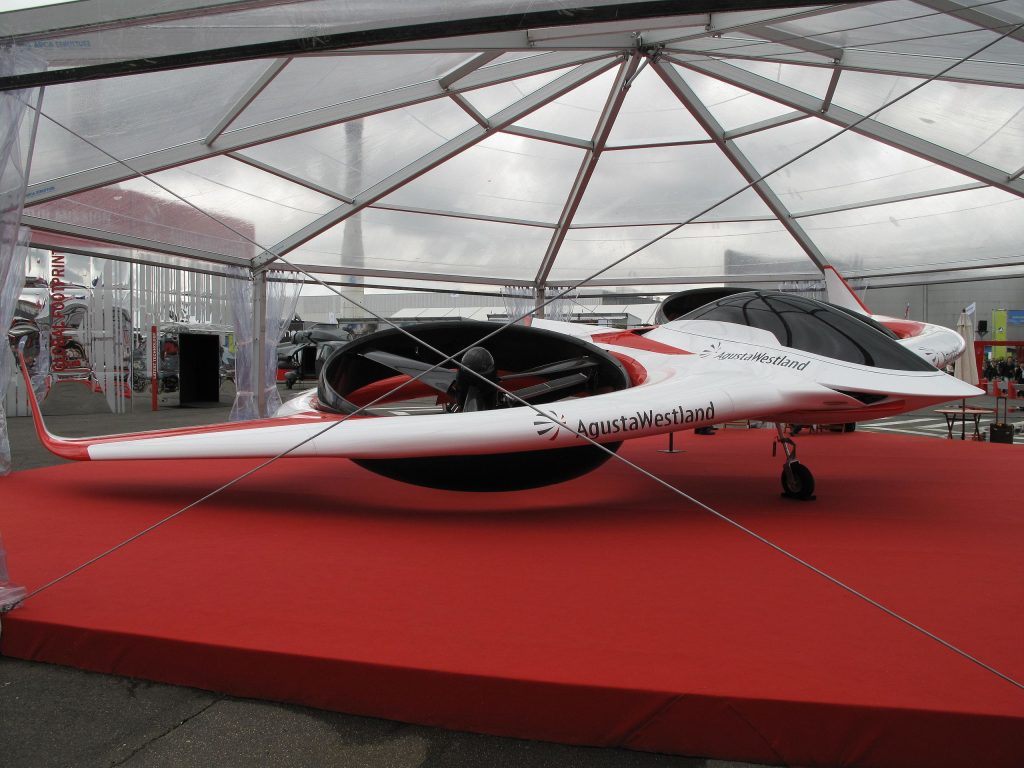
The design and development of other eVTOL aircraft have gained significant attention in the last decade, driven by continued advancements in battery technology and electric propulsion systems. These eVTOL aircraft are seen as potential solutions to enable Urban Aerial Mobility (UAM). This vision provides on-demand transportation services in congested urban areas, serving as a form of “air taxis.” The now-famous mantra of the eVTOL community is that such aircraft have the potential to revolutionize urban transportation by offering faster and more efficient travel, reducing congestion on roadways, and providing access to areas that are otherwise difficult to reach. However, like all other electrically powered aircraft, many challenges must be addressed before eVTOL aircraft can ever become a valuable part of the aviation spectrum.
Check Your Understanding #3 – Calculating the hovering performance of an eVTOL
A manufacturer of a proposed eVTOL concept with 12 rotors claims it weighs a total of 2,000 lb at takeoff, has an empty weight of 1,300 lb, and can carry a 300 lb payload for 10 minutes of hovering time. It is quoted that each rotor operates at a disk loading of 16.3 lb/ft2. What would be the weight of batteries needed to hover for this short time? Assume an efficiency (figure of merit) of 0.7 for each rotor, a net electrical efficiency of 85%, and sea level ISA conditions. Suggestion: Repeat the calculations in SI units by converting the information given in USC to SI.
Show solution/hide solution.
If the eVTOL has 12 rotors, then it can be assumed that each rotor carries 1/12th of the weight, , of the aircraft, i.e., each rotor produces a thrust of
The power required for each rotor, according to simple rotor (momentum) theory, is
where is the disk loading,
lb/ft
, and
= 0.7. Inserting the known values gives
where the air density at MSL ISA is 0.002378 slugs/ft3. Therefore, the total power required to hover will be
If the gravimetric energy density of a Li-ion battery is 0.256 kWh/kg, the needed battery weight to hover for 10 minutes (one-sixth of an hour) will be
Adding up the weights leaves 2,000 – (383.3 + 300) = 1,316.7 lb for the airframe, motors, rotors, wiring, and everything else, which seems reasonable based on the claims. However, 10 minutes is not enough flight time to be that useful.
eVTOL Configurations
Today, over a hundred established companies and startups are actively developing eVTOL aircraft that could meet the needs of Urban Air Mobility (UAM), as illustrated in the figure below. These companies are conducting research, building prototypes, and performing flight testing to bring these eVTOL aircraft to the marketplace one day. Many of these aircraft are autonomous and designed to fly without a pilot on board. While eVTOL aircraft have demonstrated promising potential, the widespread adoption and integration of these aircraft into the national airspace system will require further advancements, regulatory approvals, significant infrastructure development, and, not least, public acceptance. It will likely take considerable effort to convince the general public to step onto an aircraft without a pilot.
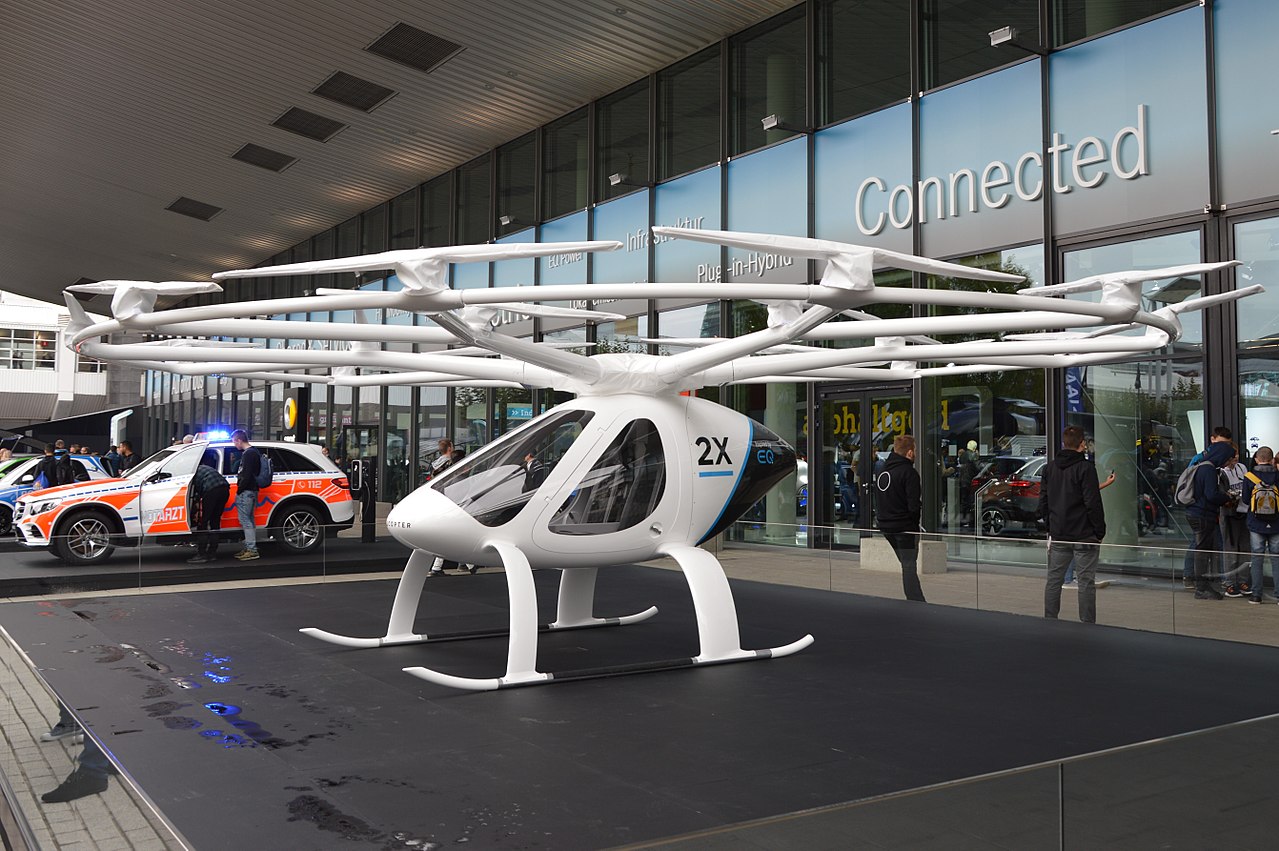
Some believe eVTOLs can function like terrestrial buses or rail services running over specific routes at certain times. However, the convenience of eVTOL vehicles that can take off and land directly at the customer’s location, other than a designated eVTOL port or heliport, will likely be another primary mission. eVTOLs will have to function similarly to existing taxis or, like Uber, provide easy, efficient, and relatively inexpensive point-to-point transportation for the general public. At least this is the vision.
While there are many proposed eVTOL configurations, as shown in the figure below, they can be broadly categorized into the following:
1. Oversized Drones: These configurations feature multiple propellers, reminiscent of existing drones, such as quadrotors. While some have a small enough footprint to fit in a front yard or on a city street, it is essential to consider the regulations and infrastructure required to accommodate them. If regulations permit, the smallest versions could pick up and drop off a few passengers at their location.
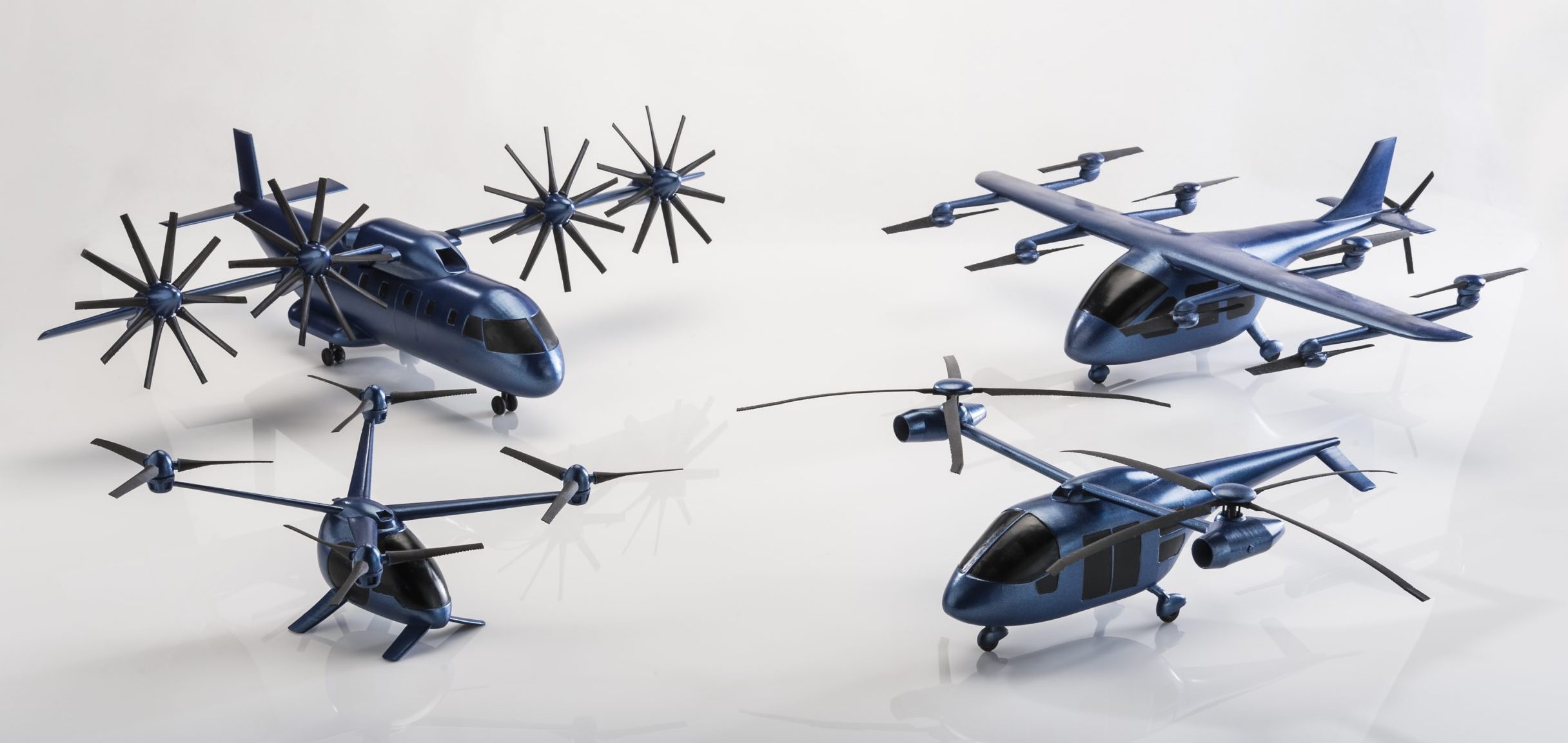
2. Modified Helicopters: Some proposed eVTOL designs resemble existing helicopters but with many more rotors or propellers. These vehicles often have a footprint similar to that of traditional helicopters, which may make it challenging for them to fit conveniently on city streets. Their long-term prospects for use in UAM are uncertain, particularly given potential regulatory and infrastructure limitations.
3. Rotor/Fixed-Wing Hybrids: Several eVTOL designs incorporate tilting wings and/or rotors, along with multiple propellers. These vehicles offer the advantage of requiring less energy in cruise flight than those with lifting rotors, such as helicopters. However, their larger footprint limits their suitability for UAM, most likely to designated landing areas such as at local airports.
4. Retractable Wings and Rotors: Some eVTOL solutions include vehicles with retractable or foldable wings and/or rotors. While they may sometimes be referred to as flying cars, they are more accurately described as drivable airplanes. It is unlikely such configurations would be technically or economically feasible for UAM because of their mechanical complexity, high empty weight and battery fractions, and limited payload fraction
Autonomous Flight
Autonomous flight refers to the ability of an aircraft to operate, navigate, and make decisions without direct human intervention. Autonomy may be needed for an eVTOL to make it useful and practical. Autonomy may involve using technologies such as artificial intelligence and machine learning combined with sensors and control systems to enable the aircraft to perform various tasks independently. Autonomous flight systems are designed to perceive and interpret the environment, plan and execute flight trajectories, and make real-time decisions based on sensor inputs and pre-programmed algorithms. These systems should also be able to handle tasks such as takeoff, landing, navigation, obstacle avoidance, and even responding to emergencies.
Aviation has different levels of autonomy, ranging from limited automation to full autonomy. These are some commonly recognized control levels:
- Pilot-in-Command (PIC): The aircraft is entirely under human control, with no autonomous features.
- Autopilot Systems: The aircraft features essential automated functions, such as maintaining altitude and heading, but a human pilot remains responsible for overall control and decision-making.
- Flight Management Systems (FMS): The aircraft has more advanced automation, including automated navigation, performance calculations, and guidance. However, a human pilot must monitor and intervene when necessary.
- Highly Automated Systems: The aircraft can perform most flight operations autonomously but requires human oversight and intervention in certain situations.
- Fully Autonomous Systems: The aircraft can operate and navigate without direct human control. It can perform all flight operations, including takeoff, landing, and navigation, without human intervention.
Autonomous flight systems can offer benefits such as increased safety, improved operational efficiency, reduced human error, and the ability to operate in challenging or dangerous environments. However, the vulnerability of autonomous flight vehicles to cyberattacks must also be considered because they rely on wireless communications. Attackers can use jamming devices or generate other wireless interference to disrupt the control signals, rendering the vehicle ineffective or causing it to crash. Various measures can be taken to mitigate vulnerabilities, including implementing encryption and authentication mechanisms, utilizing secure protocols, regularly updating software with secure coding practices, and employing intrusion detection systems.
The widespread adoption of fully autonomous flight for eVTOLs, or in any aspect of commercial aviation, is still some way off. Ensuring the safety, reliability, and integration of autonomous systems into existing airspace and infrastructure remains a complex challenge that requires extensive testing and validation. As previously mentioned, the more significant issue may be perception and convincing the flying public that it is safe to step onto pilotless aircraft.
Urban Aerial Mobility
A more provocative, if not critical, evaluation of how eVTOL can contribute to the transportation needs of the general public is needed. Such an evaluation should consider both technical grounds and accessibility, as well as convenience and cost. Besides the question of technical feasibility, the most obvious question would be: Will UAM be affordable to the public at large, or is it just another elitist proposition for the wealthy? For now, it appears more like a personal luxury service rather than a potential paradigm shift in urban mobility.
As shown in the image below, some think this will be a new aviation utopia, where everyone flies around doing their business and commuting to their homes in an eVTOL aircraft. But to be fair, there has also been a perception that electric cars are elitist; the evolving market dynamics and efforts to improve accessibility and reduce costs are gradually disproving this notion. Therefore, in time, the same may happen with eVTOL and UAM.
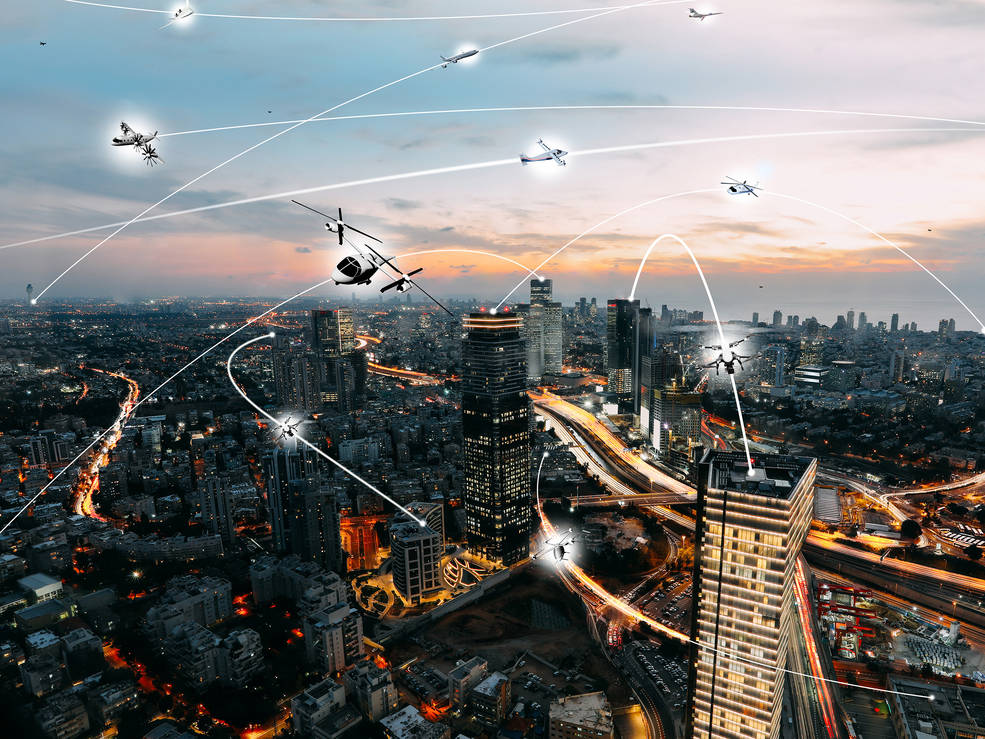
Assume that the technical issues with eVTOLs can be overcome, and they are then widely used in large U.S. cities, such as Orlando or Washington, D.C. Consider the following scenario. Each lane of an interstate highway, such as I-4 in Orlando or I-270 in Washington, D.C., has a flow rate of about 2,000 cars per hour. Assuming two occupants per car, this flow rate is 4,000 people per hour per lane. A three-lane highway can accommodate 12,000 people per hour, assuming no accidents or delays. Transit rail (e.g., MetroRail in Washington, D.C.) can carry even more, with a flow rate of up to 6,000 people per hour per track. Therefore, the question arises: how many eVTOLs would it take to offload the carrying capacity of one highway lane, or what could be achieved with MetroRail?
The answer is simple arithmetic. Assuming every eVTOL flight carried three passengers, there would have to be more than 2,000 eVTOLs in the air simultaneously. Based on an average journey time of 10 to 20 minutes, there would be up to 12,000 take-offs and landings per hour, and potentially over 500,000 eVTOL movements a day, where a “movement” is defined as either a takeoff or a landing. At the largest airports in the U.S., there may be as many as 2,000 movements per day. Therefore, it is hard to imagine any large metropolitan city accommodating 500,000 air traffic movements a day, even if it were an affordable form of transportation for the public.
The issue of weather is also a concern. Like many other aircraft, eVTOLs will not be able to fly in adverse conditions, such as low visibility, heavy rain, thunderstorms, or freezing conditions. The proximity of major airports is also a concern because of the potential for air traffic conflicts with commercial airliners. Air traffic control (ATC) decisions about who receives airspace and terminal access during times of congestion will undoubtedly contribute to delays and emergency diversions, and the batteries of eVTOLs will be quickly depleted. Popup ATC airspace restrictions, which are too frequent in the Washington D.C. area, could ground all air traffic for hours. UAM could then degenerate into urban aerial chaos.
Noise pollution is a significant concern regarding eVTOL aircraft. While many are relatively quiet on their own, the cumulative noise footprint of many of these aircraft flying over densely populated areas matters, which can result in a high level of public annoyance. Hundreds of eVTOLs zooming over houses in the suburbs every hour will likely result in a massive public backlash. Therefore, addressing the issue of noise to facilitate the realization of UAM will be crucial for public acceptance and successful implementation.
Even if eVTOL could provide an affordable service equivalent to a lane of interstate traffic or a line of MetroRail, it would have only a minimal measurable impact on the general public’s mobility. What will happen in the coming decades remains to be seen, but there are reasons to continue pursuing eVTOL concepts and electric propulsion methods.
Check Your Understanding #4 – Finding the maximum cruise range of an eVTOL
An eVTOL aircraft with tilting, electrically-powered rotors and a wing has a maximum gross takeoff mass, , of 1,200 kg. The wing has an area,
, of 10 m2. The drag polar is
. The rotors and power transfer have a net efficiency,
, of 70% from a Li-ion battery pack with a specific gravimetric power density,
, of 250 Wh/kg. The weight fraction of the battery pack is
= 0.33. For these parameters, calculate the best range cruise speed of the aircraft in level flight and the corresponding power required, assuming MSL ISA conditions. If 40% of the battery life is available for a cruise segment of the flight, what will be the best range of the aircraft when flying under these conditions?
Show solution/hide solution.
In forward flight, the lift generated by the aircraft equals its weight, and the thrust required is equal to its drag. For a propeller-driven aircraft, the best range efficiency occurs when the lift-to-drag ratio, , is at its maximum. To find this condition, the lift-to-drag ratio can be written as
We want to find the maximum value of or the minimum value of
. Differentiating the previous expression gives
So, solving for gives
with the corresponding value at this value of
given by
Therefore, the best (or
) for this aircraft is
The lift on the wing is equal to weight
, so
and rearranging gives the airspeed corresponding to this value of as
where . Substituting the numerical values gives
To find the power required for flight, we need the total drag force, , i.e.,
In level unaccelerated flight, =
, so that the net brake propulsive power required is
The energy available from the battery pack is
Therefore, based on the available battery energy, the maximum time of the cruising part of the flight will be
and the distance (range) traveled by the eVTOL aircraft during this time will be
Electrical Infrastructure
Developing an electrical charging infrastructure is crucial to enabling the adoption of any electrically powered aircraft, particularly for commercial purposes. In particular, eVTOL aircraft will require numerous charging stations, and in a large city, one of the immediate questions is where to locate them. The answer may be on the rooftops of buildings or in parking lots.
All airports, including the smaller regional airports, would also need to invest in charging infrastructure to provide the necessary power and rapid turnaround times for various electrically powered aircraft. To make economic sense, this aircraft charging infrastructure would need to accommodate the charging needs of various aircraft sizes and types, ranging from general aviation to commercial airliners to eVTOLs. It would be chaos if too many aircraft arrived at the same airport simultaneously for a battery top-off!
Another consideration is that charging electric aircraft requires more powerful and specialized charging solutions compared to charging electric road vehicles. The power and electrical current demands of aircraft charging are significantly higher than those of road vehicles, and the infrastructure must also be capable of supporting rapid battery charging to minimize turnaround times. In the meantime, efforts to electrify airport ground operations, such as ground support equipment, tugs, baggage carts and loaders, and maintenance vehicles, can provide a starting point for the development of the significantly upgraded electrical charging infrastructure needed to supply the power levels required to recharge electric aircraft.
Quantifying the load on the electrical grid, determining costs, and identifying the specific types and locations of charging stations required for electric aircraft will be critically important to the success of eVTOL and other electrically powered aircraft. Merely extending existing automotive fast-charging infrastructure will be inadequate for both power delivery and thermal management; therefore, aviation charging systems also require standardized protocols and integrated energy-management controls to ensure safety, interoperability, and reliability. Understanding the technical specifications, power requirements, and cost implications of different charging solutions will also be crucial for airport operators and aircraft manufacturers. Ultimately, addressing the infrastructure challenges, including the electrical charging infrastructure, will become an essential part of a holistic approach to the electrification of all types of aviation.
Regulation & Certification of Electric Aircraft
The FAA and EASA are the two central regulatory authorities responsible for ensuring the safety and regulation of aviation. These authorities are crucial in establishing and enforcing standards for aircraft design, production, pilot licensing, and maintenance and operating requirements. Their main goal is to ensure that the design of all aircraft meets accepted aeronautical standards and that the aircraft is safe to fly.
With the emergence of electric aviation and related technical advancements, such as specialized electric motors, new types of batteries, fly-by-wire flight control systems, and autonomous flight, unique challenges must be addressed within the existing regulatory framework, including the Federal Aviation Regulations (FARs). The innovative technologies and components used in eVTOL and other electrically powered aircraft generally differ from the certification standards for conventional aircraft. Therefore, adapting or creating new regulations becomes necessary.
Issues have arisen with the certification of Leonardo’s AW609 civil tiltrotor, a hybrid aircraft that combines features of both helicopters and airplanes. The program was launched in 1996; however, as of 2025, the aircraft still has not received certification under EASA rules. The only other civil fly-by-wire rotorcraft is the Bell 525 Relentless, which started development in 2012 and still needs certification from the FAA. Such lengthy certification processes for aircraft, not just those using new technologies, seem typical rather than exceptional. Indeed, the FAA has made its position very clear: “In terms of AAM [advanced air mobility], we are viewing [those aircraft] as the same level of safety as any other passenger aircraft or any other piloted aviation.” “We believe the societal expectations for these aircraft are that they will operate like any other Part 21 or 23 aircraft with Part 91 operations.”
The FAA and EASA are well aware of the need to continually evolve their airworthiness and operational regulations to keep pace with emerging technologies. They have engaged with industry leaders, research organizations, and manufacturers to understand the implications of electric aviation and autonomous flight. However, updating aviation regulations remains a complex and lengthy process, and certifying an eVTOL aircraft is likely to take many years. Nevertheless, the authorities understand that to advance the aviation field, they must continue to strike a balance between ensuring safety and fostering innovation, including the formal certification and the eventual issuance of a certificate of airworthiness for all types of electrically powered aircraft.
Looking to the Future
But what about looking to the future? Can electrically powered aircraft be realized and used in commercial aviation? Technically, it is just engineering. But at what cost? Can these aircraft also satisfy the airworthiness regulations set down by the FAA or EASA? The current battery technology, with a pack-level battery-specific energy of around 0.2 to 0.25 kWh/kg, has several limitations, particularly for use in an aircraft designed to carry passengers over reasonable distances. However, if battery-specific energy can be doubled to 0.5 kWh/kg, it would substantially improve the performance and capabilities of electrically powered aircraft.
The corresponding increase in range and payload capacity makes electric aviation more competitive and practical for a broader range of applications, including regional or short-haul flights. For instance, taking the aircraft in Example #2, doubling to 0.5 kWh/kg would give it a flight time of 40 minutes, during which it would cover a distance of approximately 100 nautical miles, which is significantly more helpful.
In the meantime, the industry and research organizations forge ahead, exploring new technologies and electrically-powered aircraft concepts, including NASA’s X-57, as shown in the artist’s rendering below. According to NASA: “The primary goal of the X-57 project is to share the aircraft’s electric-propulsion-focused design, airworthiness process, and technology with industry, standards bodies, and regulators to inform certification approaches for all-electric propulsion in emerging electric aircraft markets.” The X-59 project was canceled in June 2023 because the new technology was deemed too risky to be fielded on a flying aircraft. It seems ironic that an X-plane suffers cancellation because of a higher-than-average risk. Is that not why X-planes are designed in the first place? This decision is a setback for NASA in the advancement of electric aircraft, but the private industry will soon pick up the technical slack as Elon Musk did with SpaceX and Tesla.
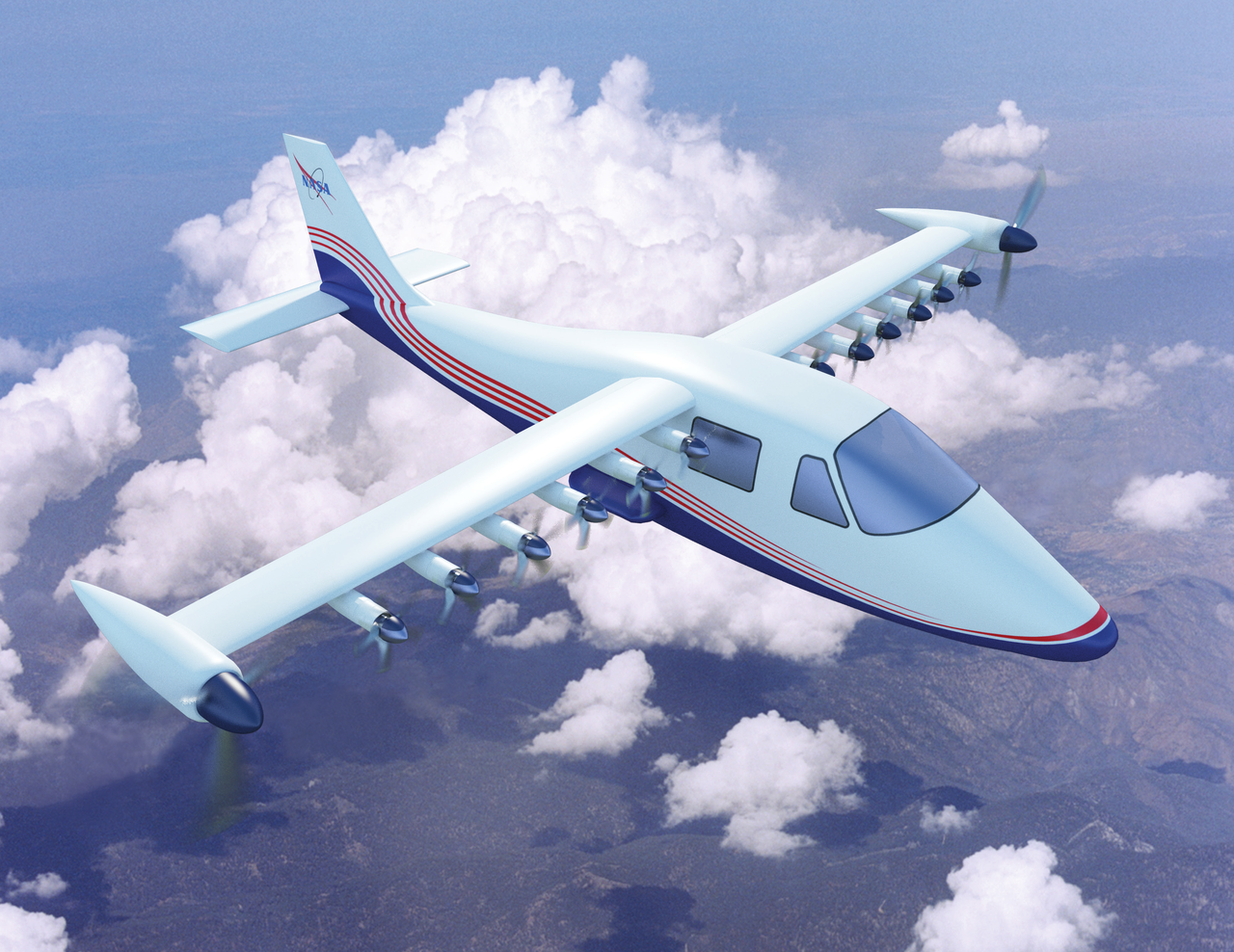
Advancements in battery technology continue to be pursued, with ongoing research into various battery chemistries that could significantly improve energy density while reducing weight, maintaining safety, and ensuring durability. In the meantime, hydrogen-powered fuel cells are another way to leverage the efficiency improvements of electric propulsion systems. They sidestep the problem of the low specific energy of batteries, but now the challenges of hydrogen production, storage, and delivery must be confronted. Hydrogen is very energy-dense and light, but is highly reactive. Hence, a concern in its use is that leaks of high-pressure hydrogen are highly susceptible to spontaneous combustion, which may cause a fire or explosion. Nevertheless, investigating the potential performance characteristics and GHG mitigation of fuel cell-powered aircraft is an opportunity for the future.
Electrically powered road vehicles have reached a tipping point, as current battery capacity has enabled them to achieve ranges of 400 miles (644 km). In the meantime, is there a tipping point to look out for when it comes to batteries surpassing Avgas or jet fuel? At this point, the goal must be at least 800 Wh/kg, but even then, the need for a mandated reserve of energy will make this the absolute minimum to be practical. Higher-life-cycle batteries currently remain at 250 Wh/kg, even less after installation, but they are likely to exceed 400 Wh/kg by 2030. High-life-cycle batteries in the 1 MWh/kg class are probably another decade away, which is closer to the tipping point needed for aviation applications.
Small-Scale Electric Propulsion for UAVs
Electric propulsion systems are increasingly common in both commercial and military aerospace applications. A focused study of small-scale electric propulsion, particularly for uncrewed aerial vehicles (UAVs), provides students and young engineers with timely exposure to technologies central to modern aerospace systems. Participation in design competitions, such as the AIAA Design/Build/Fly (DBF) challenge, has further increased student interest in small-scale electric propulsion. These competitions require teams to design, fabricate, and demonstrate electric-powered fixed-wing UAVs. The DBF competition emphasizes critical design tradeoffs involving endurance, payload, and power-to-weight ratios, making it an ideal applied design problem.
At this scale, the primary components include the battery, brushless DC motor (BLDC), and electronic speed controller (ESC). Lithium polymer (LiPo) or lithium-ion batteries are typically used because of their high energy density and rapid discharge capabilities. The battery’s voltage and capacity determine the available thrust and flight endurance. The BLDC motor, favored for its high efficiency and precise electronic commutation, delivers mechanical shaft power to the propeller.
Communication is handled by the ESC, which interprets throttle commands, typically in the form of pulse-width modulated (PWM) signals, and regulates the voltage and current supplied to the motor. The ESC translates PWM input signals, usually ranging from 1.0 ms (idle) to 2.0 ms (full throttle) at a frequency of 50 Hz, into three-phase power output. Internally, ESCs use high-frequency switching of power transistors to manage output voltage and timing. Most ESCs include startup sequencing and thermal protection and may offer telemetry such as voltage, current, temperature, or rotational speed (rpm).
The electrical power delivered from the battery is given by
(38)
where is the voltage and
is the current draw. The mechanical power output at the motor shaft, assuming motor efficiency
, is
(39)
where is the torque and
is the angular velocity. The battery’s total energy capacity, expressed in Watt-hours, is
(40)
where is the battery capacity in ampere-hours (Ah). The corresponding flight endurance can be estimated by
(41)
where is the overall efficiency of the propulsion system, and
is the average electrical power consumption in flight.
Worked Example #5 – Endurance of a small UAV
A fixed-wing UAV is powered by a 14.8V battery with a 6,600 mAh capacity. During the cruise, it draws 9 Amps. Assuming 90% usable battery capacity and 80% motor efficiency, estimate its endurance and shaft power.
Show solution/hide solution.
First, convert battery capacity to ampere-hours, i.e., = 6.6 A-hr. The usable energy is
(42)
The power draw is , giving
(43)
The shaft power available is
(44)
which needs to be matched to the drag and power requirements of the MAV.
Summary & Closure
Electrically powered aircraft offer numerous potential benefits for modern aviation, including increased energy efficiency and reduced carbon emissions compared to conventional fossil fuel-powered aircraft. However, it is likely that passengers will only fly on electric aircraft for short distances, even in the longer term. Battery technology is one of many factors limiting the feasibility of electric aviation. Other aspects of electric aircraft need to be considered, such as infrastructure development, charging systems, regulations and certification, overall economics, and public acceptance.
A combination of technical approaches will likely be employed in the next few decades to overcome the challenges associated with “pure” electrically powered aircraft. This more diversified approach will continue to improve fuel efficiency, potentially through new aircraft designs that incorporate sustainable aviation fuels (SAFs) and explore hybrid-electric or hydrogen-electric propulsion systems. When collectively applied, these interim technologies could help reduce emissions from the aviation sector. Meanwhile, engineers must continue to innovate and develop new or improved solutions that meet the unique requirements of electrically powered airplanes, while also addressing broader global concerns about reducing the environmental impact of fossil fuels.
Small-scale electric propulsion offers a compact, efficient, and instructive platform for aerospace study. A solid understanding of electrical and mechanical power conversion, control signaling, and energy budgeting enables students to confidently analyze, integrate, and optimize UAV propulsion systems. As UAV applications continue to expand in both civil and military domains, this knowledge provides a practical foundation for further coursework, design activities, and professional development.
5-Question Self-Assessment Quickquiz
For Further Thought or Discussion
- Why does the goal of decarbonizing terrestrial transport and electrifying aviation also pose an educational challenge?
- Electric car manufacturers have been experiencing problems with vehicles catching fire. How can the flying public be confident in electrically powered aircraft, knowing that an in-flight fire will likely be catastrophic?
- List critical factors that influence the performance of electrically-powered airplanes compared to traditional internal combustion engine aircraft.
- Given that air transport of lithium-ion batteries as cargo is banned or strictly controlled, how can their use as the primary propulsive energy source be considered for propelling an airplane?
- Turboprops and turbofan engines are well-proven, refined, efficient, and reliable. Why would the aviation industry ever want to stop using them?
- Are hybrid-electric systems more environmentally friendly than traditional ones? Discuss.
- Battery technology has yet to achieve sufficient maturity to make commercial electric air transport viable. Discuss this statement.
- Advances in battery and electric motor technology, combined with more efficient aerodynamic designs, will characterize the future of electric aviation. Discuss.
- Electrically powered commuter-class airliners could take to the sky in the next few years, maybe even before the decade’s end. But they probably won’t be able to take very many of us very far. Why?
- Besides the low energy density of batteries, the infrastructure and regulatory hurdles are likely more severe challenges than the technical ones. Discuss this viewpoint.
- Regulators often need to develop standards, safety rules, and certification guidelines to keep pace with technological advancements and the introduction of new products. Why?
- Will eVTOL air taxis operate similarly to regular taxis, such as picking you up at home and dropping you off at the airport?
Other Useful Online Resources
Take a deeper dive into the field of electrically powered aircraft by following up with some of these online resources:
- Chat with ChatGPT about its thoughts on electric aviation.
- A great webpage by Airbus about hybrid and electric flight.
- This is a good video on the topic of hydrogen-powered versus electric-powered aircraft.
- Take a flight on the world’s first certified electric airplane.
- Find out about the world’s fastest 345 mph electric airplane!
- Flying 150 miles with Joby’s Electric Vertical Take-Off and Landing Aircraft (eVTOL).
- Anderson Cooper reports on eVTOLs, or electric vertical takeoff and landing vehicles, which may one day provide a solution to bumper-to-bumper traffic.
- A video reviewing the progress of eVTOL and electric aviation.
- A video on how eVTOL could disrupt the $49B helicopter industry.
- The insane engineering of the Joby S4 eVTOL aircraft.
- The False Promise of Green Energy – lecture by Prof. Andrew Morriss.
- Aviation emissions account for about 2.5% of total global emissions but drive about 7.2% of global warming. See Lee D. et al., "The Contribution of Global Aviation to Anthropogenic Climate Forcing for 2000 to 2018," Atmospheric Environment 244, 117834, 2020. https://doi.org/10.1016/j.atmosenv.2020.117834. ↵
- An ICE is only about 25% efficient on average versus 80%+ for the electric motor. ↵
- Sufficient reserve fuel must be carried to comply with FAA or equivalent regulatory requirements. ↵
- Note: 1 kW ≈ 1.34 hp. ↵