9 Aerospace Structures
Introduction[1]
Now that some understanding of the anatomy of flight vehicles has been gained, it is logical to delve deeper into their structural design characteristics. While aerodynamics is the underpinning of atmospheric flight, an aircraft must also have a suitably shaped structure capable of carrying all the aerodynamic and other loads produced on it, such as engine loads, undercarriage loads, landing vertical and side loads, etc. Indeed, any aerospace structure must be immensely strong and lightweight, but also robust and durable. Therefore, the structural design options and constraints must be well understood.
Many structural design goals and engineering challenges for spacecraft are similar to those for aircraft, including the need for optimum-shaped structures made of high-strength, lightweight materials. However, unique high-temperature-capable materials may be required for specific spacecraft because of kinetic heating effects, such as during re-entry into the Earth’s atmosphere. Supersonic aircraft may also need to incorporate specific design features to expand structurally during flight without generating high internal stresses.
Learning Objectives
- Appreciate the history and evolution of aerospace flight structures.
- Understand the primary loads on an airframe, such as tension, compression, bending, torsion, and shear.
- Know how aircraft structures are constructed, including spars, ribs, stringers, skin, etc.
- Understand the principles behind the finite element method (FEM) and why it is used in designing structurally efficient aerospace structures.
- Be aware of some of the challenges in airframe design, including avoiding buckling and fatigue, as well as incorporating structural redundancy to enhance safety and reliability.
Brief History of Aerospace Structures
George Cayley, often referred to as the “Father of Aeronautics,” recognized the importance of constructing airplanes from lightweight materials. Cayley had the idea of using stacked wings in the form of biplanes and triplanes to give them a collective structural stiffness and strength. Otto Lilienthal capitalized on Cayley’s ideas of flight and lightweight structures, building several types of gliders that resembled the wings of birds and bats. Octave Chanute built gliders similar to Lilienthal’s but incorporated external bracing wires to give the wing more structural strength and stiffness. In early 1903, Samuel Langley attempted to launch his tandem monoplane from a catapult, but it crashed after its frail wooden structure failed catastrophically.
By the end of 1907, the Wright brothers had successfully flown several other versions of their original Flyer, a biplane type more strongly built from a wooden skeleton covered with fabric. Their wing design used spanwise spars and chordwise ribs braced with struts and wires. The main advantage of the biplane is that its upper and lower wings are connected by vertical struts and bracing wires, forming a strong, box-like structure, as shown in the photograph below. This type of design is much more resistant to bending and twisting than a single wooden wing. The skeleton is then covered in cotton fabric, which is tightened and sealed by brushing on cellulose dope. However, a biplane wing design also has high aerodynamic drag, which is a significant overall disadvantage. Nevertheless, this type of wing and airframe construction continued into the 1930s, and many successful biplane aircraft were built.
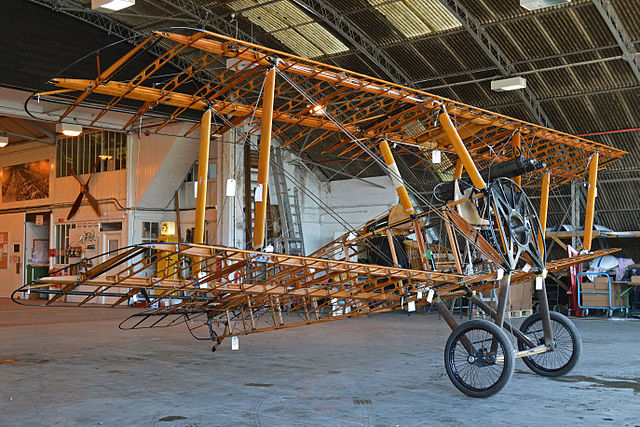
In 1909, Louis Bleriot of France built and flew a monoplane aircraft made of wood and fabric, although it was extremely fragile. One significant advantage of a monoplane is its reduced aerodynamic drag compared to the braced wings of biplanes or triplanes. Bleriot followed Octave Chanute‘s approach, where steel wires supported the single wings from a tall mast extending above the fuselage. However, the cables still created significant aerodynamic drag on the airplane, reducing its performance. Bleriot also used a welded truss-type fuselage that was lightweight and strong, and this method became a standard type of early airframe construction.
By the 1920s, aluminum alloys suitable for airplane construction had become increasingly available, so airplanes made of wood and fabric were being increasingly relegated to history. In addition, the years leading up to WWII saw many advances in aircraft construction techniques, and riveted aluminum “stressed skin” construction techniques became the standard for almost all new aircraft. In 1925, Ford Motor Co. entered the aviation business with the 4-AT Trimotor, a three-engine, all-metal airplane using corrugated aluminum skins. Dubbed “The Tin Goose,” it quickly became successful and was used by over 100 airlines worldwide.
By the mid-1930s, airplanes were becoming larger and heavier and were almost entirely made of stressed-skin aluminum construction in which the components were all riveted together. Other construction methods were developed to achieve the required structural strength and stiffness of the wings, including multi-spar and box-beam designs, one of which is illustrated in the figure below. Box beam designs use multiple spar caps, webs, and shear panels to achieve high bending and torsional stiffness, efficient material use, and overall structural redundancy.
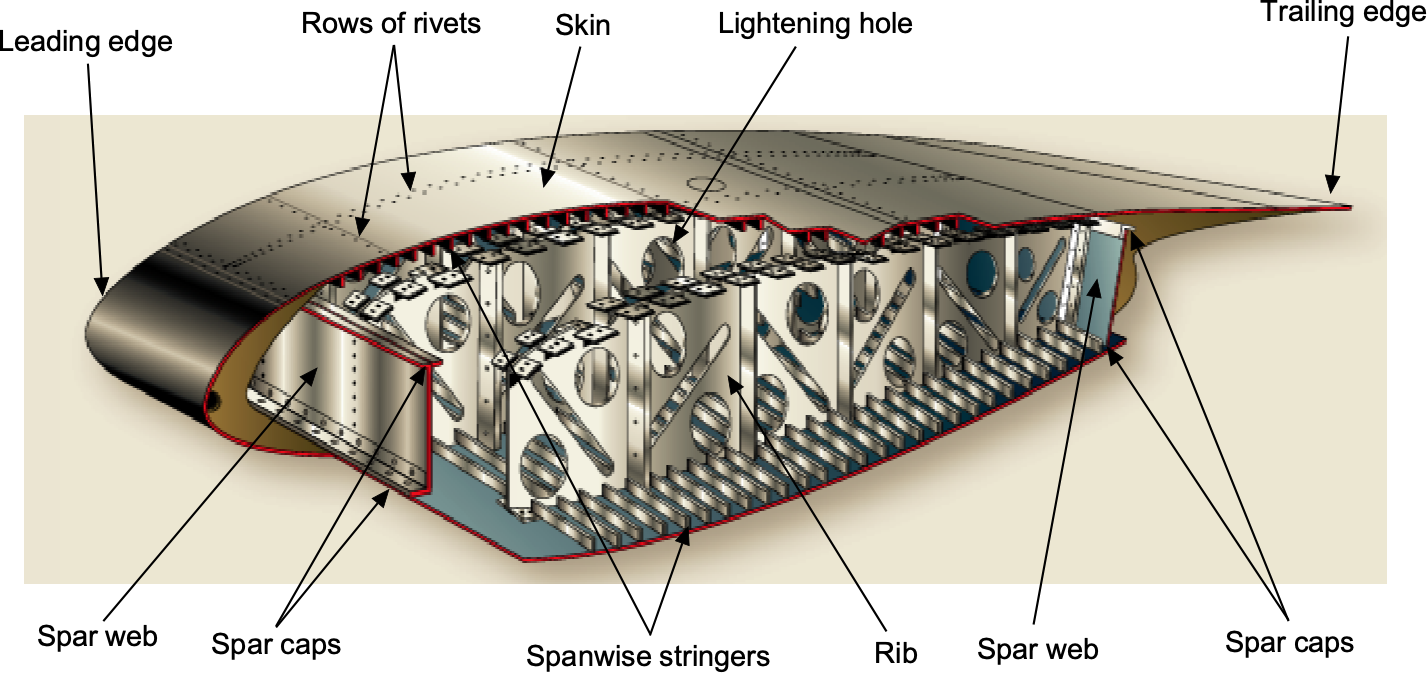
Over the last 50 years, there has been a steady increase in honeycomb and foam core sandwich components made from composite materials such as glass and carbon fiber. Bonded aluminum honeycomb sandwich panels, developed in the 1960s, offer exceptional stiffness and strength for their weight. These sandwich structures were increasingly used for wing skins, flight control surfaces, cabin floors, launch vehicles, satellites, helicopter rotor blades, and many other applications. Sandwich construction is widely used in the manufacturing of helicopter rotor blades, as illustrated in the figure below. The rotor blades must be extremely strong but also lightweight. The dominant loads on the blade are caused by centrifugal effects resulting from its rotation, which produce a tensile load directed along the length of the blade. The blades are also subjected to cyclic lift forces that cause bending and torsional twisting. Early rotor blades were made of aluminum or steel, perhaps using metal honeycomb as a core material.
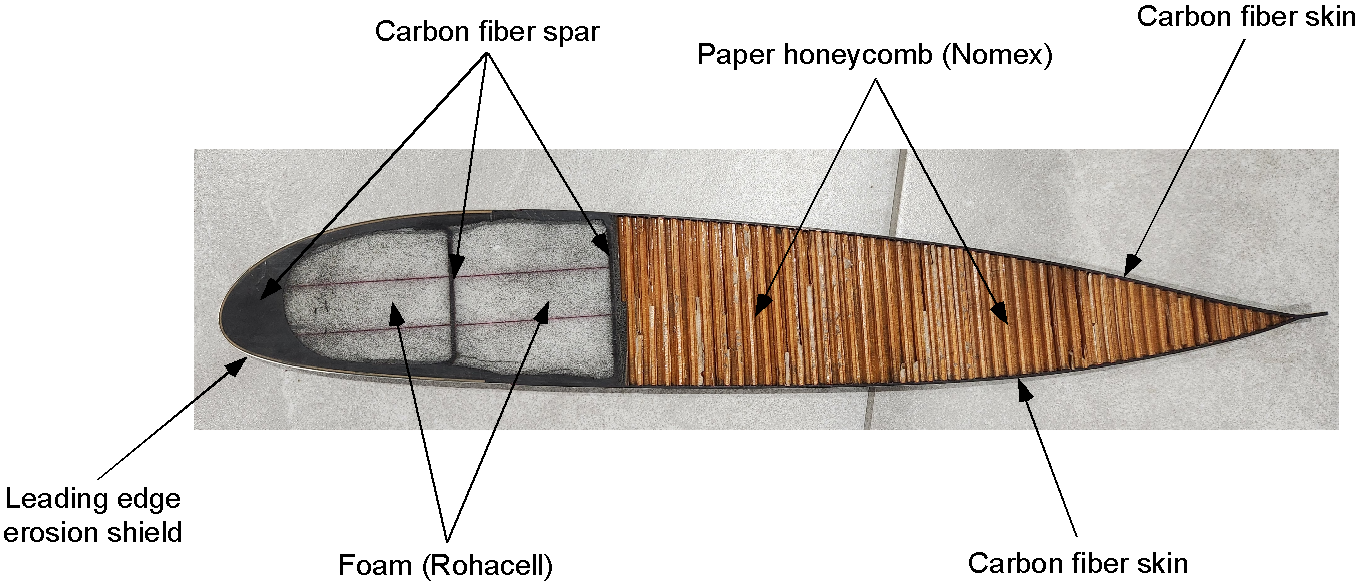
Over the last few decades, advanced materials and manufacturing techniques have enabled a transition from primarily building airframe structures made entirely of aluminum to those composed of a majority of composites, such as carbon fiber-reinforced polymer (CFRP). CFRP offers several advantages over traditional aluminum. Its higher strength-to-weight ratio means that structures made from CFRP can achieve the same or greater strength while using less material. This reduction in material volume lightens the overall structure, leading to improved fuel efficiency per unit of payload carried. For example, the fuselage barrel shown in the photograph below is approximately 30% lighter than it would be if made from aluminum stressed skin construction.
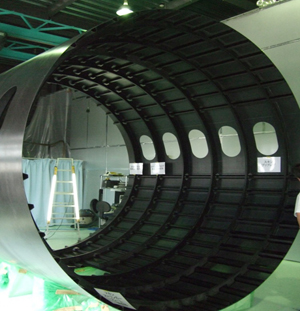
Modern aerospace structures can be tailored using advanced computational techniques, such as the finite element method (FEM). FEM enables engineers to simulate and analyze the structural performance of complex shapes and materials under various conditions. This tailoring ensures that every component is optimized for maximum structural efficiency, striking a balance between strength, stiffness, and weight. Additionally, CFRP’s resistance to fatigue and corrosion, combined with its superior mechanical properties, yields a longer service life and lower maintenance costs compared to traditional materials. As a result, the shift toward composites, such as carbon fiber-reinforced polymer (CFRP), in aerospace engineering represents a significant leap forward in creating lighter, stronger, and more efficient airframes that meet the stringent demands of modern aviation.
The history of spacecraft structures spans from the simple stainless steel shells of early satellites to the complex modular designs of the International Space Station (ISS). Key milestones include the Apollo Lunar Module’s lightweight aluminum and titanium construction, as well as the Space Shuttle’s intricate aluminum airframe, covered with reinforced carbon-carbon tiles. Modern 3D-printed and inflatable structures allow for cost-effective and adaptable designs. At the same time, projects like SpaceX’s Starship push boundaries by utilizing lightweight stainless-steel structures, embodying the continuous evolution of spacecraft structures in response to technological advancements and evolving exploration goals.
Types of Structural Loads & Stresses
The aerodynamic and other loads or forces imposed on a flight vehicle cause internal stresses in the material(s) from which the flight vehicle is made. Stress can be viewed as the internal action that opposes the deformation of the material under load. The corresponding deformation of the material under load is called strain. Therefore, when any material is subjected to an external loading, it will become stressed and deformed, i.e., it will always exhibit some strain, regardless of how stiff or strong the material is.
As shown in the figure below, five types of stresses and strains can be produced in the parts comprising aerospace structures, namely compression (pushing or squeezing), tension (pulling), shear, torsion (twisting), and bending. These stresses and strains can be produced individually in a structural component or in combination with other loads.
The five basic types of stresses and strains that can be produced in aircraft structures are compression, tension, shear, torsion, and bending.
- Compression is the stress that causes a strain that squeezes and shortens the part. A component’s compressive stiffness is its resistance to compression forces.
- Tension is the stress that resists the force pulling and causes a strain that tries to extend the part. A component’s tensile stiffness is its resistance to tensile forces.
- Shear is the stress that resists the forces acting in opposition, tending to cause one material layer to move relative to the adjacent layer. For example, most fasteners used in aerospace structures are subjected to a shearing action.
- Torsion is the stress produced by a torque that causes a strain that manifests as a twisting effect. A torque is a moment, so it is the product of a force times a distance or “arm.” Therefore, a component’s torsional stiffness can be viewed as resistance to this twisting action.
- Bending stresses result from a combination of compression and tension in the material. A beam-like spar or other component subjected to a bending moment will cause a compressive strain on one side and a stretching strain on the other. In most cases, the individual structural members of aerospace structures are designed to carry mostly tension or compression rather than pure bending.
Structural Stress & Strain Relationships
Stress, given the symbol , is used as a measure of the forces that cause a structure to deform and can be defined as the force per unit area acting on the cross-sectional area of the structure, i.e.,
(1)
where is the force, and
is the area of the cross-section over which the force acts. Stress has units of force per unit area, which is analogous to structural internal pressure. A force pulling on a structural member causes it to elongate, creating tensile stress. A force squeezing a member is called compressive stress. A structure subjected to forces from all sides is referred to as bulk stress.
Strain, given the symbol (or sometimes
), is a measure of the deformation of an object under such stress and is defined as the fractional change of the object’s length relative to its original length, i.e.,
(2)
where is the original length and
is the change in length. Notice that strain is a dimensionless quantity.
The stress produced in a structural member also depends on the stiffness of the material used for that member. Many materials exhibit a linear elastic relationship between stress and strain, as shown in the figure below, at least up to a point referred to as the proportional limit.
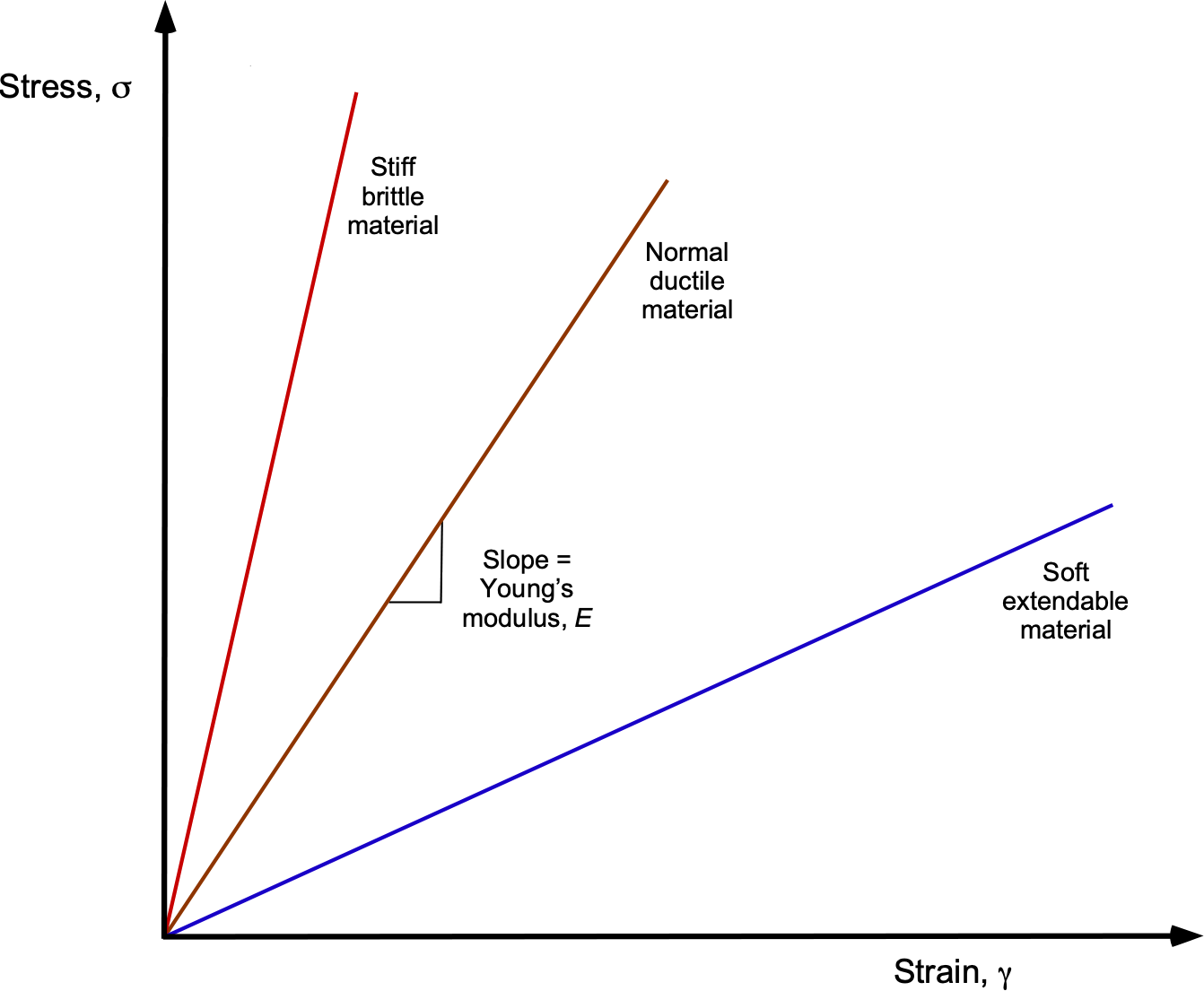
The elastic nature of materials means that after the load is removed and the stress is released, the material returns to its original undeformed state. This linear stress-strain relationship is known as Hooke’s Law, and the gradient or slope of the stress-strain curve is called the modulus of elasticity, given the symbol , which is usually called Young’s modulus, i.e.,
(3)
Stiff materials have a higher Young’s modulus value but tend to be brittle, fracturing easily. Soft and easily extendable materials have a lower Young’s modulus value.
Check Your Understanding #1 – Determining stress & strain in a structural member
A structural member in an airframe has a cross-sectional area of 3.2 cm2 and is 1.3 m in length. A tensile force of 0.51 kN is applied to the member, causing it to elongate by 0.21 mm. Assuming the material is perfectly elastic, determine the stress and strain in the member.
Show solution/hide solution.
The stress is given by
where is the force, and
is the area of the cross-section. Inserting the known values for this problem gives
Note that stress is measured in units of Pascals (Pa) in SI units, i.e., 1 N m = 1 Pa. The corresponding strain is defined as
Inserting the known values gives
Notice that strain is dimensionless (i.e., it has no units).
Trusses & Shear Webs
The development of aircraft structural concepts paralleled advances in aerodynamics, materials, and flight performance. In the earliest aircraft, such as the Wright Flyer and many WWI biplanes, a significant portion of the airframe consisted of trusses made from rods and cables, as illustrated in the figure below. These frameworks consisted of a series of triangular elements, typically constructed from wood or steel tubes, with tensioned wires providing bracing and contributing to the structural stiffness. By appropriately combining rods and wires, designers achieved a lightweight and mechanically efficient structure. A fabric skin covered the truss to create an aerodynamically smooth surface, although the fabric itself was not load-bearing. While these truss structures were relatively easy to fabricate, the use of diagonal wires limited their function to carrying tensile loads. Hence, any member in compression had to be a rigid rod.

While truss frameworks are relatively simple, they lack redundancy. As a result, the failure of a single rod or wire can lead to the catastrophic collapse of the entire structure. To address this vulnerability, engineers began to incorporate the fail-safe design concept. Unlike safe-life structures, in which each component must survive the entire design life without failure, fail-safe systems are designed to tolerate the failure of individual elements by redistributing loads through alternate structural paths. A truss composed entirely of rigid rods, rather than a combination of rods and tension-only cables, offers greater strength and inherent redundancy. This design philosophy became increasingly crucial as aircraft structures evolved toward more integrated and continuous load-bearing configurations.
Subsequently, engineers moved away from discrete structural members and began constructing frameworks using continuous elements, including thin plates known as shear webs, as illustrated in the figure below. The upper and lower members acted as flanges, carrying axial tension and compression induced by bending moments and other loads. The shear webs connected these flanges along their lengths, completing the load paths and enabling the structure to resist both bending and shear. Early designs still featured internal frames and spars covered with non-load-bearing fabric skin. However, as aircraft grew larger and faster and encountered greater aerodynamic loads, designers increasingly replaced diagonal truss members with continuous shear-carrying plates and adopted stressed-skin construction using aluminum sheet, which contributed structurally to the airframe.
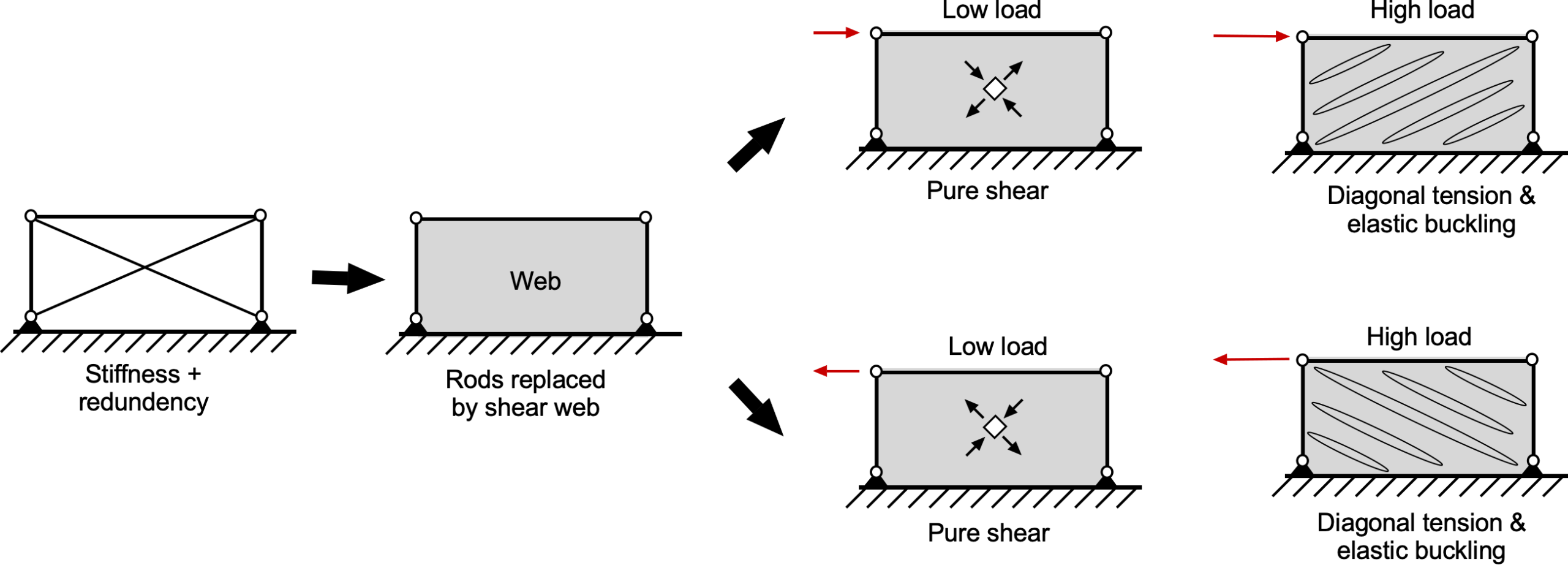
This transition introduced a new design challenge, namely the wrinkling or buckling of thin webs. Sheets subjected to compressive stress are prone to elastic instability, commonly referred to as buckling. Although buckling does not always lead to structural failure, it reduces effective stiffness and diminishes the ultimate load-carrying capacity of the structure, often requiring reinforcement or redesign. While one solution is to increase the thickness of the web, a more weight-efficient approach is to incorporate supporting members, called stiffeners or stringers, that are attached to the thin web to prevent local buckling.
As aircraft performance demands increased, particularly in terms of speed, maneuverability, and payload capacity, designers adopted fully stressed-skin and semi-monocoque structures. In these configurations, the external skin was no longer a passive aerodynamic fairing but became an active, load-bearing element of the airframe. The skin carried a substantial portion of the shear and bending loads, particularly under torsion, resulting in strong, lightweight, and inherently redundant structures.
Wing Structures
The wings generate lift to overcome the aircraft’s weight and are typically the largest and heaviest structural components of the airframe. As such, they must be designed to be both extremely strong and as lightweight as possible. Wing geometry varies widely, and any particular design reflects a balance among structural strength, weight, and aerodynamic efficiency. In some aircraft, especially smaller or slower ones, wings may be externally braced using struts or wires that help support aerodynamic loads. While this approach allows for a lighter internal wing structure, it increases drag from the exposed bracing elements.
In the 1930s, the transition toward widespread use of monoplanes, which offered inherently lower aerodynamic drag than biplanes, created a growing demand for stronger, lighter wing structures. The increased flight speeds and wing loadings necessitated more advanced structural solutions beyond the trussed spars and externally braced wings commonly found in earlier designs. To address these demands, engineers introduced thin shear webs between the upper and lower flanges of the main spar, allowing the spar to function as an I-beam. This design efficiently distributed bending loads through the flanges, while the shear web carried transverse shear forces. In some aircraft, particularly those requiring higher torsional stiffness or longer spans, the I-beam configuration was replaced by or supplemented with a closed-section box beam, further improving shear and torsion resistance. These innovations marked a fundamental shift toward semi-monocoque construction, paving the way for stressed-skin designs that enabled cleaner aerodynamic profiles, reduced structural weight, and higher overall performance.
Today, wings are designed as complete cantilever beams to reduce drag, i.e., without any external bracing. Most wings have various internal structural members covered by a thin aluminum sheet skin, i.e., they are of a typical semi-monocoque stressed skin design, as shown in the figure below. The internal structures of wings are made up of a lattice of spars and stringers that run spanwise and ribs or other types of formers that are placed chordwise. The main spar is the primary structural member of a wing, carrying most of the applied bending and shear loads. The skin carries most torsional loads and transfers the stresses to the wing ribs.
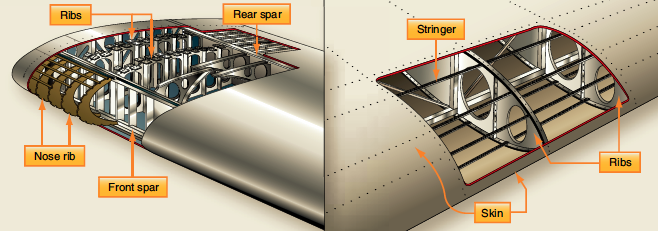
The ribs give the wing its aerodynamic (airfoil) shape and transmit the skin loads and stringers to the spars. The lightweight ribs are stamped out of a flat aluminum sheet, and then flanged holes are cut into the ribs to reduce the overall weight of the assembly. Flanging the holes increases the resistance to buckling. The rib has a cap around its periphery, often in the form of a “T” or “L” shape, which stiffens and strengthens the rib and is then attached to the wing skin using rivets. Ribs can extend from the wing’s leading edge to the rear spar or the wing’s trailing edge. Similar ribs are also used to construct the ailerons, elevators, rudders, and other components.
Depending on a specific aircraft’s design criteria, spars may be made of metal, wood, or composite materials. Bolts typically attach the spars to the fuselage, using various fittings to distribute the loads. Wing main spars are variations of I-beam structures made of solid extruded aluminum or several aluminum extrusions riveted together, as shown in the figure below. The I-beam’s top and bottom parts are called the spar caps, which take the compression and tensile loads produced from bending. The vertical section, commonly referred to as the web, carries the vertical shear loads. The web forms the spar’s principal depth portion, to which the caps are attached.
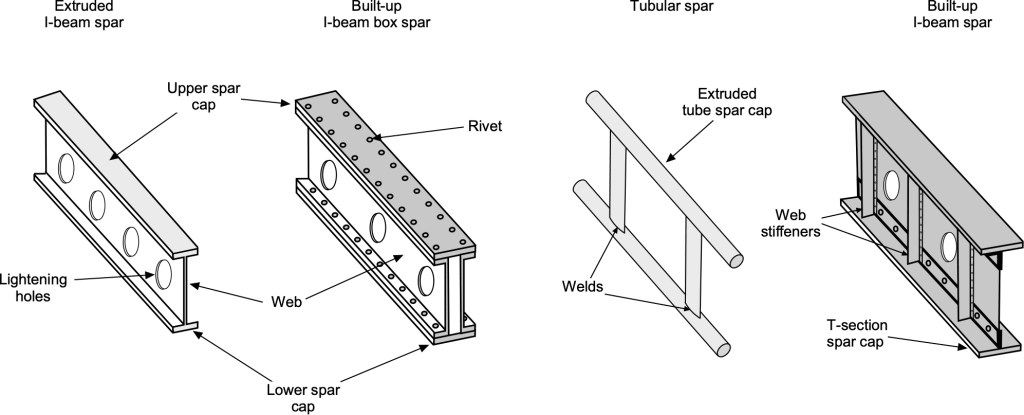
The stress, , in a wing spar can be calculated using the bending stress equation as given by
(4)
where is the bending moment,
is the second moment of area of the cross-section, and
is the distance from the neutral axis to the point where the stress is being calculated, as shown in the figure below. The highest stresses will arise in the spar caps, the lower cap being in tension and the upper cap in compression. The second moment of area
for the cross-section of the spar (or the wing as a whole) depends on the geometry of the cross-section. Values for common shapes are available, including rectangles, L-shapes, T-sections, U-sections, and I-beams. For a symmetric cross-section, the neutral axis will be halfway between the top and bottom of the section.
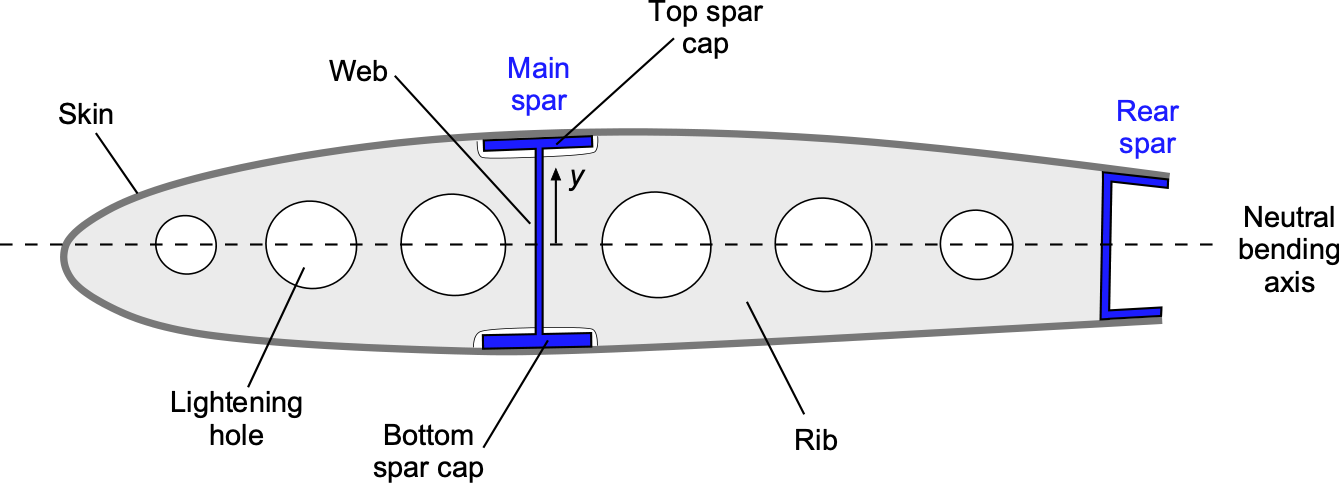
Today, composite materials are also used to manufacture wing spars because of their excellent strength-to-weight ratio and resistance to fatigue cracking. Fatigue is the weakening of a material caused by repeated cyclic loading, which can result in a catastrophic failure of a wing spar or other structural component if a fatigue crack grows too much. Sharp corners are a potential source of fatigue cracks; therefore, rounded holes and smooth transitions enhance fatigue resistance. Smaller airplanes may have just one or two spars. Rear “false” or part-span spars are also commonly used in wing construction, serving as hinge attach points for control surfaces such as flaps and ailerons.
Larger aircraft have multiple spars that can be built into a box beam, as shown in the figure below, which is a standard structural design for commercial airliners. It uses two or three main longitudinal spars to connect ribs and bulkheads, forming a box shape with tremendous bending and torsional strength. The interior of the wings may also be used for fuel tanks. The wing joints are sealed with a special fuel-resistant sealant, enabling fuel to be stored directly inside the structure, a design known as a wet wing. Alternatively, a separate fuel bladder or tank can be fitted inside the wing, a more typical implementation on smaller aircraft.
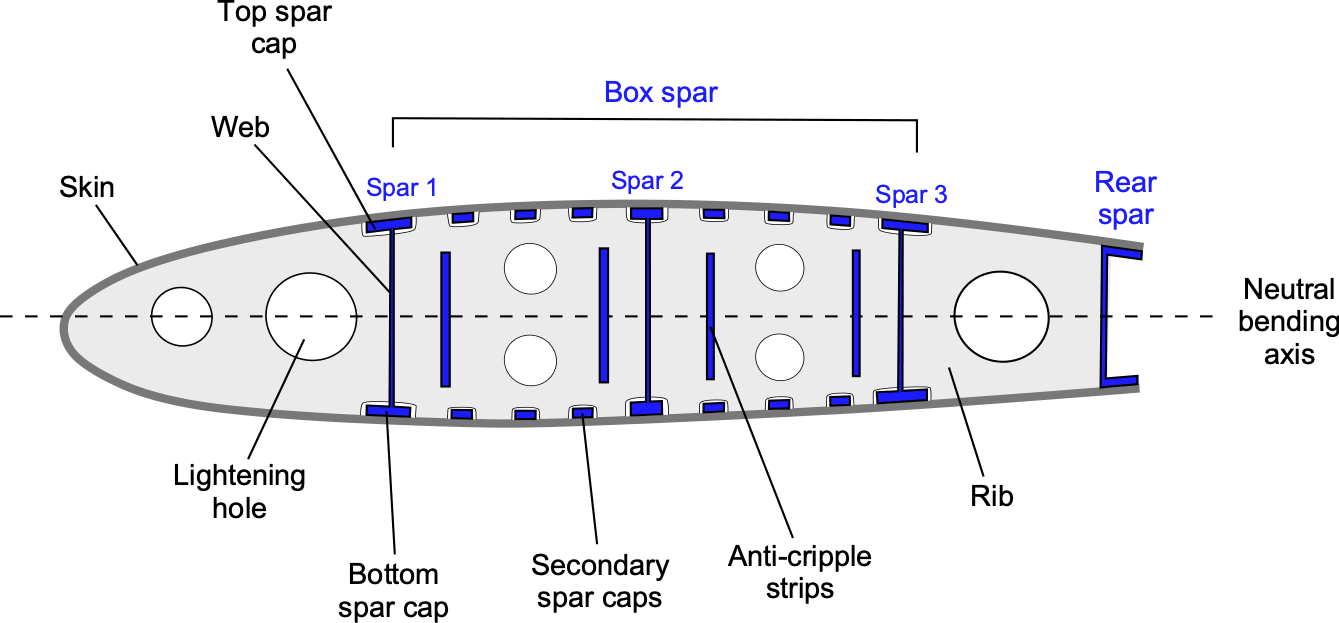
Secondary spars and stringers may be used to enhance strength, prevent buckling, and provide structural redundancy, making the wing fail-safe. In this context, “fail-safe” means that if one critical wing component fails, there is enough remaining structural redundancy and alternative load paths to prevent a catastrophic failure. The FAA’s accepted definition of fail-safe is “The attribute of the structure that permits it to retain its required residual strength for a period of unrepaired use after the failure or partial failure of a principal structural element.”
Check Your Understanding #2 – Bending moments and stress in a spar
An engineer needs to calculate the maximum stress in the lower cap of a cantilevered wing spar. The material is an aluminum alloy with a maximum allowable stress of 276 MPa. The spar is 3 m long and has a height of 0.1 m. The spar must carry an in-flight load of 20 kN with a factor of safety of 5, which can be considered to act at the mid-length of the spar. The second moment of area of the spar is m
. The spar can be considered as encastré at the root, i.e., rigidly fixed.
Show solution/hide solution.
The bending moment, , on a cantilevered beam of length
with a point load,
, acting at its mid-span is
where is the factor of safety. The maximum bending stress in the beam will be in the spar caps at a distance
from the neutral axis, so that the root of the spar in the lower cap, the tensile stress will be
Substituting the numerical values gives
This stress value is well below the strength of the aluminum alloy (276 MPa), so the spar will easily carry the required load, including a significant margin.
Fuselage Structures
The fuselage is the primary structure, or “body,” of the aircraft. It provides space for the aircrew, passengers, cargo, and other equipment. There are two basic types of fuselage construction: the truss type and the monocoque/semi-monocoque type. In single-engine aircraft, the fuselage also usually houses the engine. In multi-engine aircraft, the engines may be located in the fuselage or attached to it, although they can also be suspended from the wings or contained within them.
A truss-type fuselage is a lightweight framework of steel alloy tubes that provides stiffness and resists deformation from applied loads. As shown in the figure below, this type of structure is sometimes referred to as a space-frame design. Diagonal web members give the truss most of its bending and torsional stiffness. The truss-type fuselage frame is typically constructed from light steel alloy tubing that is welded together, allowing all truss members to carry primarily tension and compression loads.
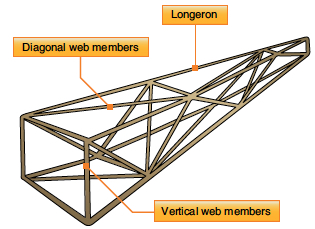
In some aircraft, truss fuselage frames may consist of aluminum alloy rods riveted or bolted at their ends using gusset plates. The truss-type fuselage is typically covered with fabric, although thin plywood or aluminum sheets may be added to provide additional stiffness and improve durability. Although it is often used on smaller general aviation aircraft, the design does not scale well for larger aircraft because it becomes too heavy compared to other designs.
The most common type of fuselage construction for aircraft is the monocoque or semi-monocoque design. As shown in the figure below, the monocoque (i.e., single-shell) fuselage relies primarily on the skin’s strength to carry the loads. In this case, the skin must be thick enough to prevent large compressive deformations or buckling, which increases the structure’s weight. Because the skin is designed to carry significant loads, it is known as a stressed skin design. Skin buckling is likely to occur under bending, compression, or torsion loads in a monocoque structure.
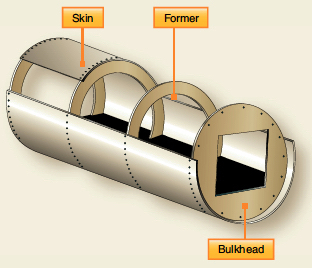
Most modern aircraft utilize semi-monocoque construction, as illustrated in the figure below, which combines a lightweight skin with internal reinforcements, such as frames, longerons, and stringers, to create a strong and rigid structure. The skin, made thinner and lighter, is supported by these components, which help distribute loads and prevent buckling. Longerons, typically aluminum alloy extrusions in “U” or “T” sections, run across multiple frames, providing significant stiffness and supporting primary bending, torsion, and compressive loads. These elements are joined using rivets and other fasteners, ensuring durability while optimizing the strength-to-weight ratio. This design makes it ideal for modern aircraft, offering superior resistance to aerodynamic and structural stresses.
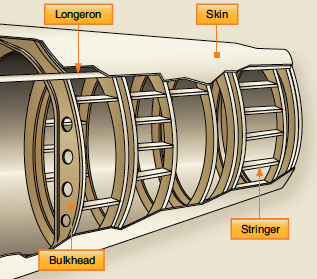
In a semi-monocoque structure, shorter but more numerous stringers are also used to enhance rigidity by supporting the skin and preventing buckling. Attached beneath the skin, they help maintain its shape and may be riveted directly without always connecting to frames or ribs. Both stringers and longerons primarily work in tension and compression, distributing loads efficiently across the fuselage to ensure structural integrity.
How to drive a rivet!
A solid rivet is the most common type of fastener used on an aircraft structure. The principle of driving a rivet is relatively simple.
- Drill several matching holes in the two pieces to be joined.
- Hold the components together with clamps or clecos.
- Slide in one solid rivet until the head of the rivet is firmly against the outer part of the structure.
- Hold the rivet head in place and then drive or buck the tail of the rivet from the other side with a bucking bar until the rivet is squeezed (deformed) to hold the pieces together tightly.
Rivets are strong because they fill the entire hole with a solid aluminum plug. They are also very light and inexpensive. However, setting rivets requires skill, and sometimes more than one person is needed to install them. The use of a pneumatic hammer (with a set shaped to the rivet head) and a bucking bar (used for the tail of the rivet) speeds up the installation process, which can involve hundreds or thousands of rivets, even on a modest-sized piece of structure. Riveting can be labor-intensive, but the process results in a strong, lightweight, and durable structure.
Most, if not all, commercial aircraft have pressurized fuselages, which means that the cabin pressure is increased to produce a differential pressure between the air inside the cabin and the outside atmosphere. Pressurization is achieved by designing an airtight fuselage that is pressurized with a compressed air source, typically from engine bleed air. In most pressurized airplanes, the cabin pressure is maintained at an altitude equivalent to approximately 6,000 ft to 8,000 ft (about 2,000 m to 2,500 m) to ensure good passenger comfort. Nevertheless, some passengers may still exhibit mild hypoxia symptoms (oxygen deprivation) during long-haul flights, contributing to the all-too-frequent malady known as jet lag.
Structurally, pressurization causes significant tensile and hoop stresses to be developed in the fuselage structure, as shown in the figure below, adding not only to the complexity of its design but also increasing its structural weight. The fuselage is an enormous pressure vessel that expands like a balloon as the aircraft climbs to altitude. The ceiling for most commercial transport airplanes is often limited by cabin pressurization requirements, which set a structural stress limit on the fuselage. Naturally, the stresses can be reduced by increasing the thickness of the fuselage skin; however, this approach also significantly increases the weight of the airframe.
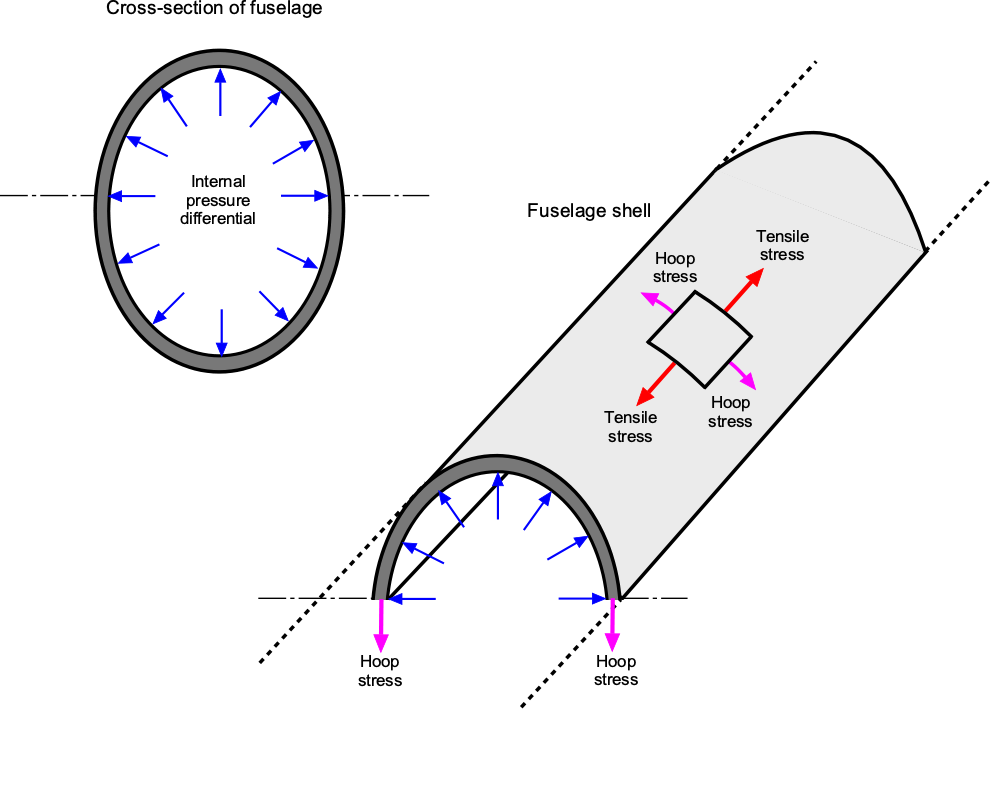
The hoop stress in a cylindrical pressure vessel is generally the dominant tensile stress and is given by
(5)
where is the differential pressure across the skin,
is the mean radius of the fuselage, and
is the wall (skin) thickness. The longitudinal or axial stress
is approximately half the hoop stress and is given by
(6)
These stress limits impose critical constraints on fuselage design. The maximum allowable cabin differential pressure, and hence the maximum cruise altitude, is bounded by the material strength and thickness of the fuselage skin. Although increasing skin thickness reduces stress levels, it also adds structural weight, diminishing payload capacity and fuel efficiency. Therefore, optimizing fuselage design involves balancing structural strength, weight efficiency, and operational ceiling.
Another type of semi-monocoque structure is the geodesic design, pioneered by the British aeronautical engineer Barnes Wallis in the 1930s. The famous Vickers Wellington bomber, shown in the photograph below, was built of a geodesic structure, and it proved its structural integrity even after suffering significant combat damage.

While a less common type of airframe design, this structure is relatively lightweight yet strong, and has also been used in spacecraft designs. While this type of geodesic construction has advantages, it tends to be more expensive to build and repair. It is unsuitable for pressurized fuselages because replacing the fabric covering with sheet metal quickly drives up the structural weight compared to other types of construction, such as the more common semi-monocoque design.
Empennage Structures
The tail assembly of an aircraft is referred to as the empennage. The structure of the vertical (fin) and horizontal stabilizers is very similar to that used in wing construction, including spars, ribs, and stringers, all of which are covered with a thin skin. They perform the same functions: shaping and supporting the structures and transferring stresses to the fuselage. However, the stabilators also have control surfaces, which means that additional structural requirements exist from the airloads produced by control deflections. For example, a rudder application causes a change in the force on the fin, resulting in a torsion or twisting effect. These loads are, in turn, applied to the fuselage as both a bending moment and a torsional twisting moment.
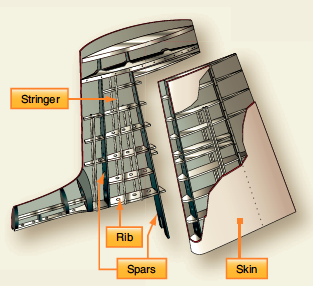
Flight Control Structures
An airplane’s primary flight control surfaces are the ailerons, elevators, and rudder. Other movable surfaces include flaps and spoilers. The ailerons are attached to the trailing edge of both wings and are used for roll control. The elevator, located on the trailing edge of the horizontal stabilizer, controls the aircraft’s pitch. The rudder is hinged to the trailing edge of the vertical stabilizer and gives yaw or directional control.
Control surfaces are typically made from an aluminum alloy structure built around a single spar member or torque tube to which ribs are fitted and skin is attached. Primary control surfaces and flaps can also be constructed from composite honeycomb materials, a method used primarily on larger commercial airliners where excessive weight growth is a concern. Other sandwich construction structures may include cabin floors, nose cones, and engine cowlings.
Winglets
A winglet is a vertical upturn of the wing tip, as shown in the figure below. Winglets are designed to reduce the drag created by wing tip vortices, i.e., the induced part of the total drag. Winglets are made from aluminum or composite materials and are often retrofitted to existing wings to improve the airplane’s performance. A winglet must be structurally attached to the main wing box to create a fully integrated design.
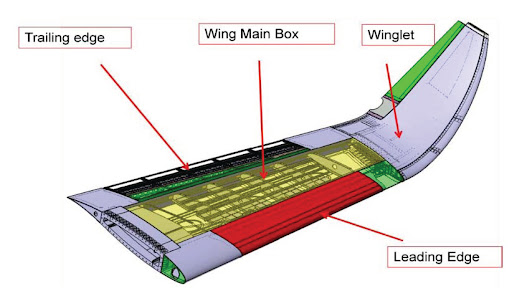
Stress Analyses
A structural stress analysis involves determining aerodynamic and other loads and evaluating the resulting stresses imposed on the structural components. While a stress analysis may be conducted on separate components or assemblies, any single structural member may be subjected to a combination of stresses from multiple loading paths. Therefore, a thorough stress analysis generally must consider the aircraft’s total structure to ensure it is strong and stiff enough to carry all flight and ground loads.
This type of stress analysis is performed using the finite-element method (FEM). The FEM is a numerical method in which the aircraft structure is modeled by a set of finite blocks or lattice elements interconnected at discrete points called nodes; an example of a lattice used for an entire aircraft is shown in the figure below. The process begins with creating a geometric model of the aircraft and its detailed components using Computer-Aided Design (CAD) software. Each block or finite element may have different properties, such as thickness and material characteristics, reflecting the characteristics of aerospace materials like composites and metal alloys, giving the FEM tremendous optimum design capabilities. Regions such as between the fuselage, the engine nacelles, the wings, and cutouts like cockpit windows require particular attention with FEM to avoid local stress concentrations.
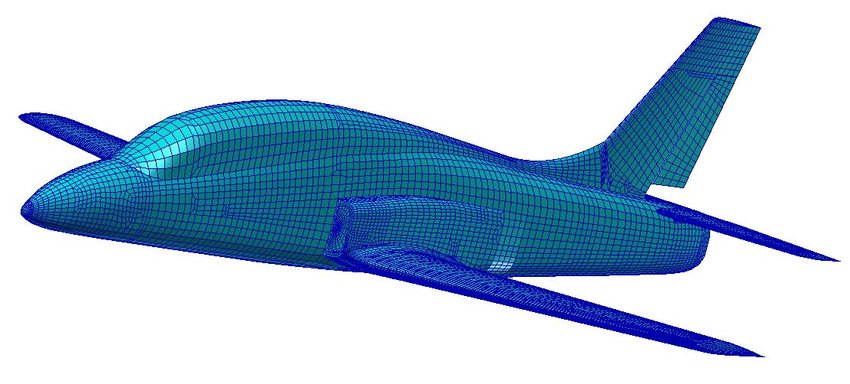
Material properties, such as Young’s modulus, Poisson’s ratio, and density, are assigned to each element. Boundary conditions, including constraints, loads, and perhaps even thermal effects, are applied to the model, representing the operating environment and mission requirements. The assembly of system equations involves the formulation of the stiffness matrix by aggregating the contributions from individual finite elements and the assembly of the load vector to account for applied loads and environmental conditions. For linear systems, the displacement vector is determined by solving the equation
(7)
where represents the stiffness matrix and
is the load vector comprising of forces and moments. This equation describes the relationship between the loads acting on all nodes in the mesh and the displacements and rotations at those nodes. The nodal displacements and rotations of the structure are the unknowns in the FEM.
Solution techniques in the FEM encompass a variety of numerical methods. One approach is to invert the stiffness matrix to find and solve for
. However, directly inverting a large matrix is not a numerically efficient process. Instead, preferred methods iteratively approximate the displacement vector to converge to a solution. Post-processing tools are then employed to visualize and interpret the results, as shown in the figure below for a spar lug, which is color-coded based on stress levels (blue indicating the lowest). Notice the higher stresses around the bolt holes. The idea is to distribute the stresses so that they “flow” smoothly into the primary attachment points without large concentrations.
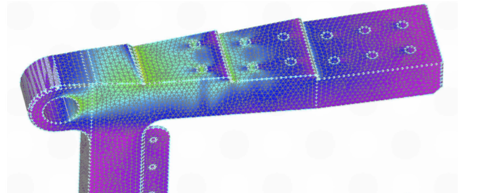
From the FEM results, engineers can assess the structural integrity of the flight vehicle by analyzing stresses, strains, and overall deformations to ensure that the vehicle and its components meet safety, performance, and certification requirements. In this regard, the design of an aircraft or spacecraft may involve finding the strongest and most durable structure with the minimum possible weight, while also ensuring good fatigue and corrosion resistance, as well as other desirable characteristics.
Fail-Safe & Safe-Life Structural Designs
Aerospace engineers have developed safe-life and fail-safe design philosophies for structural design. Fail-safe designs incorporate techniques, such as structural redundancy and multiple load paths, to prevent catastrophic failure in a single component. Safe life design is the philosophy that a component or system is designed not to fail during operational use within a specific period. This period may be defined by the number of flight hours, takeoffs and landings, years of operation, or some combination. Testing and analysis can estimate the expected life of the component or system, with a margin of safety also being applied. The part or component must be removed from operational service and scrapped at the end of its expected life.
The decision between a safe-life and a fail-safe structural design depends on a cost-benefit analysis of the likelihood and potential consequences of failures. The benefit of a safe-life design is freedom from specific inspection processes and maintenance cycles, which can save an operator a significant amount of time and money. However, fail-safe designs are usually heavier and more expensive. Safe-life designs are often simpler and lighter, aiming to minimize unplanned maintenance and the possibility of failure by designing components to last for a specific period.
An example of a safe-life versus failsafe structure is illustrated in the figure below for a wing spar, a critical component of an aircraft. The upper spar cap will be in compression, and the lower cap in tension; the lower cap is more essential regarding the likelihood of fatigue failure. Notice that in the event of a failure of the lower spar cap, the fail-safe structure has sufficient redundancy because of an alternative load path that can carry the bending moment loads. Unless the fatigue cracking of a safe-life structure is identified before progressing too far, the spar will fail catastrophically under load.
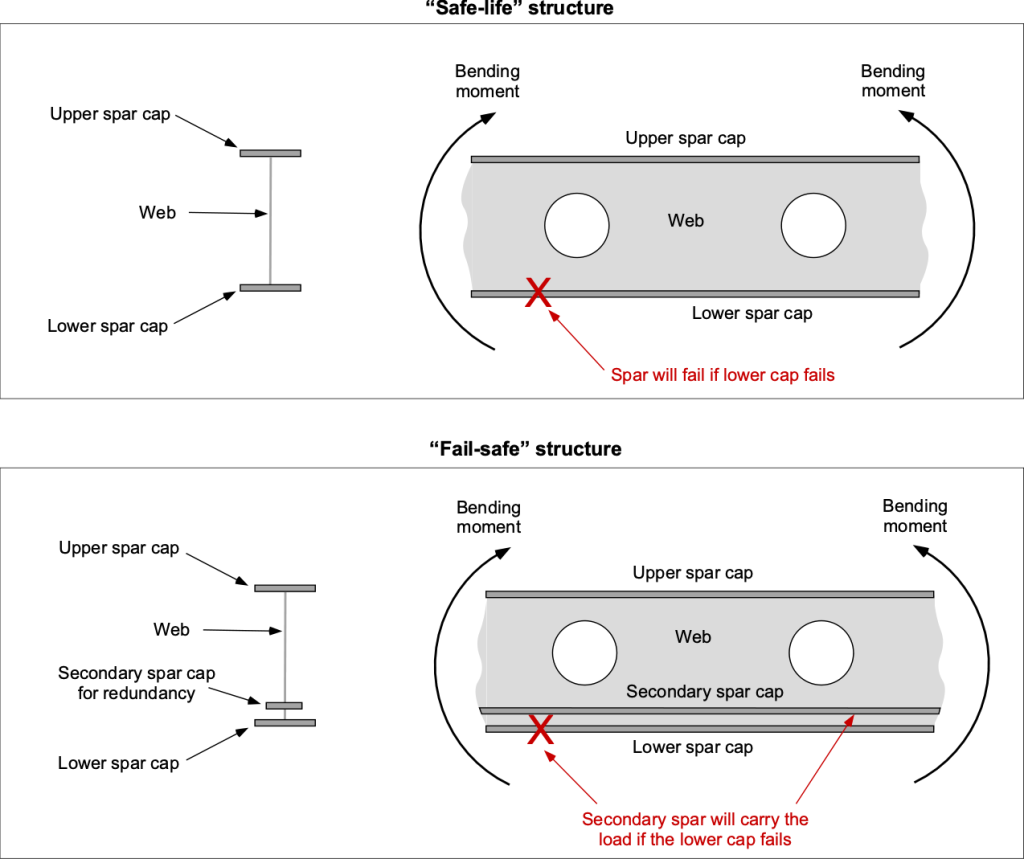
The final decision to employ one or the other design philosophy must be made on a case-by-case basis, and the specific application of the parts or systems to different types of airframes. For example, commercial airliners are designed using fail-safe principles, as are military aircraft. The use of a fail-safe design philosophy in the aircraft industry provides structural redundancy against damage that may occur during an aircraft’s service life. By incorporating fail-safe design features at the expense of some extra airframe weight, the consequences of a single component failure can be minimized, ensuring the safety of the aircraft and its passengers.
A small general aviation (GA) airplane may be designed using safe-life principles to save weight and cost, recognizing that it will likely be flown much less frequently and accumulate a significantly lower number of loading cycles over its life. This approach assumes that the components will not be subjected to a critical number of cycles during their lifespan and so do not require the same level of durability and safety factors as commercial or military aircraft. Nevertheless, catastrophic structural failures occur on aging GA airplanes, increasing the burden on the owner/operator for more frequent inspections.
Buckling
Aerospace structures have relatively thin structural members, including thin external skins. Buckling may occur when an aerospace structural component is subjected to high compressive stresses. Buckling is characterized by a sudden out-of-plane deflection of the structural member with increasing compressive loading, as illustrated in the figure below. Different types of buckling may occur depending on the kind of structure and the applied loads.
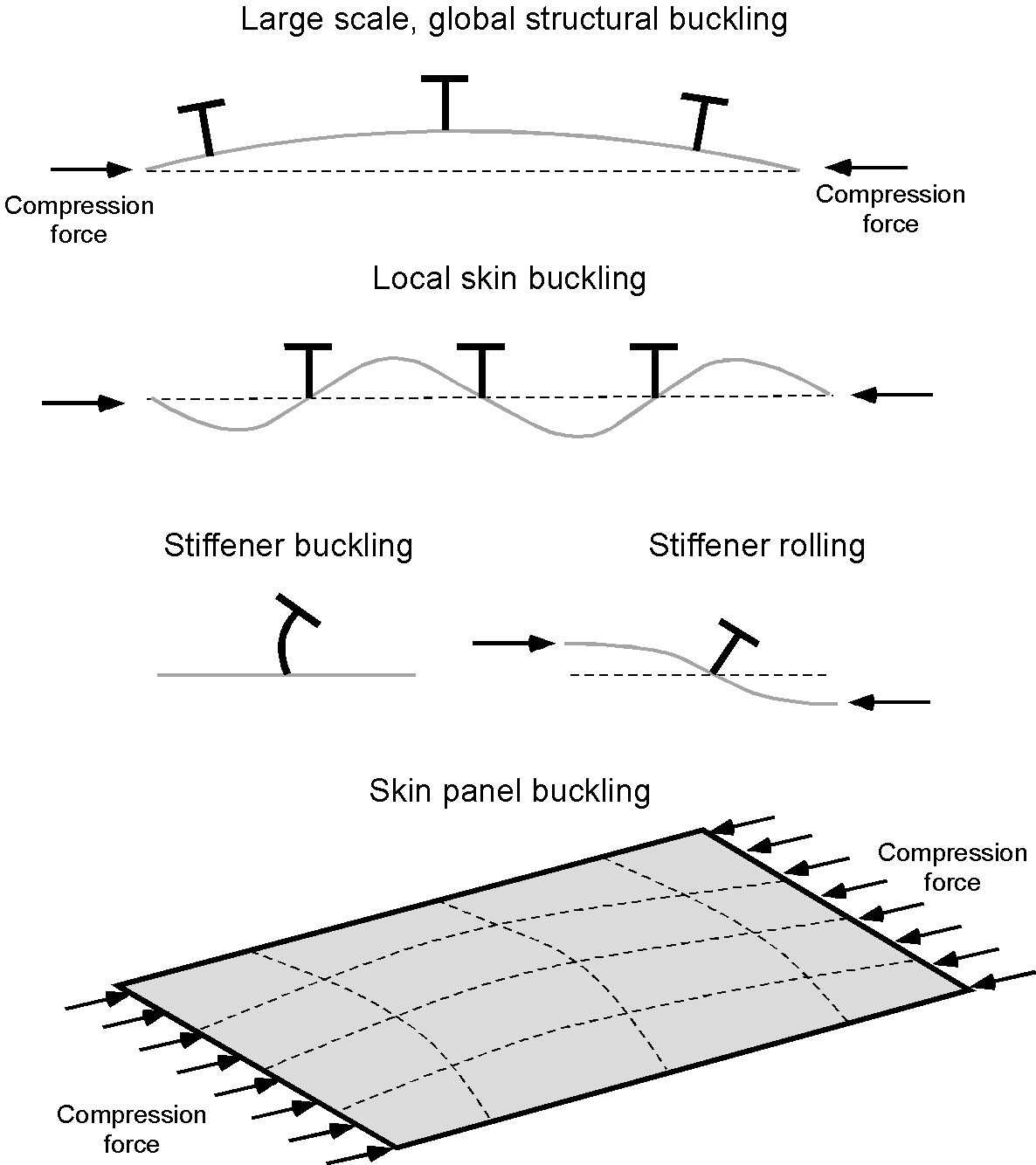
The thin skins on aerospace structures must be designed to prevent buckling under normally expected flight loads. This is done by supporting and stabilizing the skin from below using stringers or a substrate such as a honeycomb sublayer. However, stringers may also buckle when carrying high compressive loads, as shown in the image above. When they are under load, a certain amount of skin wrinkling of aerospace structures can generally be expected. Larger unsupported areas of the skin often tend to form mild waves or wrinkles, usually between frames and stiffeners, even under normal flight loads, as shown in the photograph below. Under these conditions, the skin develops a form of mild elastic buckling and carries the normal compressive loads for which it was designed; it will return to its undistorted shape when the load is removed. Repeated elastic buckling at higher stress levels, however, does tend to increase the likelihood of fatigue cracking of thin skins.
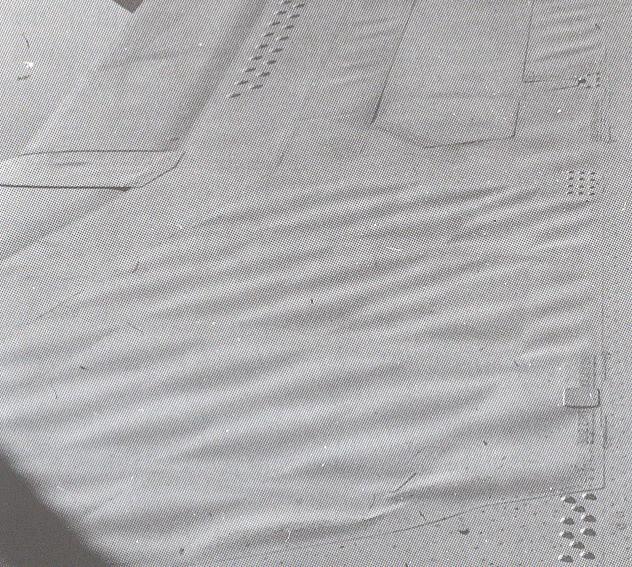
An aerospace structure may buckle, and its skins may wrinkle, even though the stresses are well below those needed to cause material failure. However, if sufficiently severe, buckling can result in permanent material deformations that significantly reduce the structure’s load-carrying capability. Further loading on a structure after severe buckling can lead to structural failure. The example shown in the image below is from a NASA test on a representative spacecraft structure, where the stringers have suffered permanent (plastic) buckling, substantially reducing the component’s strength.
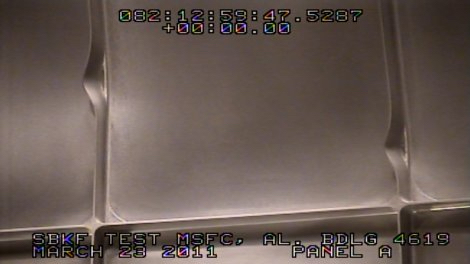
The onset of buckling can be predicted using theoretical methods first developed by Leonhard Euler. The Euler buckling formula allows a prediction of the maximum axial load an “ideal” structural member in the form of a column can carry before buckling. An ideal component is perfectly straight, made of a uniform homogeneous material, and free from any initial stress.
When the applied load reaches a critical load, the column reaches a state of unstable equilibrium. In this condition, any small lateral load will cause buckling. The buckling force or critical force, , can be written as
where is Young’s modulus of elasticity,
is the second moment of area of the cross-section of the column, and
is the unsupported length. The value of
, the effective length factor, depends on the end conditions of the column. For example, if both ends are pin-jointed (i.e., fixed but free to rotate), then
. If both ends are rigidly fixed to prevent rotational movement (i.e., encastré), then
, and the buckling force is twice as high. There are similar buckling formulae for plates and shells.
Check Your Understanding #3 – Estimating a buckling load on a structural member
A structural member in a wing structure is an unsupported aluminum alloy column measuring 2.1 m in length. The member can be considered fully encastré at both ends and has a second moment of area of 0.18 cm. Find the force required to produce compressive buckling. Young’s modulus for the aluminum alloy material is 69.0 GPa.
Show solution/hide solution.
The Euler buckling load can be calculated using
In this case, the member is encastré at both ends, so = 0.5. Inserting the known values and being careful to convert quantities to base SI units gives
Thermal Considerations
Thermal expansion issues in aerospace structures may be a necessary consideration in airframe design. Spacecraft and aircraft structures can encounter wide swings in temperature, ranging from the cold of high altitudes or space to the kinetic heating in supersonic flight to the intense heat of atmospheric re-entry. When materials expand or contract in response to temperature changes, they can lead to significant structural stresses and potential failures if not properly managed.
Different materials expand at different rates, a property quantified by the coefficient of thermal expansion (CTE). In aerospace structures, materials with mismatched coefficients of thermal expansion (CTEs) can lead to differential expansion or contraction, causing stress concentrations at the interfaces where these materials meet. For example, composites and metals in the same structure might expand or contract differently when exposed to temperature changes, potentially leading to delamination or cracking.
Engineers address these thermal issues through careful material selection, designing joints and interfaces that can accommodate movement, and incorporating thermal isolation or control techniques to minimize temperature gradients. A good example is the wing ribs used on the Concorde, an example being shown in the photograph below. Some of the webs were made of pin-jointed rods, allowing the structure to expand thermally from kinetic heating in supersonic flight without creating high stresses—some stringers in the wing skins fitted in sliding joints in the ribs for the same reason. The Concorde also used high-temperature stainless steel honeycomb structural components. Today, advanced materials like carbon composites and thermal barrier coatings can mitigate thermal effects and enhance the durability of aerospace structures.
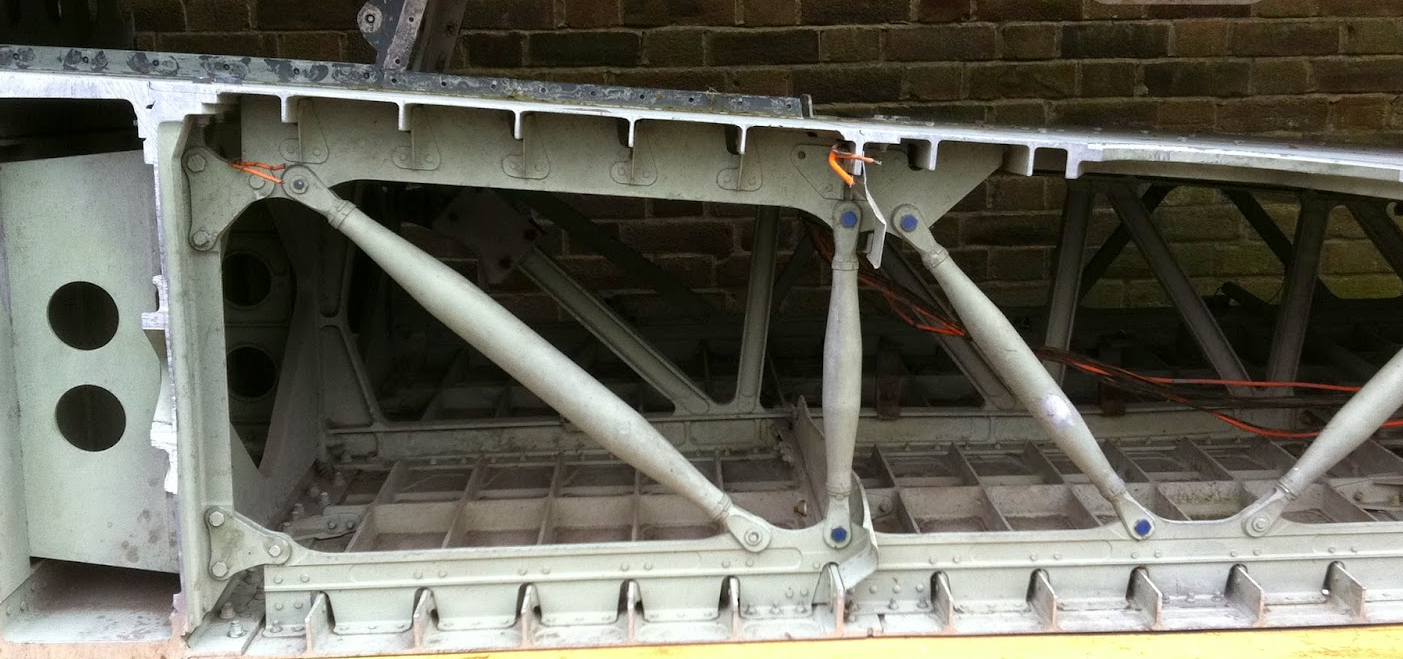
Launch and re-entry vehicles are subject to high aerodynamic loads and severe kinetic heating effects, which pose additional challenges in designing the structure and selecting the appropriate structural materials. Aerodynamic heating can significantly soften and weaken all materials at high temperatures. Besides designing for strength and stiffness, additional methods of protecting the structure may be needed, such as silica tiles on the Space Shuttle, to protect the airframe from kinetic heating during re-entry.
An example of a state-of-the-art spacecraft thermal protection system, based on an inflatable concept, is illustrated in the figure below. A further engineering challenge is that these re-entry environments cannot be easily simulated on Earth or fully modeled analytically under the expected combined mechanical and thermal loads. Hence, the design risks are higher than for an aircraft.
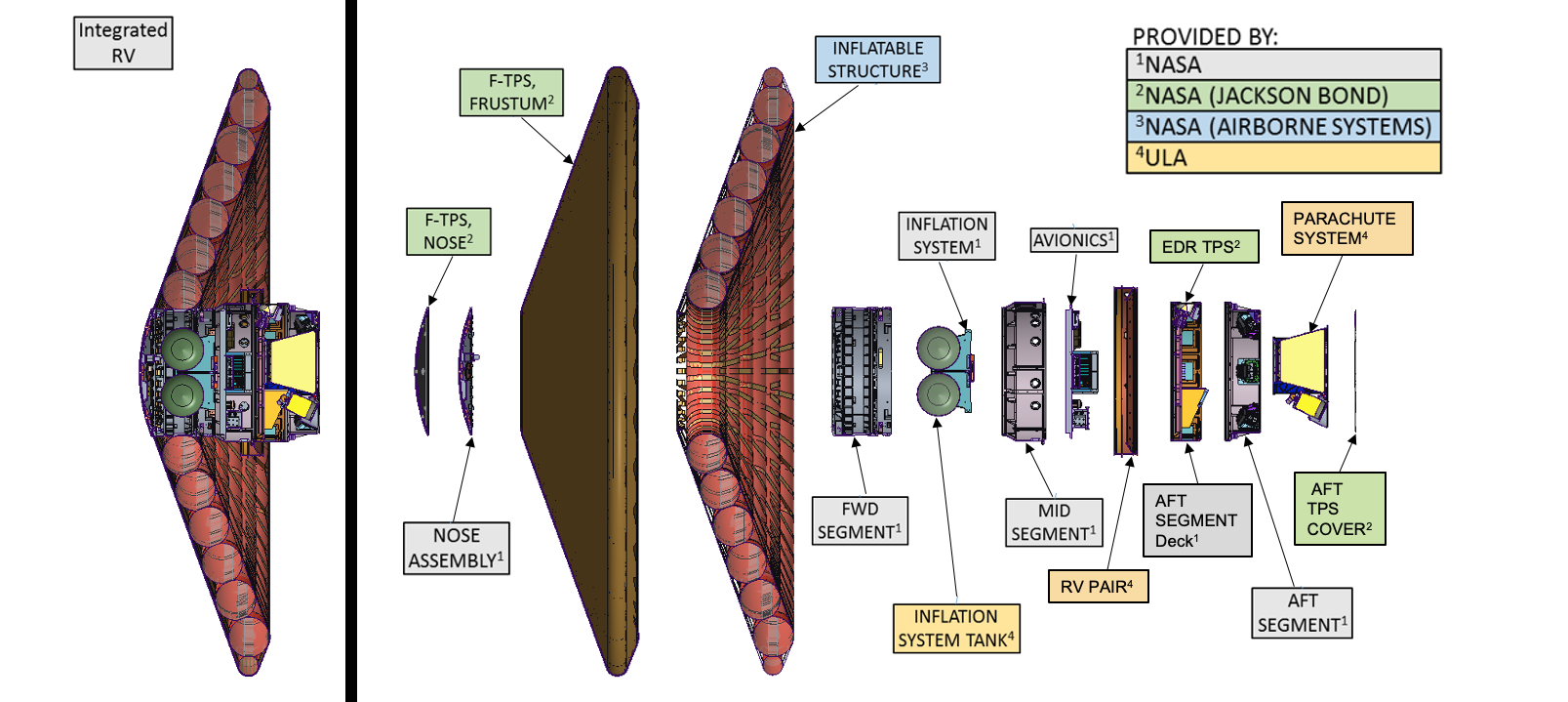
Airframe Weight Estimation
A key goal in flight vehicle design is to achieve maximum performance with the lowest structural weight and cost. For a given type of aircraft, its price is roughly proportional to its empty weight. However, this goal is not always so readily obtained in practice. In this regard, “cost” includes both the acquisition cost of the vehicle or its “price” as well as its operational costs. A flight vehicle comprises many parts, generally combined into major groups or sub-assemblies, such as wings, fuselage, tail, undercarriage, and propulsion system. Of course, the weight of a new aircraft design is never known a priori and must be obtained iteratively as an integral part of the design process.
For preliminary airframe design, weight estimates can be performed using historical data for existing aircraft, such as the approaches discussed by Ramer and the related approaches documented by Torenbeek and Roskam. As the design process is refined, which will inevitably include computer-aided design (CAD), finite element methods (FEM), and computational fluid dynamics (CFD), the estimated weight of the components and sub-assemblies can be obtained more accurately. The effects of weight on performance and cost can then be reassessed, and the structural design can be iteratively refined toward closure. It should be recognized that the weight of an airframe design generally grows disproportionately quickly with increasing size (i.e., the so-called “square-cube law“), which becomes a significant design challenge for commercial aircraft, in particular.
Advanced materials and sophisticated manufacturing techniques may be considered, which can reduce the required material and lower the airframe weight. The additional design time and investments in tooling required to achieve significant airframe weight savings may result in a higher useful weight for the aircraft (i.e., more fuel load and/or payload), but not necessarily a lower acquisition cost. Nevertheless, the long-term economics of higher payloads and lower operational costs for airliners are very attractive to an aircraft operator such as an airline.
What is the payload?
Payload refers to the weight, , carried on the aircraft that pays the bills. The payload comprises the passengers, their baggage, and cargo. The useful load,
, includes everything on board the aircraft that is not part of the aircraft’s empty weight,
. The empty weight comprises the weight of the airframe, engines, and all necessary systems for flight. Fuel is not a payload but part of the useful load. The useful weight,
, therefore, is the sum of the payload weight,
, and the fuel weight,
, i.e.,
The useful load and, hence, the payload weight can vary depending on the aircraft type, the intended purpose of the flight, the altitude at which the aircraft flies, and the flight distance. For most aircraft, the payload and fuel load can be traded off against each other, allowing for more payload to be carried with a lower fuel load. Payload is an essential consideration for airlines because they need to have as much payload as possible but also ensure that they take sufficient fuel for the flight and do not exceed the maximum certified gross takeoff weight, , for any given aircraft, i.e.,
Spacecraft Structures
Many of the structural design challenges for spacecraft are similar to those for aircraft, including the need for high-strength-to-weight materials and low manufacturing costs. Most space vehicles are constructed using components made of metallic materials, such as aluminum and titanium, and composite sandwich materials, which are both strong and lightweight, helping to avoid buckling under high applied loads. As with aircraft structures, spacecraft structures are mainly thin-walled, semi-monocoque designs. They are subject to most, if not all, of the issues associated with aircraft structural design, an example being shown in the photograph below. This spacecraft’s structure is made of aluminum, and to maximize its strength-to-weight ratio, it features a triangular iso grid pattern with curved conic sections, similar to a geodesic construction.
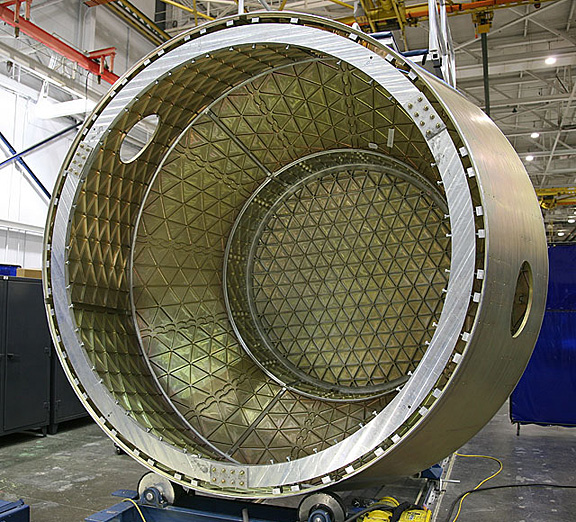
A significant challenge in designing launch vehicles is the structural design of fuel tanks, which are large pressure vessels often filled with cryogenic liquids. In this case, the embrittlement of metals at low temperatures is a significant consideration, as internal stresses are caused by differential temperatures, for example, between liquid hydrogen and oxygen tanks. Cryogenic propellants must be stored at extremely low temperatures to remain in a liquid state. The most common cryogenic propellants include liquid hydrogen (LH2), liquid oxygen (LOX), and liquid methane (LCH4). Their storage tanks are made from lightweight materials such as aluminum alloys, stainless steel, or advanced composites. They are equipped with multilayer insulation and vacuum jackets to minimize heat transfer. The hemispherical and cylindrical shapes help evenly distribute the structural stresses produced by internal pressures, while maintaining their structural integrity against buckling through the use of integral support structures.
Cryogenic tanks are vital for space launch vehicles, such as the SpaceX Falcon 9 and NASA’s Space Launch System (SLS), as well as for deep space missions where long-term propellant storage is necessary. An example of the liquid hydrogen fuel tank used on NASA’s SLS rocket is shown below. This tank was made using friction welding, which relies on the friction generated between a rotating tool and the material to heat and soften but not melt the workpieces. The tool then stirs the softened material across the joint, producing a solid-state weld. This process yields high-quality welds with minimal defects, reduced distortion, and enhanced mechanical properties compared to traditional welding methods. Composite materials have also been utilized in the design of rocket fuel tanks.
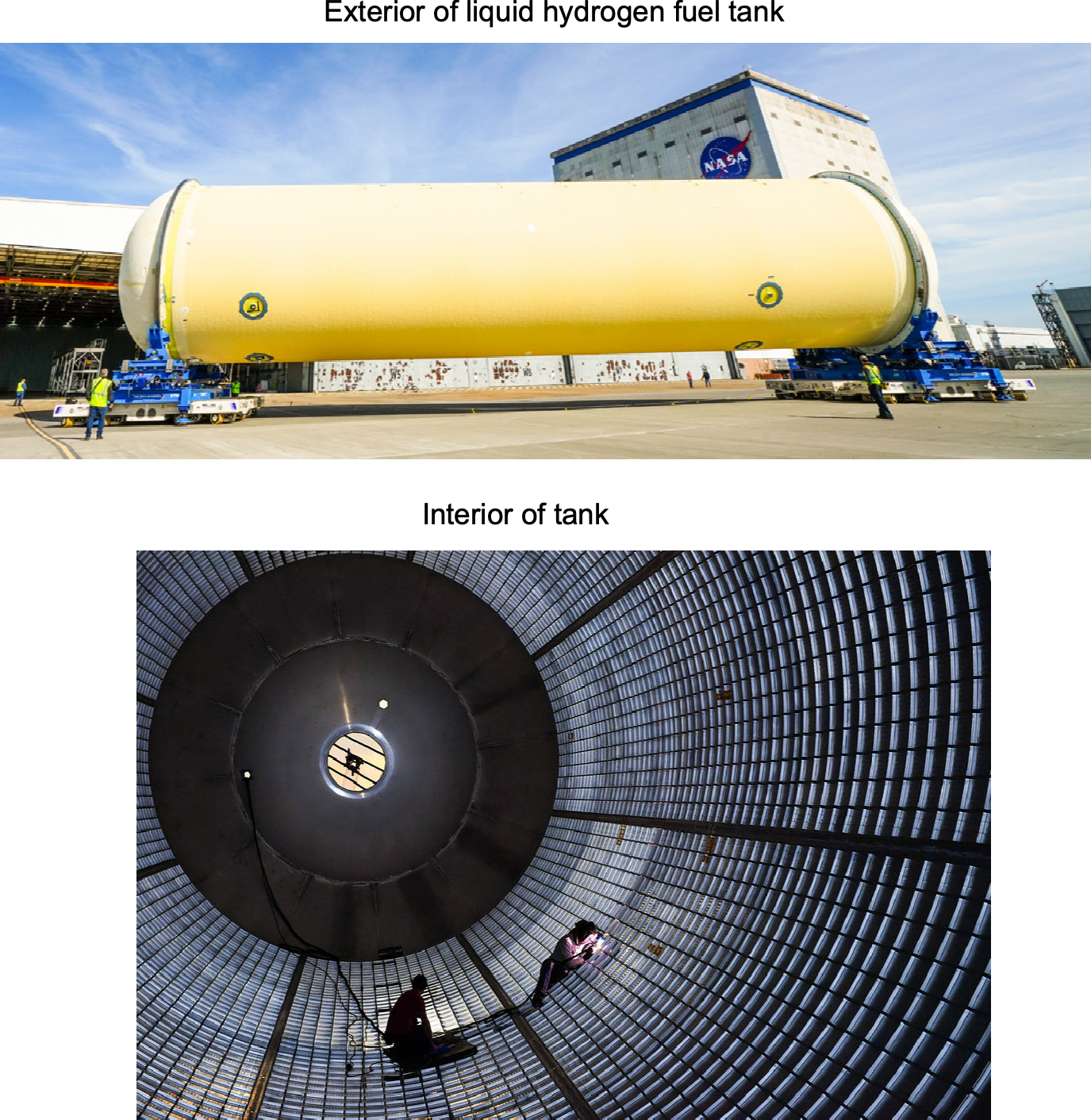
Managing boil-off gases and maintaining the low temperatures of cryogenic propellants are significant challenges. These are addressed through both active cooling systems and passive insulation. Tanks are integrated with sophisticated feed lines and monitoring systems to ensure a controlled supply of propellants to rocket engines, along with sensors to track pressure, temperature, and liquid levels. Pressure management systems with vents and relief valves are also needed to handle the high pressures of cryogenic liquids.
Summary & Closure
Aerospace structures require a unique combination of strength and lightness. The finite element method (FEM) is widely used to design structures that meet specific requirements while minimizing weight. Stressed skin structures made of aluminum alloys have been the dominant material for aerospace applications for many years, providing the necessary strength and durability for most aircraft and spacecraft. However, composite materials, such as carbon fiber-reinforced polymers, have gained increasing popularity in recent years, particularly for primary structures like wings and fuselages. Using composites allows for improved strength-to-weight ratio and greater structural design flexibility, making them an excellent alternative to aluminum alloys in many aerospace applications.
The design of spacecraft structures parallels that of aircraft in many ways. Advanced materials and fabrication techniques, such as carbon fiber composites and friction stir welding, are employed to achieve high strength-to-weight ratios. Spacecraft structures designed for cryogenic applications present unique technical challenges, as they must store and manage cryogenic propellants at extremely low temperatures, such as liquid hydrogen and oxygen. The design and engineering of spacecraft structures are critical to mission success, ensuring reliability and durability while optimizing for weight and efficiency.
5-Question Self-Assessment Quickquiz
For Further Thought or Discussion
- List some of the relative advantages of wood and fabric airplane construction versus stressed metallic skin construction.
- Research the manufacturing methods of making airplanes using conventional riveted construction.
- What are the primary potential failure modes in aerospace structures, and how are they mitigated in design and manufacturing?
- What are the fundamental differences between aerospace structures and structures in other engineering disciplines?
- Discuss the challenges and considerations in designing flight vehicle structures for supersonic and hypersonic flight.
Other Useful Online Resources
To learn more about flight vehicle structures, try some of these online resources:
- Video lecture on aircraft structures and loads applied to an airframe.
- A short video explaining wooden airframe structures and the selection of the wood.
- Great video lecture on aerospace structures: Airframe Basics.
- Test your knowledge of the construction of an aircraft: Engineering a Jetliner.
- Lecture series on advanced aircraft structures by Dr. Goyal.
- Learn how to buck a solid rivet for an airplane structure.
- Aircraft conversion XXL – A cargo plane is born.
- The author is grateful to his structures teacher, Professor Henry Wong. He was an engineer for the Armstrong Siddeley Company, the Hunting Percival Aircraft Company, and the de Havilland Aircraft Company. Dr. Wong worked on the investigations of the De Havilland Comet airliner crashes, during which time significant advances were made in understanding the metal fatigue phenomenon. He was a Professor of Aeronautics and Fluid Mechanics at the University of Glasgow from 1960 to 1987. ↵