47 Airplane Performance Envelopes
Introduction
All aircraft have operational limits regarding the maximum and minimum airspeeds and altitudes at which they can fly in steady, level, unaccelerated flight, e.g., within the airspeed versus altitude boundary, as shown in the figure below. Notice that, by design, some aircraft, such as military supersonic-capable fighter jets, can fly faster and higher over a broader range of flight conditions than other types of airplanes. However, remember that military aircraft also have different types of missions. In comparison, commercial jet airplanes are highly specialized “point designs” in that they are designed for long periods of cruising at high altitudes at a specific airspeed (or Mach number). Turboprops are often used for short-haul flights. While they fly at lower altitudes and airspeeds, they are better suited for operating out of shorter runways and have greater climb rates at lower airspeeds than jets. They are also better for operating out of airports situated in mountainous terrain.
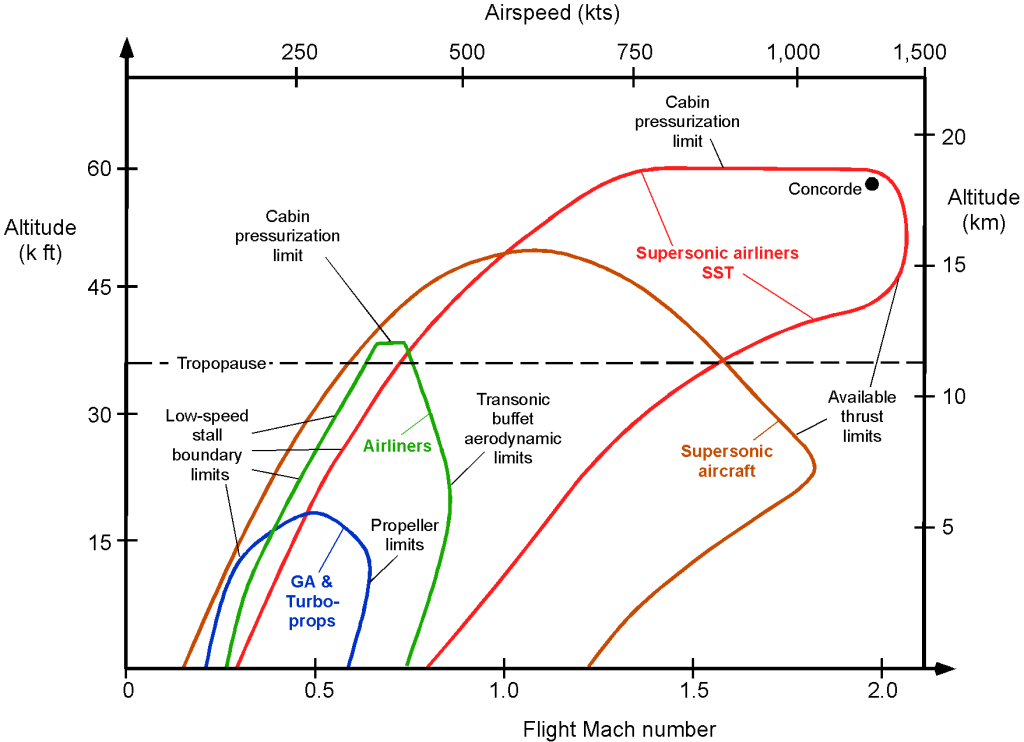
The area inside the boundaries that limit normal flight operations of an aircraft is referred to as the operational flight envelope. The flight corridor is often referred to as the speed range or band over which an airplane can fly at any given altitude and weight without encountering any flight limits. The limits of the envelope are defined and set based on several criteria, such as:
- The highest achievable Mach number.
- The engine power available, e.g., for a turboprop or piston engine.
- The thrust available, e.g., for a turbojet or turbofan.
- The onset of maximum structural loads.
- The onset of aeroelastic effects, such as flutter or buffeting.
- Limits could also be set by excessive aerodynamic heating for supersonic aircraft.
Learning Objectives
- Understand the meaning of an airplane’s flight envelope and a flight corridor.
- Know about the various factors that may limit the operational flight envelope of an airplane, including the onset of stall.
- Understand the phenomenon of wave drag and why it can also limit the flight envelope.
- Be aware of the concept of reducing drag from compressibility effects by utilizing supercritical wing design and the area rule.
Flight Envelopes
The size and shape of the flight envelope (or flight corridor) depend on the type of airplane, specifically whether it is propeller-driven or jet-powered, has an unpressurized or pressurized fuselage, and whether it is designed for subsonic, transonic, or supersonic flight. Naturally, the exact size and shape of the envelope for any given airplane also depend on the properties of the atmosphere, particularly the air’s density and temperature. Generally, the lowest possible airspeed of an airplane (either jet-powered or propeller-driven) is dictated by the onset of wing stall, which determines the left-side boundary of the flight envelope. This stalling airspeed will be a function of the airplane’s weight and altitude, as well as the wing flap settings and whether the undercarriage is up or down.
The right side of the boundary will be set by the highest possible airspeed, which is usually limited by the power available (for propeller-driven airplanes) or the thrust available (for jet engines) to overcome drag, a function of the airplane’s shape and flight Mach number. The right-side boundary may also be limited by the onset of transonic buffeting effects, control system “buzz,” or the onset of wing flutter.
The upper edge of the flight envelope is the maximum attainable altitude, referred to as the operational ceiling. The ceiling is the altitude above which an aircraft cannot climb, typically defined by a threshold of a diminishing rate of climb of less than 100 ft/min. The attainable flight ceiling depends on the excess power available relative to the aircraft’s aerodynamic characteristics and other factors, including weight. In some cases, however, such as on most commercial airplanes, the flight ceiling is limited by the onset of wave drag or transonic buffet or by the airplane reaching some maximum structural loads associated with the pressurization of the fuselage (which is a trade with airframe weight), even though the airplane may have the excess power available to achieve higher flight altitudes.
Trimmed Flight
In a steady, level, unaccelerated flight, the airplane’s three forces (lift, drag, and side force) and the three corresponding moments (pitching, rolling, and yawing) are perfectly balanced. In this case, the airplane is said to be in trim, as shown in the figure below. The balance of forces in steady trim is that vertical equilibrium requires that lift = weight
and horizontal equilibrium requires that thrust
= drag
, i.e.,
(1)
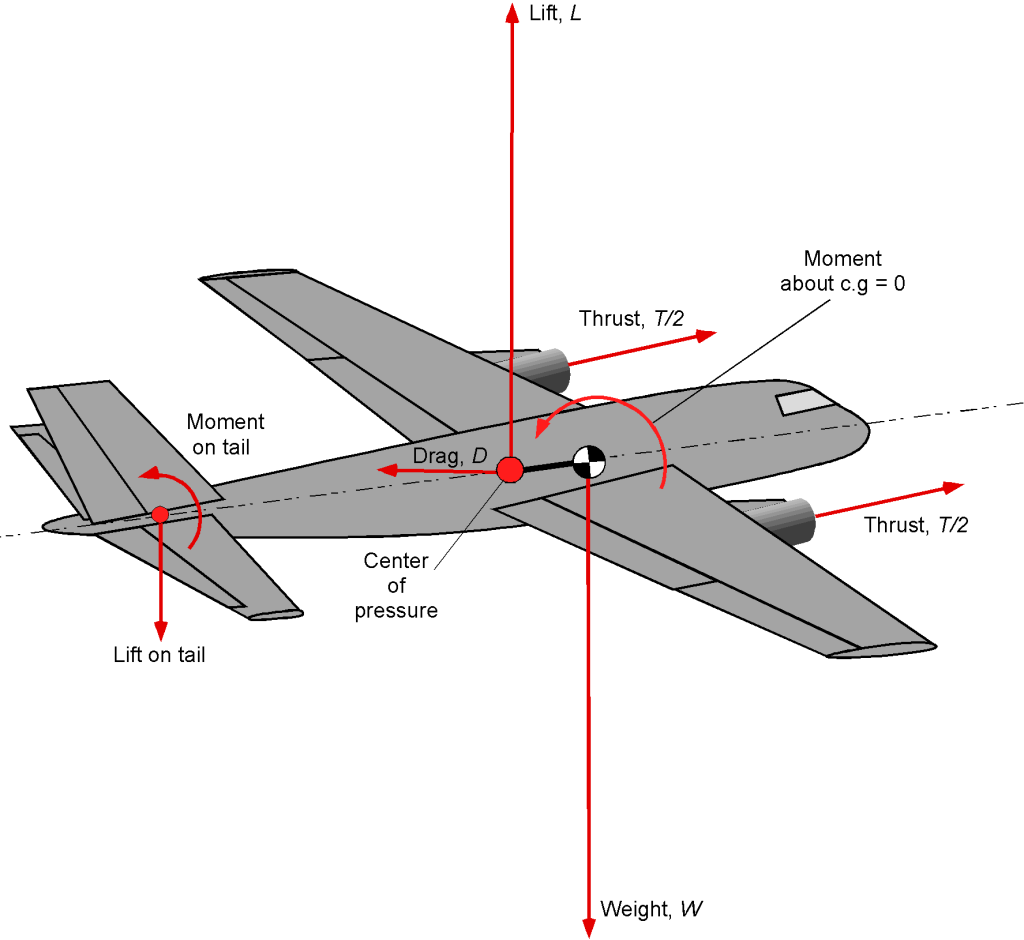
In this case, another assumption is that the thrust vector’s line of action is primarily aligned with the flight direction. However, full flight trim also requires that the airplane have a moment balance in pitch, roll, and yaw about its center of gravity. Therefore, the side force is also assumed to be zero in trimmed flight.
Remember that the wings generate lift to overcome the weight, and the engines provide the propulsive force to overcome the drag of the airplane, generating this thrust that requires a source of power and fuel. In terms of basic aerodynamics, for vertical equilibrium, then
(2)
where is the air density in which the airplane is flying,
is the reference wing area, and
is the total wing lift coefficient (the assumption here is that the wings generate all lift). Notice that
where
comes from the ISA model, i.e.,
(3)
Rearranging this equation allows us to solve for the lift coefficient that needs to be produced on the wing for a given flight speed, i.e.,
(4)
or the flight speed that corresponds to a given lift coefficient, i.e.,
(5)
Recall that the ratio of an airplane’s weight to its lifting wing area, , is called wing loading. Notice that the lift coefficient is proportional to weight (or to wing loading) but decreases with the square of the airspeed. The lift coefficient also increases with altitude for a given true airspeed and weight as the value of
decreases.
Stalling Airspeeds
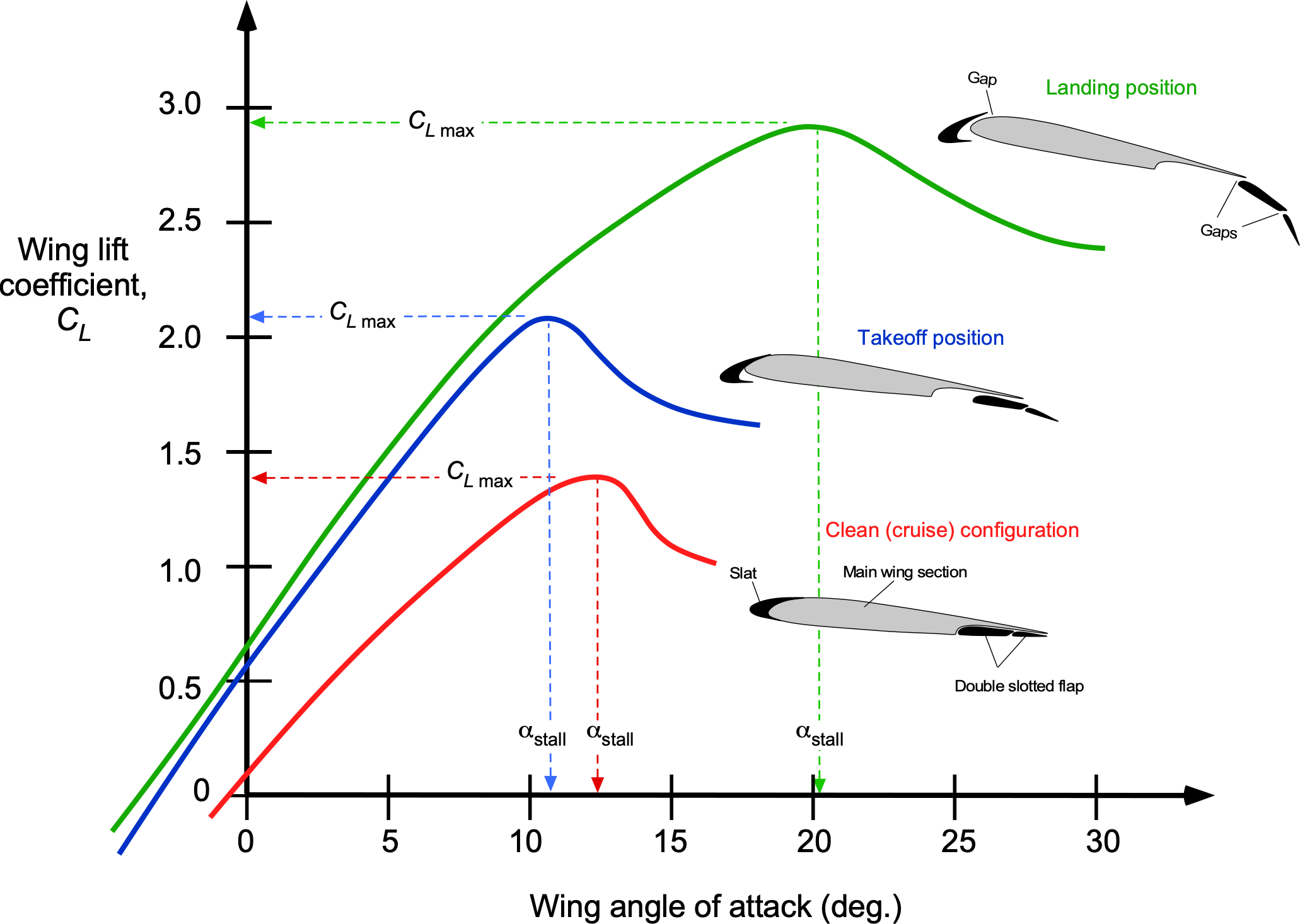
Although the value of may not be precisely determined by calculation, it can be indirectly determined from flight tests with the airplane through measurements of true airspeed and density altitude. After determining the value of
for the wing, the stall speed in steady-level flight can be solved at any weight and density altitude. i.e.,
(6)
using the value of from the ISA model, i.e., based on the prevailing pressure altitude and outside air temperature. Notice that for a given
, the stalling speed depends on the wing loading,
, i.e., all things being equal, an airplane with a higher wing loading will stall at a higher airspeed.
If a linear lift-curve slope of the wing is assumed, say , then the angle of attack of the wing
(measured relative to the zero-lift angle) can be calculated using
(7)
and so the stall angle of attack will be
(8)
the value of typically being less than 15
at low Mach numbers and lower than that at higher Mach numbers, e.g.,
may be as low as 5
at a Mach number of 0.7. However, it is essential to recognize that a wing will stall at any airspeed if the angle of attack is sufficiently high. For this reason, caution must be used when referring to stall speeds.
In summary, four conclusions can be drawn from the use of Eq. 6, all of which apply to level, unaccelerated flight:
- Stall speed,
, will increase with the increasing weight of the airplane.
will increase with increasing density altitude, i.e., with a lowering of the air density.
will decrease with increasing values of wing
, which, as previously discussed, can be achieved by the application of wing flaps and/or leading-edge slats.
will decrease with increasing wing area. Increased lifting wing area is also possible with certain types of flaps, such as Fowler flaps.
Stall airspeeds, and so the identification of the boundary on the left side of the flight envelope, is carefully measured during flight testing. Besides measurements of stalling airspeeds, the actual stall development on aircraft wings can be studied by placing strips of yarn called “tufts” all over the wing’s upper surface, as shown in the photograph below. The tufts are arranged in orderly rows, spanwise and chordwise, over the wing surface. The tufts are free to move around in the airflow. When the tufts are blown straight back, the flow is fully attached. However, suppose the tufts change direction and lift up from the surface. In that case, the flow at those locations is inevitably separated, and this condition is likely an indicator of an incipient stall on the wing.
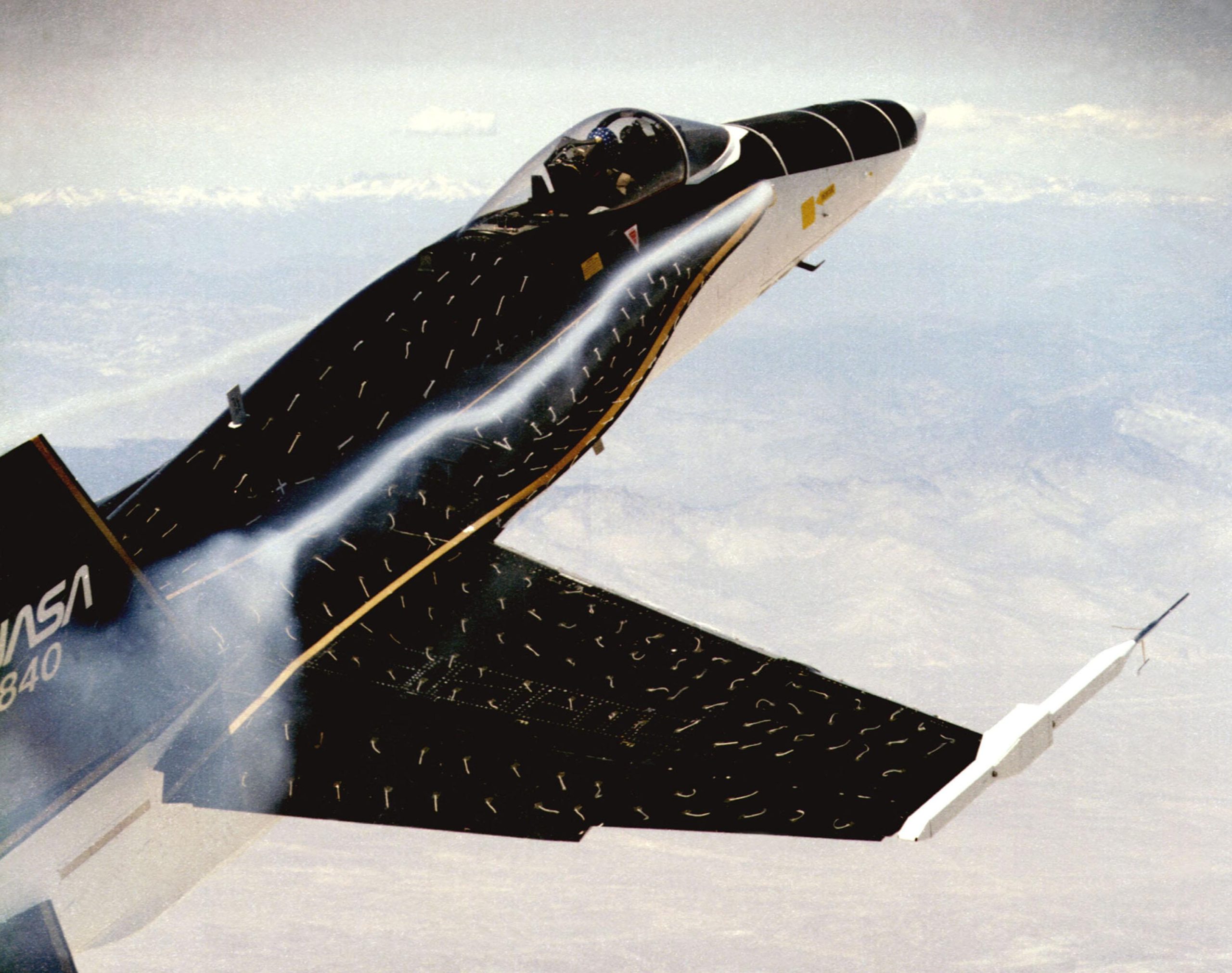
The stall patterns that develop on any given wing depend on many factors. It is desirable that the stall starts at the wing’s root and works forward and outward. The consequence of this behavior is buffeting, which allows the pilot to recognize the onset of stall before it progresses too far. It is expected that the airplane also tends to pitch down naturally at the stall, reducing the wing’s angle of attack and suppressing further stall developments. It is also essential that the wing’s outer parts have a fully attached flow, so there is no tendency for the aircraft to roll, and that the ailerons are fully effective in their usual operational sense. Some aircraft have been found to exhibit control reversals and spin tendencies during stall testing, a potentially hazardous behavior that can disqualify them from receiving a certificate of airworthiness.
Limiting (Maximum) Cruise Speeds
The figure below illustrates a historical trend of how cruise airspeeds for commercial transport airplanes have increased over the decades, a direct consequence of aeronautical technology’s rapid advancements and maturation. Of course, the introduction of the jet engine was responsible for the more rapid growth in the achievable cruise speeds obtained after 1960, first with the turbojet and later with turbofans.
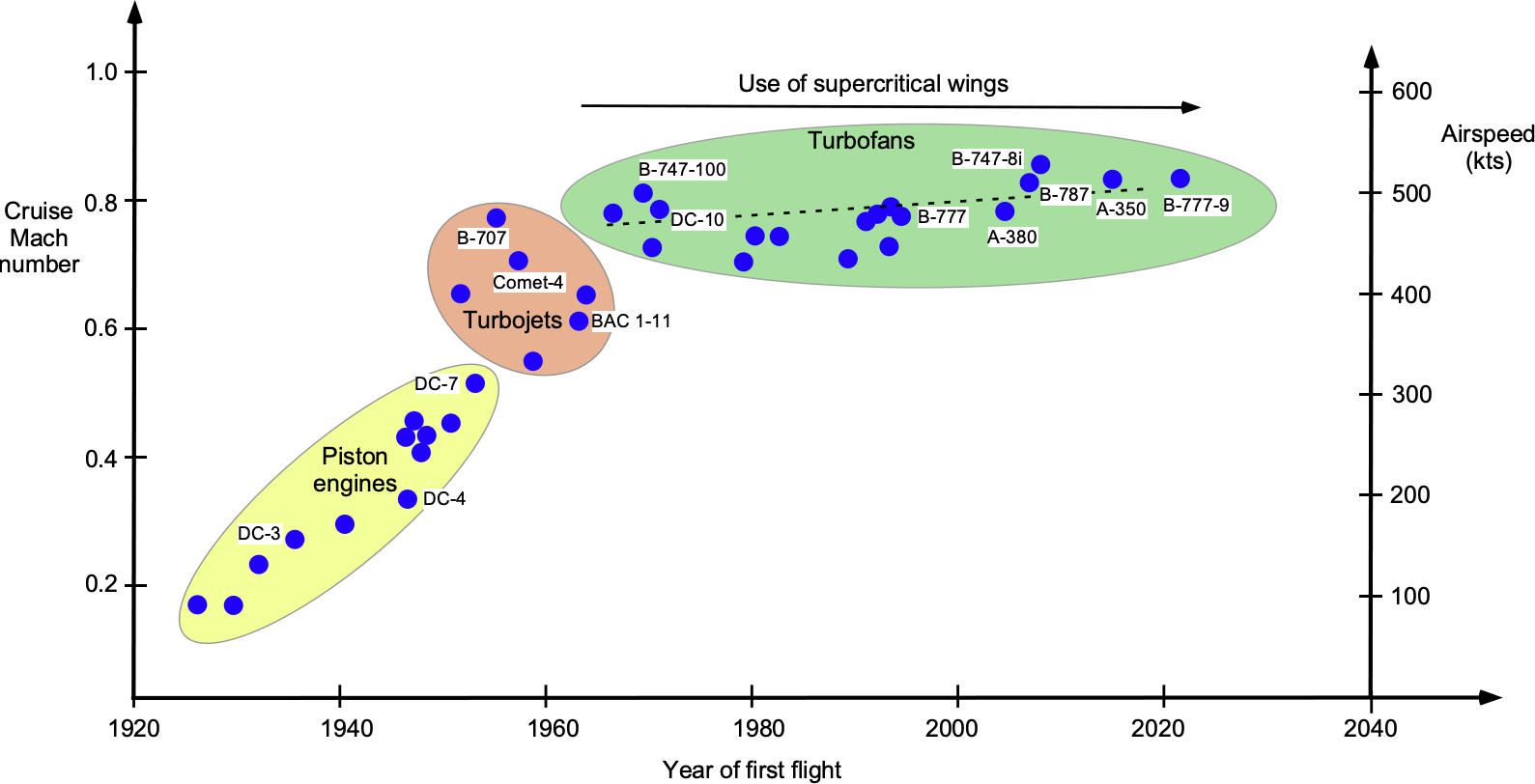
However, it can also be seen that since the early 1970s, the cruise airspeeds for commercial airplanes have plateaued, with corresponding achievable cruise flight Mach numbers in the range of 0.8 to 0.85. There are a couple of exceptions to this trend with the Anglo-French Concorde and the Russian Tu-144, but these airplanes were explicitly designed to be at supersonic Mach numbers. While supercritical wing designs have extended the flight envelope of airliners to higher transonic Mach numbers of about 0.85, the eventual onset of wave drag and shock-induced buffeting remains a physics-based barrier to faster flight.
Supercritical Flows & Drag Rise
One reason cruise speeds for commercial airliners have reached a plateau is because of the buildup of high drag on a wing as transonic flow conditions are approached. The fundamental physics of what happens on the wing section is shown in the figure below. The drag buildup resulting from the development of compressibility and shock waves requires significantly more thrust to overcome. Additionally, operating at higher flight Mach numbers presents other issues, such as the onset of shock-induced flow separation and buffeting, as previously discussed.
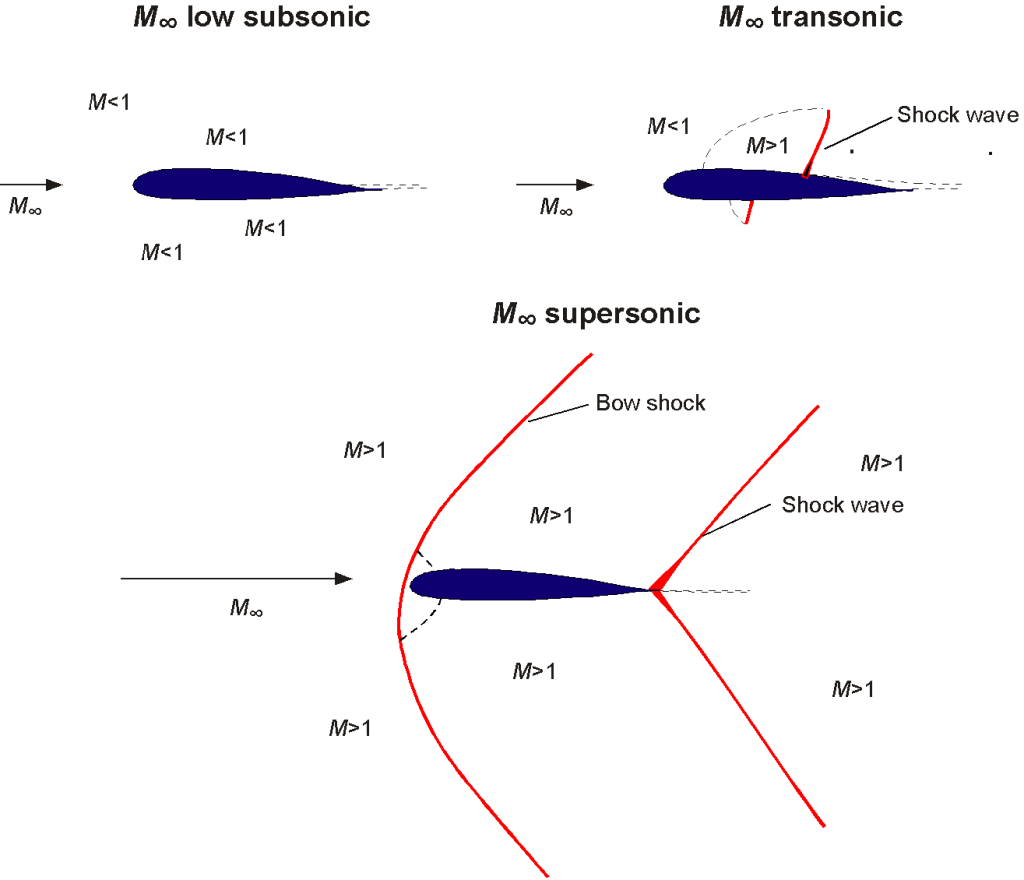
At some freestream Mach number, the local flow at a point on the wing’s surface reaches sonic conditions, known as the critical Mach number. As the freestream Mach number increases further, a small pocket of supersonic flow develops on the wing section, resulting in a weak shock wave in the flow. As the Mach number continues to increase, the shock strengthens and moves aft over the wing section, forming a supersonic region. An associated shock wave also develops on the lower surface, although this is much weaker. This condition is known as the well-established transonic flow region, where the formation of shock waves leads to an energy loss that manifests as a type of drag called wave drag. Wave drag causes the total drag on the wing to increase rapidly as the Mach number approaches one, as shown in the figure below.
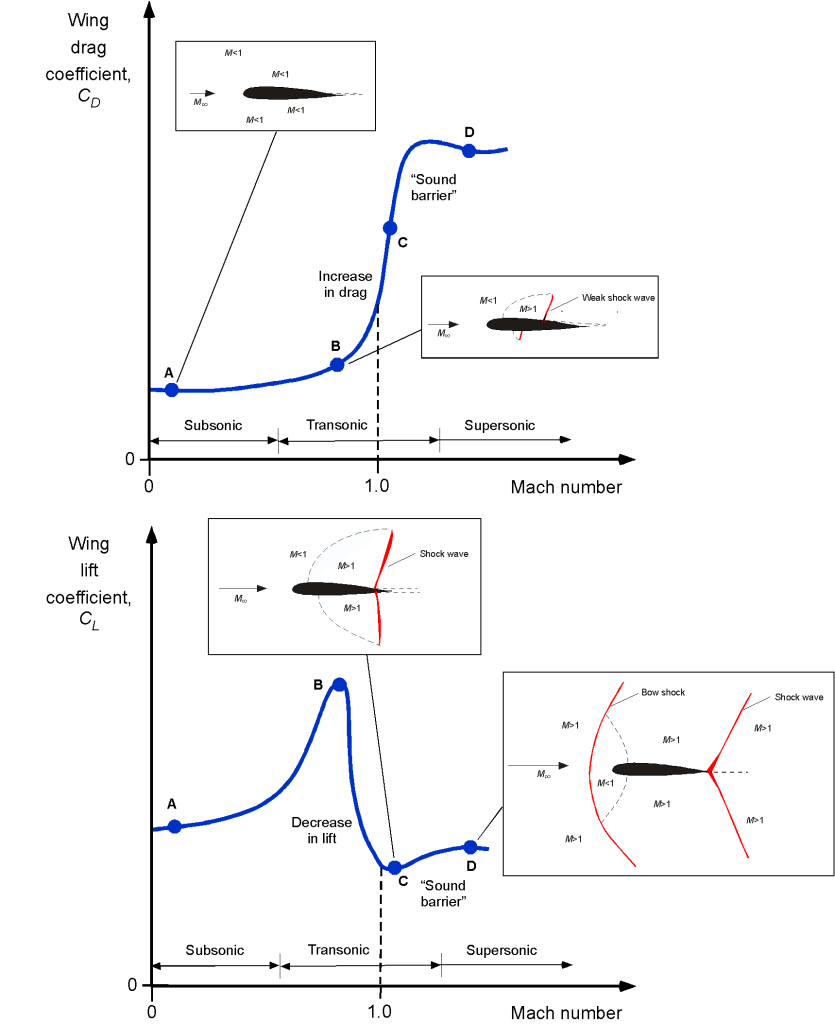
Because steep adverse pressure gradients also accompany the shock waves that develop during transonic conditions on the wing section, the boundary layer downstream of the shock wave becomes thicker, resulting in increased profile drag. If the shock wave becomes sufficiently strong (intense), flow separation may occur at the foot of the shock, leading to a buffeting aerodynamic phenomenon. Buffeting can result in high levels of vibration transmitted to the airframe, especially the tail structure, and it is not a sustained flight condition. The onset of buffeting can also cause aeroelastic concerns, so the possibility of this behavior must be scrutinized through flight testing. The onset of buffeting is usually a limiting factor in the operational flight envelope of most airplanes, unless they are designed for supersonic flight, and is referred to as the buffet boundary.
If and when the Mach number approaches unity, the shock waves move to the trailing edge of the wing section. Finally, when the Mach number exceeds one, a bow wave appears just ahead of the wing section, and the shock waves at the trailing edge become oblique. For supersonic airplanes, these strong shocks are responsible for the pressure changes heard on the ground, manifesting as the impulsive “boom-boom” sound, known as the sonic boom, as the airplane passes overhead at supersonic speeds. The drag rise on the aircraft during the transition from transonic to supersonic flight typically requires an excess of thrust to be produced using an afterburner. Some aircraft may be able to cruise supersonically without using the afterburner, but this depends on the engine. Concorde, for example, could cruise supersonically without the use of afterburners because it employed a unique variable geometry inlet design to increase the pressure entering the engine.
Reducing Compressibility Drag
The minimization of wave drag on the wings as the transonic flight regime is approached is crucial for reducing drag and/or allowing the airplane to fly faster, thereby expanding the flight envelope before significant drag rise is encountered. Additionally, lower drag means that less thrust and power are required for flight, resulting in less fuel consumption and increased flight range.
Swept Wings
The figure below illustrates that wing sweep has a profound impact on transonic and supersonic drag. This characteristic is because of the use of swept-back wings, which reduce the strength of the shock waves and prevent them from interfering with the flow over the wings, thereby preventing flow separation and drag. However, although swept wings can help delay the rise in drag from compressibility effects, other aerodynamic and aeroelastic problems are associated with swept wings. Therefore, aircraft designers tend to use as little wing sweep as possible, with 20 to 30 degrees being typical of many airliners.
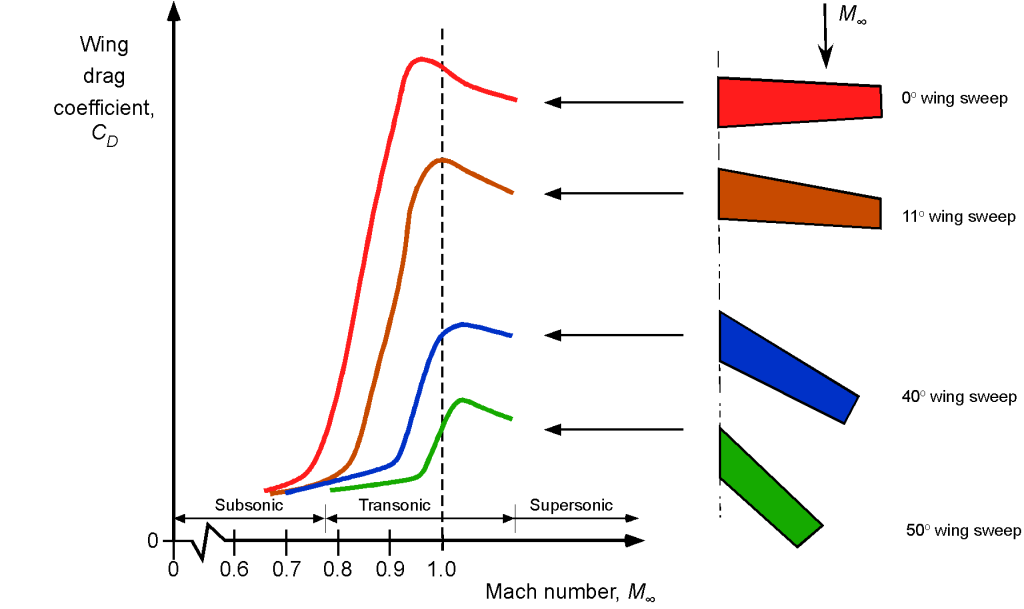
- Below is a visualization of the flow around swept and unswept wings at a low supersonic speed, obtained using the schlieren flow visualization method. The circular images from the spherical mirrors always indicate the use of schlieren. Notice that with sweepback, shockwaves do not interact directly with the wing, which keeps the drag low. However, with the unswept wings, the shock waves are stronger and interact more strongly with the wing, causing a loss of lift and flow separation that increases drag.
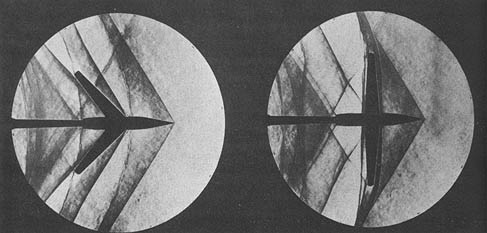
Airfoil Sections
The figure below shows the difference in the shapes of a conventional airfoil and a supercritical airfoil. The basic principle in transonic airfoil design is controlling the flow’s expansion to supersonic speed and subsequent recompression. Compared to a conventional wing section, a supercritical wing section is distinctive in that it is much flatter (i.e., less cambered) along the top surface but with significantly more camber at its trailing edge. Variations of supercritical airfoil sections are used on all commercial jet airliners.
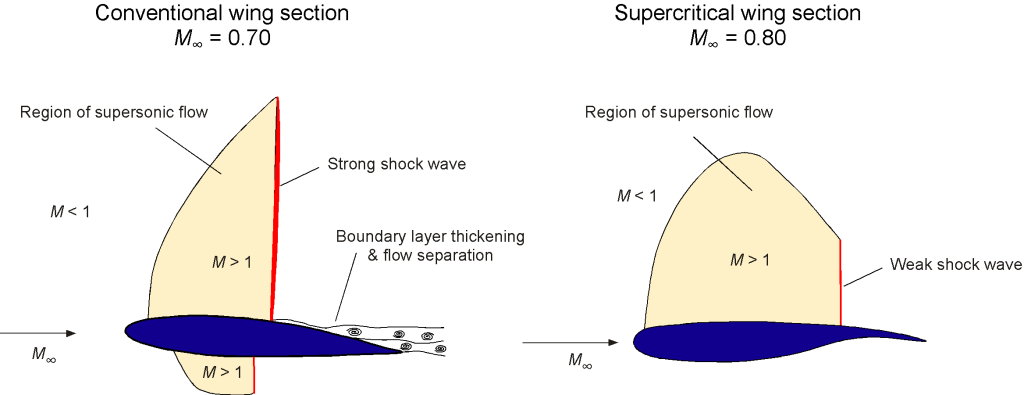
The challenges in reaching higher transonic cruise speeds have led to the design of a unique swept wing shape, known as a supercritical wing. The supercritical wing evolved from the careful tailoring of the airfoil section(s) in conjunction with the overall wing design to delay the formation and reduce the strength of shock waves over the wing, thereby reducing wave drag. In the early 1970s, NASA achieved great success by modifying an airplane (see photo below) to test a supercritical, crescent-shaped planform wing, which replaced the conventional wing, thereby minimizing the effects of shock waves and wave drag. The results of NASA’s supercritical wing research indicated that aircraft utilizing this concept were expected to achieve improved performance. Delaying shock wave formation at these higher speeds resulted in less drag, significantly increased cruising speed, and improved fuel efficiency. Since then, aircraft designers have never looked back.
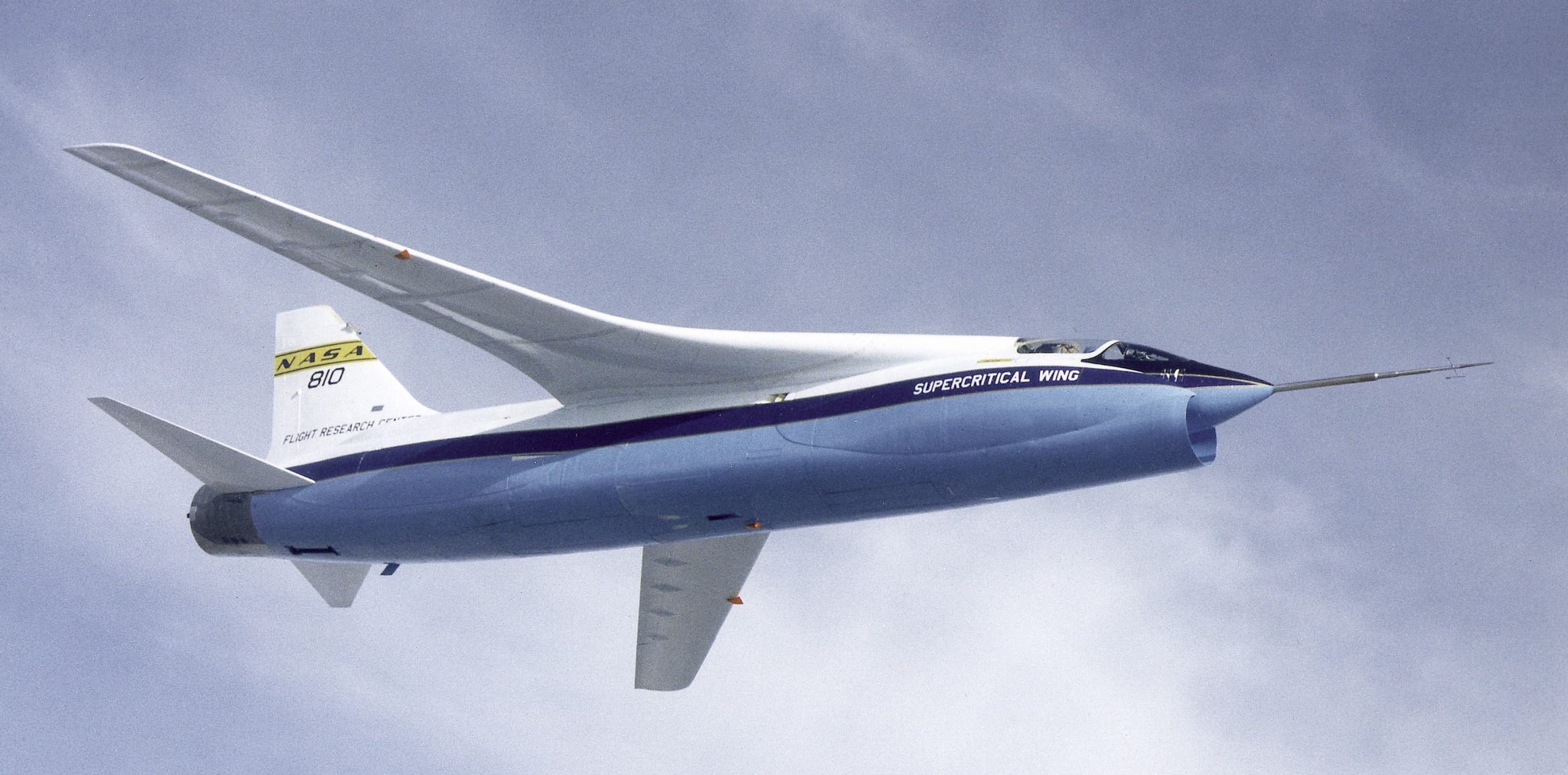
Area Rule
Other ways of reducing wave drag and expanding the airplane’s flight envelope to higher cruise speeds include using the area rule, which Richard Whitcomb developed. The basic design principle behind the area rule is that the airplane’s overall cross-sectional shape should change smoothly with no significant discontinuities to reduce the number and intensity of shock waves over it as it approaches transonic and supersonic flight.
The principle was proven to work in wind tunnel testing, as shown in the photograph below, and then applied retroactively to various airplanes, with successful results after flight testing. Early airplanes modified to validate the area rule had distinctive, if not odd-looking, “waisted” fuselage shapes at the wing root, as shown in the figure below, which were often referred to as “flying Coke bottles.” Nevertheless, the notable reductions in drag proved the viability of the area rule concept.
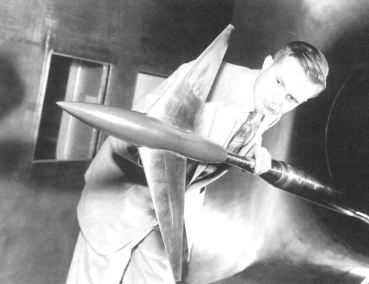
Later, airplanes were designed with the area rule in mind. They were aesthetically more pleasing because of the blending of the wing root area and the careful positioning of the engines, the use of sizable trailing edge anti-shock wing pods or “canoe” fairings. Other, more subtle changes to the shape of the airplane were used to prevent significant changes in effective cross-sectional area. In addition, for many commercial airliners, the wing-mounted “pod” engines are placed relatively far forward from the wings to control the change in the cross-sectional area of the airplane at the wing.
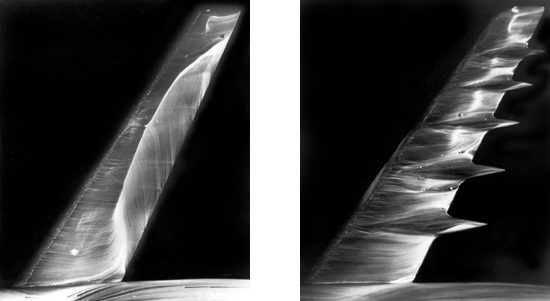
A careful examination of most commercial airliners reveals some careful contouring of the fuselage and wing root, designed to minimize wave drag according to the principles established by the area rule. For the same reason, later versions of the Boeing 747, such as the 800 series, were also modified with an extended upper deck and a shallower transition at its end to keep area changes as progressive as possible.
Most airplanes capable of transonic or supersonic airspeeds incorporate design features that can be traced back to the fundamental principles underlying Whitcomb’s area rule. For example, the three orange pods or “canoe fairings” shown in the photograph below are hollow fiberglass fairings that streamline the flap track and actuator mechanisms. However, they are oversized to progressively reduce the cross-sectional area of the aircraft behind the wing and decrease transonic drag, as per the area rule.
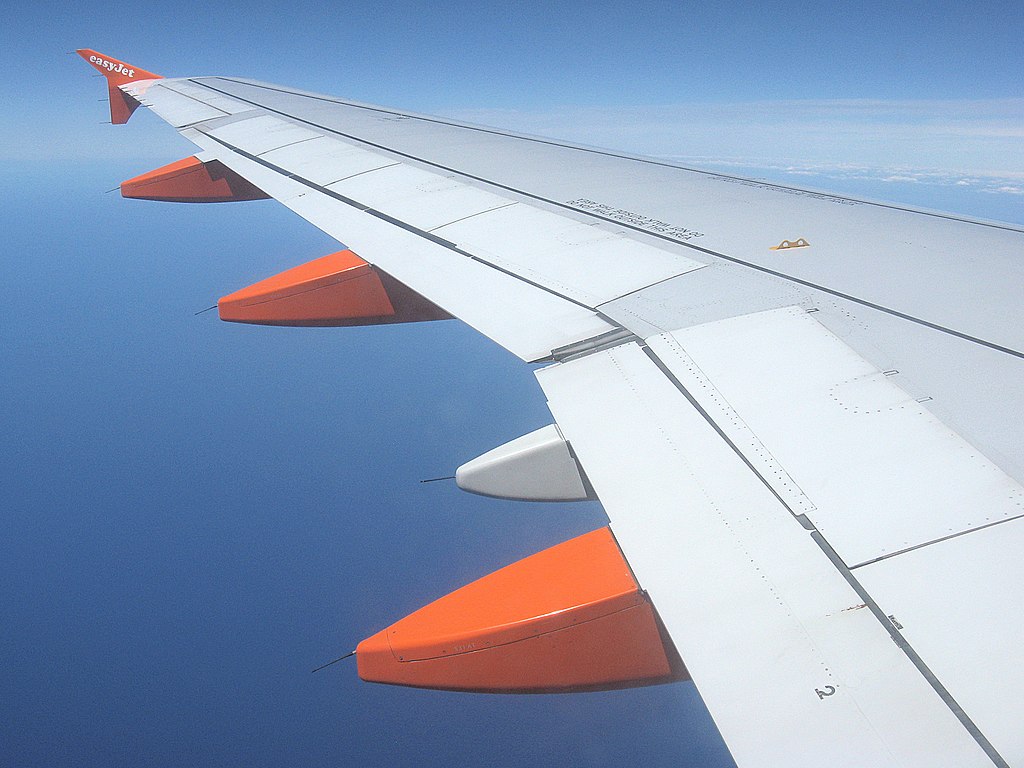
Crescent Wing
One of the wing designs that stands out for its excellent high subsonic and transonic performance is the crescent wing. The figure below shows that crescent wings have smoothly varying wing sweep angles, the sweep angle being highest at the root and then decreasing toward the wing tip. The crescent wing design is an excellent aerodynamic solution for delaying the onset of wave drag and allowing the aircraft to cruise at higher transonic flight Mach numbers.
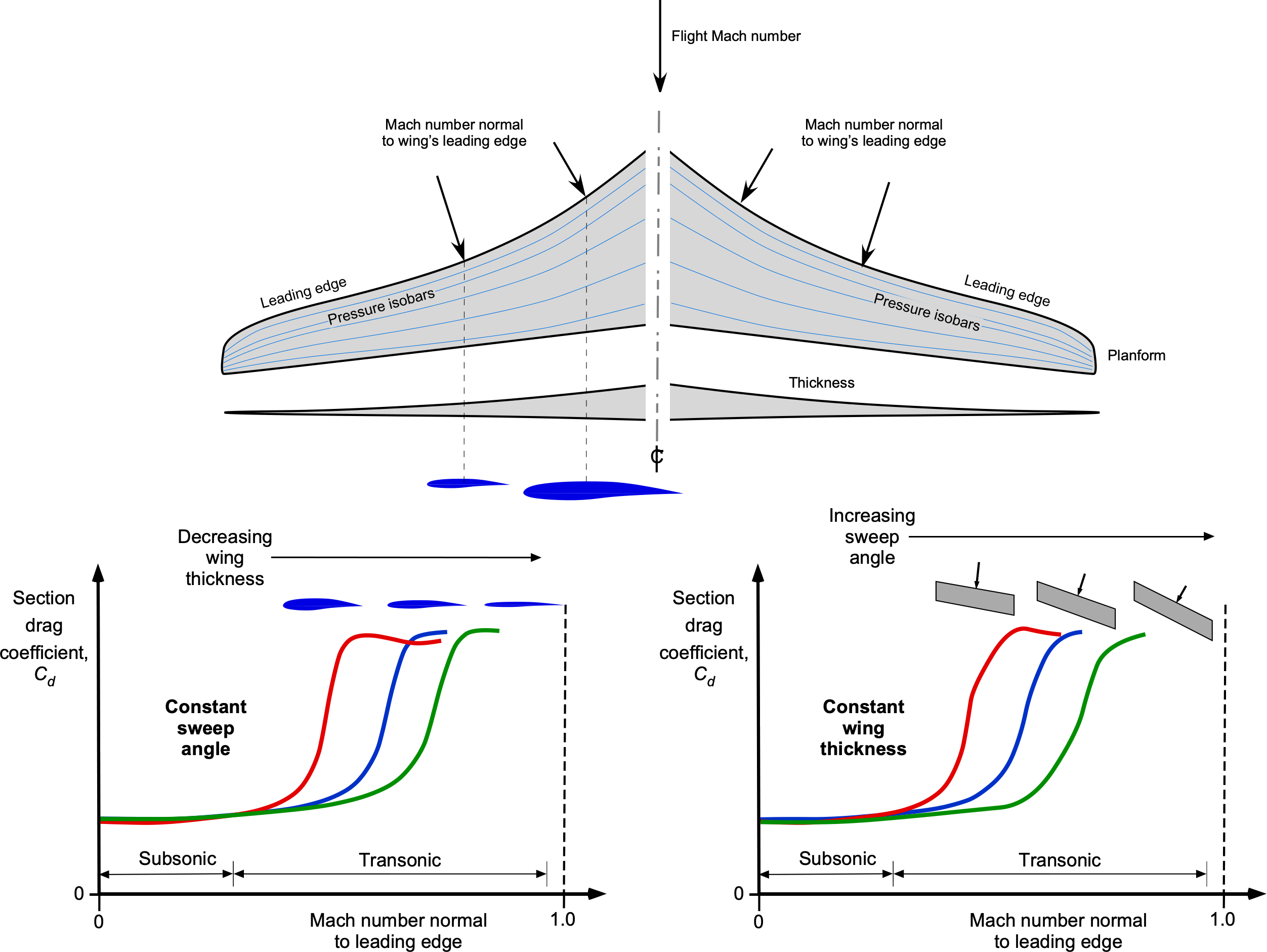
The crescent wing’s design follows the supercritical design philosophy, which aims to delay the onset of drag rise as much as possible. Notice the rapid reduction in wing thickness approaching its tip, which is relatively thin. The structural bending moment on a wing increases toward the wing root with the square of the distance from the wing tip. Therefore, limiting bending stresses necessitates increased wing thickness, which will be roughly proportional to the magnitude of the moment. Wing thickness may also be needed to house the propulsion system and/or landing gear. However, this leads to a problem: the wing thickness at the root becomes so high that it significantly reduces the critical Mach number of the wing. Consequently, the onset of transonic drag rise will occur at a lower flight Mach number.
The crescent wing attempts to maintain the highest possible cruise Mach number for a given wing thickness by altering the local sweep angle. This approach sweeps the wing more with increasing sectional thickness, maintaining or reducing the Mach number normal to the wing’s leading edge, and pressure isobars. The idea is to improve the sweep angle just enough to offset the detrimental effects of increased sectional wing thickness. In addition, because there is a super-velocity and corresponding Mach number produced at the ing root by the fuselage, the additional sweep angle also offsets this effect. While the principle is aerodynamically attractive, such a wing is more complicated and expensive to manufacture. Therefore, there have been few aircraft built with crescent wings.
One notable exception was the British Handley Page Victor strategic bomber, a significant component of the West’s nuclear deterrent during the 1950s and 1970s. The Victor’s distinctive feature was its almost crescent-shaped wing, which gave it a sleek appearance and excellent aerodynamic performance with cruise Mach numbers of about 0.9. Its high-mounted T-tail also followed the same supercritical design philosophy. The Victor was one of the three “V-bombers” designed by the British aircraft companies Handley-Page, Vickers, and Avro. A careful examination of the wings on both the Vickers Valiant and the Avro Vulcan will also reveal the incorporation of certain supercritical design features; the Vulcan essentially has the “delta” equivalent of the crescent wing.
Flight Ceilings
The flight ceiling for an airplane is defined based on a demonstrated rate of climb. The absolute ceiling is determined when the achievable rate of climb diminishes to zero, whereas the service ceiling is defined as the rate of climb that reduces below 100 ft/min. The airplane’s standard performance ceiling is when the climb rate reduces below 200 ft/min. The ceiling is reached when the excess power available, over and above that required for level flight at the same airspeed and weight, becomes diminishingly small.
The ceiling for most commercial transport airplanes is limited by cabin pressurization requirements rather than attainable engine thrust and power, which sets a structural stress limit on the fuselage. For most airplanes, the cabin pressure is maintained at an altitude equivalent to approximately 6,000 to 8,000 feet, allowing for good passenger comfort. Nevertheless, some passengers may still exhibit hypoxia symptoms (oxygen deprivation) during extremely long flights over 12 hours, contributing to the disorder known as jet lag. Therefore, the most modern commercial transport airplanes, such as the Boeing 787, maintain cabin pressure at an equivalent altitude of 6,000 ft (i.e., at a higher pressure differential), thereby improving passenger comfort and reducing the effects of jet lag.
Representative Flight Envelopes
The general idea of a flight envelope has already been introduced, although now, having learned about the specifics of airspeed and Mach number, stalling, transonic drag rise, and the thrust/power required for flight, the characteristics of the flight envelope of an airplane and why it has inherent boundaries can be better understood. Stalling speeds always define the low-speed end of the envelope, and the onset of transonic drag rise and buffet will define the high-speed end of the envelope. As previously explained, the ceiling is often determined by the allowable differential pressurization, which is a structural limit, not an aerodynamic one.
A representative flight envelope for a commercial subsonic transport (jet) airplane is shown in the figure below, with measured test points also being identified. In this case, the graphs are defined in terms of airspeed and the flight Mach number, the significance of which has already been discussed. At lower airspeeds, the envelope is bounded by the stalling speeds in the “clean” configuration. The stall region of the flight envelope requires little further elaboration, as it is a complex aerodynamic region involving flight at low airspeeds and high angles of attack, which also depends on the airplane’s configuration, such as whether flaps are up or down, landing gear is up or down, and so on. The stall boundary is always defined carefully during flight testing. Typically, numerous tests are conducted to establish reasonable confidence that the stall boundary, handling qualities, and other aircraft characteristics at the stall have been thoroughly explored for all flight combinations (e.g., weights and altitudes).
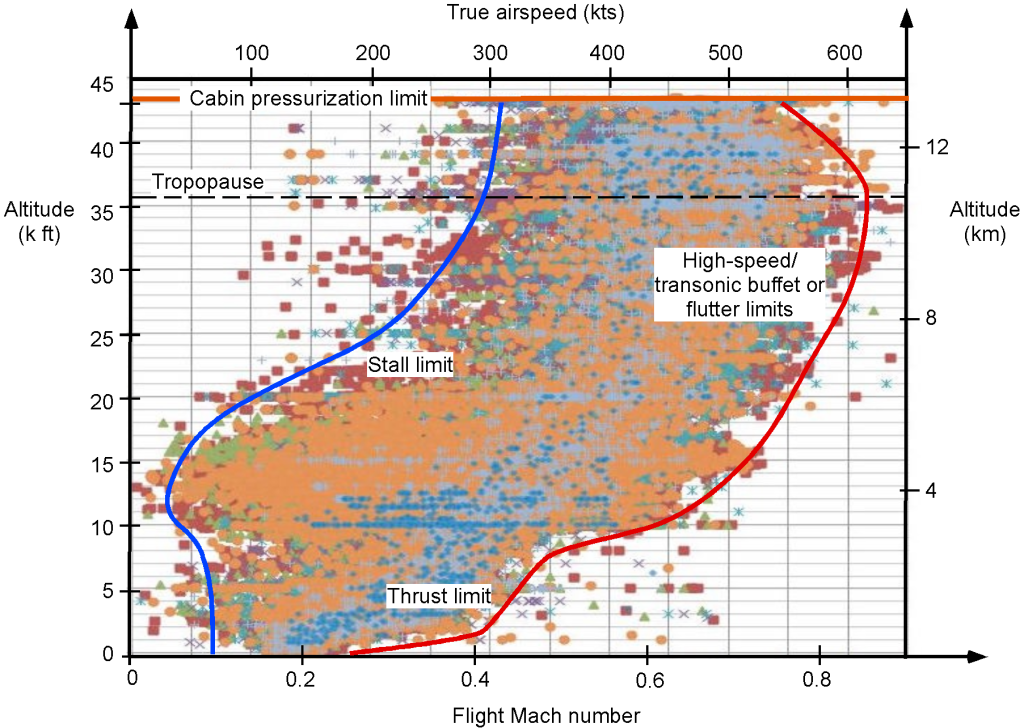
At higher airspeeds, the limits of flight are dictated by the maximum operating Mach number, which is called , with the corresponding airspeed being called the maximum operating airspeed
or VMO. In operational service, the airplane will cruise at an airspeed somewhat lower than the recommended airspeed, as specified in the airplane’s operating manual and procedures.
While fundamental engineering issues are critical, non-engineering factors may limit the usable flight envelope. For example, problems often center on financial requirements, manufacturability, passenger ergonomics and safety, airfield requirements, and environmental and noise regulations. For example, an airline always wants to maximize its profit; in this respect, the airplane’s empty weight is critical. The benefit is that not only is the fuel burn lower (i.e., lower costs for a given payload), but the revenue can also be increased by carrying more payload. One reason lightweight composite materials have become critically important in modern aircraft design is the need to carry more payload. This is not because composites are necessarily lighter per se, but because they can be better tailored to give a better strength-to-weight ratio.
The figure below illustrates the flight envelope of high-performance jet airplanes, which can reach nearly supersonic flight speeds, particularly at higher altitudes. In this case, the envelope was established again using flight test data, which included various types of maneuvers, such as accelerations, decelerations, climbs, and descents. Notice this airplane’s relatively broad flight envelope regarding attainable altitudes and airspeeds (Mach numbers). However, such high-performance airplanes tend to expose the limits of aeronautical technology, which are closely tied to the limitations imposed by aerodynamics, the strength of the airframe, and the engines.
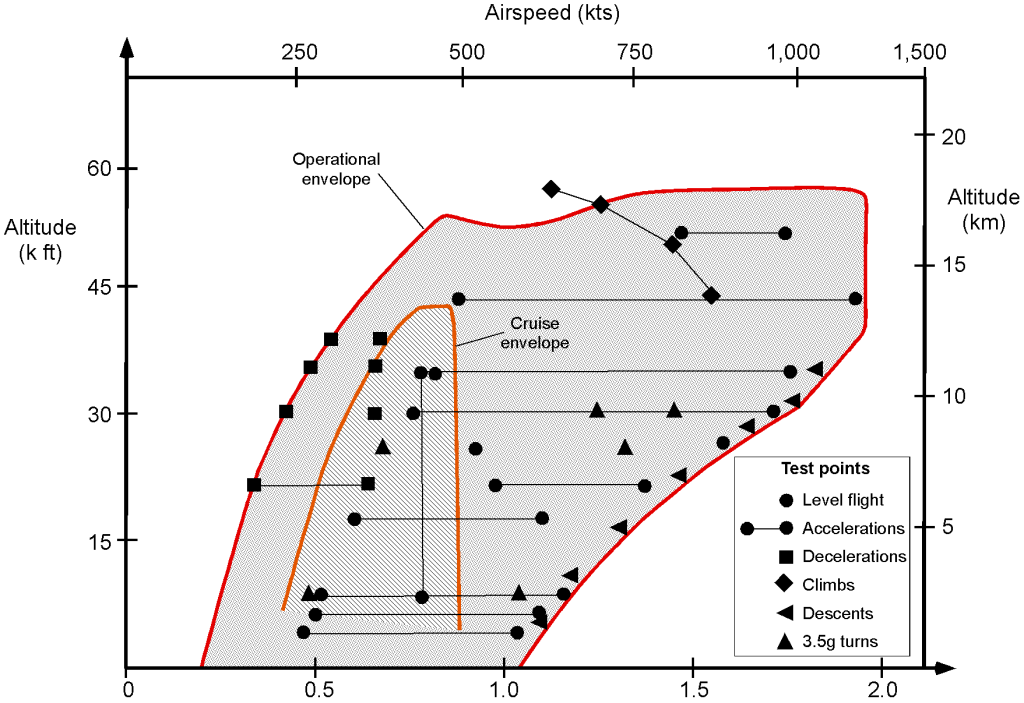
Other Possible Limiting Factors
Engine limitations and aeroelastic effects may impact the flight envelope of airplanes, including airliners. Engines impose thrust and power limits, efficiency constraints at higher altitudes, temperature restrictions, and maintenance requirements to ensure reliability and performance. Aeroelastic effects, such as flutter, divergence, and control reversal, involve instabilities that can lead to structural deformation and failure. These phenomena require careful design considerations and will set critical speed, altitude, and load limits to ensure safe and efficient aircraft operation.
Engine Limitations
The engines themselves may suffer from various problems that limit the airplane’s flight boundary, including surge/stall issues and intake buzz. Intake “buzz” is usually associated with supersonic airplanes, which have inlets designed to reduce the flow speeds to subsonic conditions before the flow enters the engine’s compressor stage. If it occurs, the buzz phenomenon involves the interaction between the surface boundary layer flows and the shock waves, which can result in an erratic flow behavior at the intake to the engine.
Engine surges can occur on all jet engines when a stall manifests in the compressor stage. However, the onset is usually precipitated by operating the aircraft at an excessive angle of attack, especially when flying at lower airspeeds, e.g., during takeoff. The phenomenon results in sudden back pressure through the engine, leading to unstable engine operation. In some cases, the combustion process is interrupted, allowing raw fuel to burn in the tailpipe, often resulting in a spectacular series of “bangs” accompanied by the discharge of smoke and flames.
While serious in that surges cause an immediate loss of thrust, they are usually quickly self-correcting when the conditions that promoted the problem are removed, i.e., by the pilot reducing the angle of attack of the wing and/or increasing airspeed by pushing forward on the control stick. Nevertheless, engine surge conditions have been known to manifest more often during the critical takeoff and climb phases of flight, which always pose a safety-of-flight issue. Usually, an engine that suffers from surging or stalling must be closely inspected for damage before further flight, especially the hot sections of the engine.
Aeroelastic Effects & Flutter
Aircraft are flexible structures, and significant structural deformations can occur even during routine flights. Wing flutter is an aeroelastic phenomenon, a coupling between the aerodynamic loads and the elastic deformation of the structure. Wings and tail surfaces are prone to flutter at higher airspeeds and Mach numbers, although other parts of the airframe, such as the engine nacelles and tail surfaces, may also be susceptible to such problems. Even on a wing, the onset of flutter is not necessarily catastrophic and can manifest as benign (but often alarming) limit-cycle torsional and/or bending oscillations.
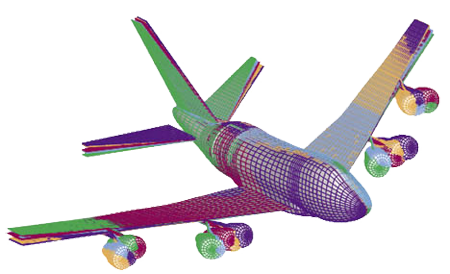
Generally, however, avoiding flutter is a crucial design requirement. Therefore, the structural dynamics and potential flutter characteristics of the aircraft’s structure are carefully examined using computer models to identify the natural frequencies and modes of deformation, as shown below. The parameters that may affect the onset of flutter on a wing include the geometry of the wing (its span, aspect ratio, thickness, sweep angle, etc.) as well as its structural stiffness, total weight, and weight distribution, positions and weights of the engines, moments of inertia about the bending and torsional axes, etc.
However, flutter developments can still occur even with a good understanding of the flexible airframe. Flutter typically results in significant structural deformations and, in some cases, structural failure. Because the onset of flutter conditions on an airplane can be potentially catastrophic, wings, in particular, are carefully designed to avoid the problem and verified through flight testing to ensure that flutter will never occur if the airplane is flown within its standard, validated flight envelope.
Summary & Closure
While all aircraft have an operational flight envelope defined by specific airspeeds and altitudes for safe operation, not all aircraft are designed equally. The advent of the supercritical airfoil and its subsequent evolution into the supercritical wing have revolutionized the design of commercial jet aircraft. Supercritical airfoils are characterized by their distinctive flat top surfaces, which are easily recognizable on modern jetliners. This innovation has significantly expanded the flight envelope of airliners and other high-speed, transonic aircraft, enabling them to cruise more efficiently at higher speeds and altitudes. The improved aerodynamics of supercritical wings reduce drag and delay the onset of shock waves that occur near the speed of sound, improving fuel efficiency and performance.
In addition to the supercritical wing, the application of the area rule has further advanced aircraft design. The area rule is a principle that minimizes wave drag, which is a significant source of aerodynamic drag at transonic and supersonic speeds. Engineers can reduce drag and improve efficiency at higher transonic Mach numbers by designing aircraft with a smooth distribution of cross-sectional area along their length. Together, these innovations, i.e., the supercritical wing and the area rule, have set new standards in the design and performance of modern subsonic commercial airliners, making them more efficient, faster, and capable of operating safely over a broader range of conditions.
5-Question Self-Assessment Quickquiz
For Further Thought or Discussion
- Think about the nature of the flight envelope for a small, general aviation airplane powered by a reciprocating engine and propeller. What factors limit the maximum flight speed, maximum altitude, and minimum airspeed?
- What factors will limit a turboprop airplane’s lowest and highest achievable airspeeds?
- What is the operational flight envelope of a typical helicopter compared to that of an airplane? A tiltrotor?
- Study photos you can find of the Airbus A380. Can you identify any design features that relate to the use of the “area rule” in its design?
- What type of flight envelope would a supersonic transport (SST) aircraft have? What factors will or may limit the highest achievable flight Mach number?
Other Useful Online Resources
To learn more about aircraft flight limitations, check out some of these online resources:
- An older but interesting educational film discussing high-speed flight.
- Great video showing the stall patterns on the wing of a general aviation (GA) aircraft.
- Video of stalling a Boeing 737-400.
- National Aerospace Library educational film series:
- To learn more about the supercritical airfoil, refer to this NASA article.
- The story of the area rule.
- NASA video – Aviation Pioneer Richard Whitcomb.
- Lecture by Richard Whitcomb.
- Stall testing the MD-11.
- Boeing 787 Dreamliner stall tests.
- Video of flutter testing.
- Video of the structural deformations on a Boeing 747 when flying through turbulence.
- Video of wing flex on a Boeing 737 wing.